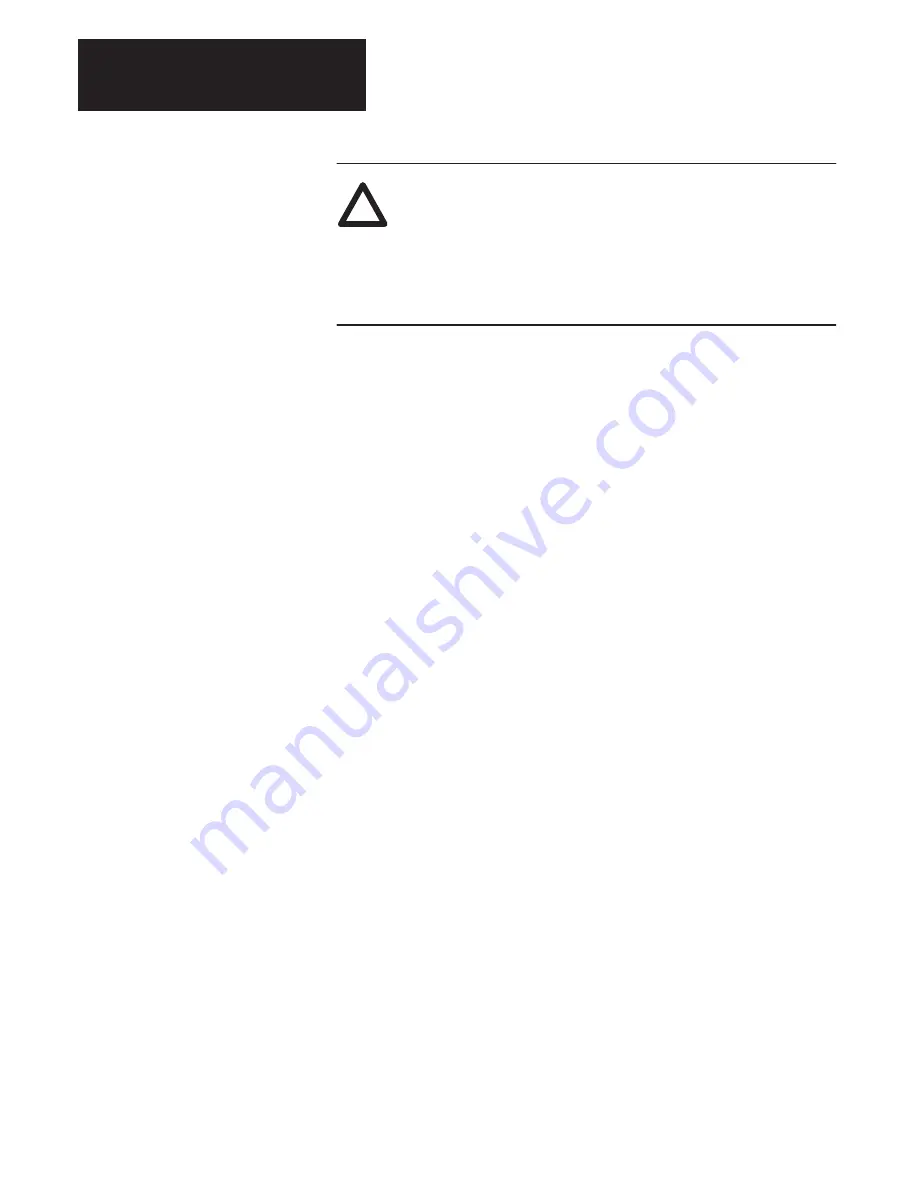
Chapter 8
Start-Up
8-4
ATTENTION: In the following steps, reverse rotation or
uncontrolled rotation at high speed can occur. Be prepared to
remove drive power by opening (MCB) or the branch circuit
disconnect device if this occurs. This movement may be due to
a wiring error or system component malfunction and must be
corrected before proceeding. Damage to machine system
components can occur due to uncontrolled machine movements.
!
13.
The drive will display the message “DANGER, MOTOR MAY
RUNAWAY!!” Be prepared to open MCB on the drive if the motor
does not run correctly (under this condition the motor current limit is
set to 25% of rated current to minimize motor speed) – press Enter
to continue.
14.
The display will now read “enable to strt rotation test.”
Energize the contactor (M) and enable the drive.
A correctly wired drive will rotate the motor clockwise at 30 rpm for
5 seconds – stop for 2 seconds – then rotate the motor
counterclockwise for 5 seconds – then stop.
If the motor runs away or does not rotate, verify all power and
resolver wiring.
15.
The display will now read “disable drive to continue.” Disable the
drive by opening the Enable input, leaving the contactor energized.
Display: “press enter to exit motor test” – press Enter.
16.
The display will now read “zero analog velocity offset” – press
Enter.
In this mode the drive will automatically adjust out any offset, while
the motor remains at zero speed. When the display reads: “enable to
strt zero vel offset,” apply the Enable input to the drive.
The display will now read “jumper analog velocity inputs.” Jumper
TB2-1 to TB2-2. This applies zero volts to the velocity inputs. Press
Enter to continue.
The display will now read “now zeroing velocity offset.” The drive
can take up to 60 seconds to zero the offset. If zeroing was
successful, the display will show “velocity zero complete.” Remove
the jumper and press Enter.
Important: If for some reason the offset cannot be adjusted, the
message “cannot zero velocity offset” will be displayed. If this
occurs, verify that the jumper connections are correct and continue
on with the procedure. After completion, do a manual zero speed
adjustment as explained in step 32.
The display will now read “disable drive to continue” – Remove
enable, leaving the contactor (M) energized.
Summary of Contents for ALLEN-BRADLEY 1391-DES
Page 1: ...User Manual 1391 DES Digital AC Servo Drive...
Page 9: ...Chapter 1 Introduction 1 10 End of Chapter...
Page 37: ...Chapter 5 Inputs Outputs and Switch Settings 5 8 End of Chapter...
Page 84: ...Chapter 8 Start Up 8 16 End of Chapter...
Page 88: ...Chapter 9 1326 AC Servomotors 9 4 End of Chapter...
Page 106: ...Chapter 11 Troubleshooting 11 12 End of Chapter...
Page 122: ...Appendix B Interconnect Drawings B 12 End of Appendix...
Page 126: ...Appendix C Cable Information C 4 End of Appendix...
Page 134: ...Appendix E Parameter Record E 8 End of Appendix...
Page 135: ...Notes...
Page 136: ...Notes...
Page 137: ...Notes...
Page 138: ...Notes...
Page 139: ...Notes...
Page 140: ...Notes...
Page 141: ...Notes...
Page 142: ...Notes...
Page 143: ...Notes...
Page 144: ...Notes...
Page 147: ...IMC is a trademark of Allen Bradley Company Inc...