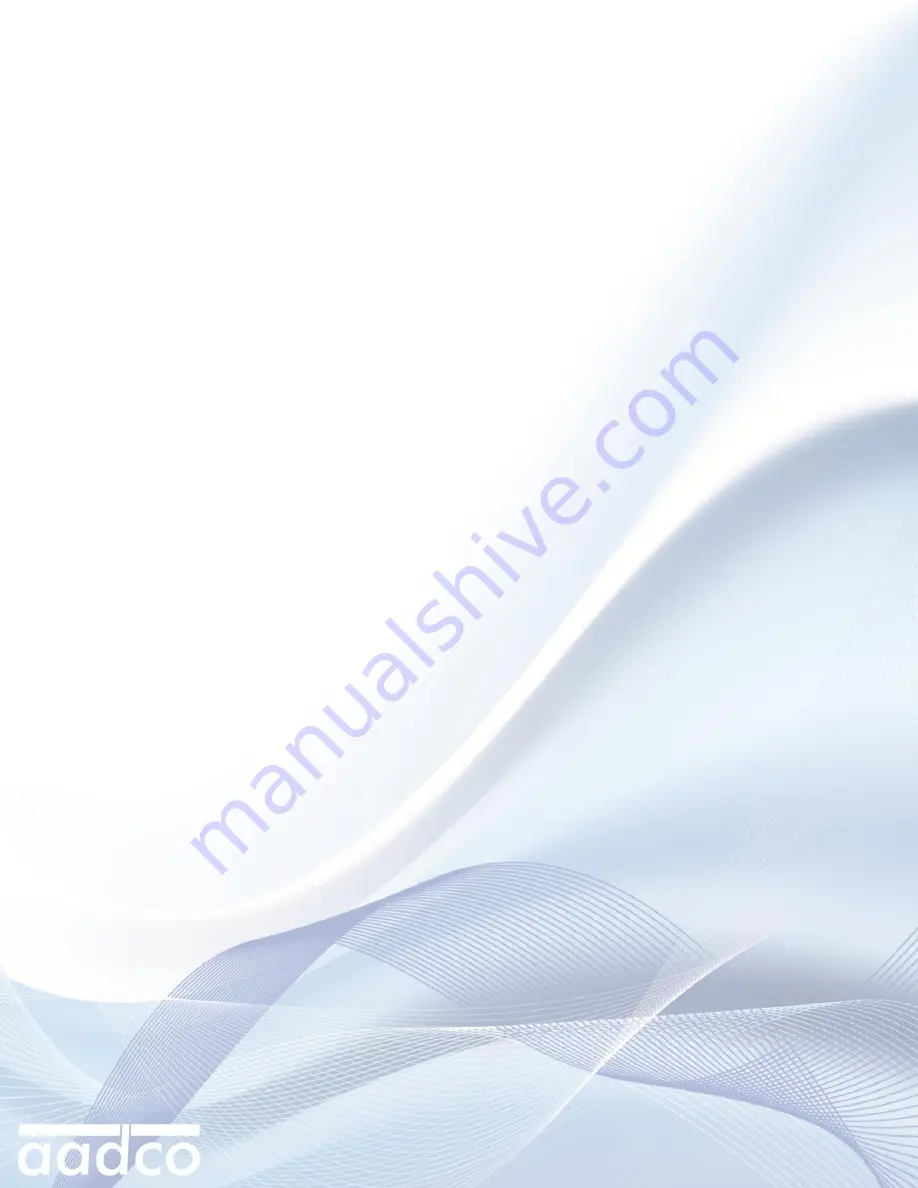
38
15.0
COMPONENT REPLACEMENT
15.1
TO REPLACE THE PURIFICATION REACTOR:
(a)
REMOVE THE POWER CORD FROM THE WALL OUTLET
and
disconnect the two electrical disconnects leading to the solenoid valves of
the purification reactor.
(b) Disconnect the ¼-inch stainless steel tubing at the inlet of the purification
reactor, allowing the stainless steel tubing and all of its connecting tubing
to remain suspended.
(c) Disconnect and remove the ¼-inch tubing leading from the output of the
purification reactor to the input of the OUTPUT PRESSURE
REGULATOR, Figure 6 (5), unless mixer-receivers, Figures 7, 7a, and 11
(49), are incorporated in the unit, in which case, the tubing will be that
which is connected between the output of the purification reactor and the
rear mixer-receiver.
(d) Remove the two 10-32 screws on the underside of the generator cabinet
which hold opposite corners of the purification reactor.
(e) Disconnect the ¼-inch tubing leading to the DUMP connection on the rear
wall of the generator unit.
(f)
It may be necessary to remove the mixer-receivers, if present, to gain
access to the connection on the purification reactor.
(g) Lift the defective purification reactor from the generator unit.
(h) To install new purification reactor reverse procedures (a) through (f). It is
not necessary to make any flow adjustments with the new purification
reactor since all adjustments will have been made at the factory. Be
certain to leak check all connections.
15.2
TO REPLACE THE METHANE REACTOR:
(a)
REMOVE THE POWER CORD FROM WALL OUTLET
and disconnect
the red, white and black leads at the terminal strip, noting connections for
new methane reactor leads, and the two-conductor thermocouple quick-
connect between the pyrometer and the methane reactor.
(b) Disconnect and remove the cooling coil.
(c) Disconnect the ¼-inch tubing leading from the output of the rotameter to
Summary of Contents for 737 Series
Page 4: ...v 20 737 10 ROTAMETER FLOW NOMOGRAPH 62 ...
Page 11: ...7 3 16 Follow the procedures as outlined in Section 3 7 through Section 3 13 ...
Page 36: ...32 defective check valve ...
Page 48: ...44 ...
Page 49: ...45 ...
Page 50: ...46 ...
Page 51: ...47 ...
Page 52: ...48 ...
Page 53: ...49 ...
Page 54: ...50 ...
Page 55: ...51 ...
Page 56: ...52 ...
Page 57: ...53 ...
Page 58: ...54 ...
Page 59: ...55 ...
Page 60: ...56 ...
Page 61: ...57 ...
Page 62: ...58 ...
Page 63: ...59 ...
Page 64: ...60 ...
Page 65: ...61 ...
Page 66: ...62 ...
Page 67: ...63 ...
Page 68: ...64 ...
Page 69: ...65 ...
Page 70: ...66 ...
Page 72: ...68 ...