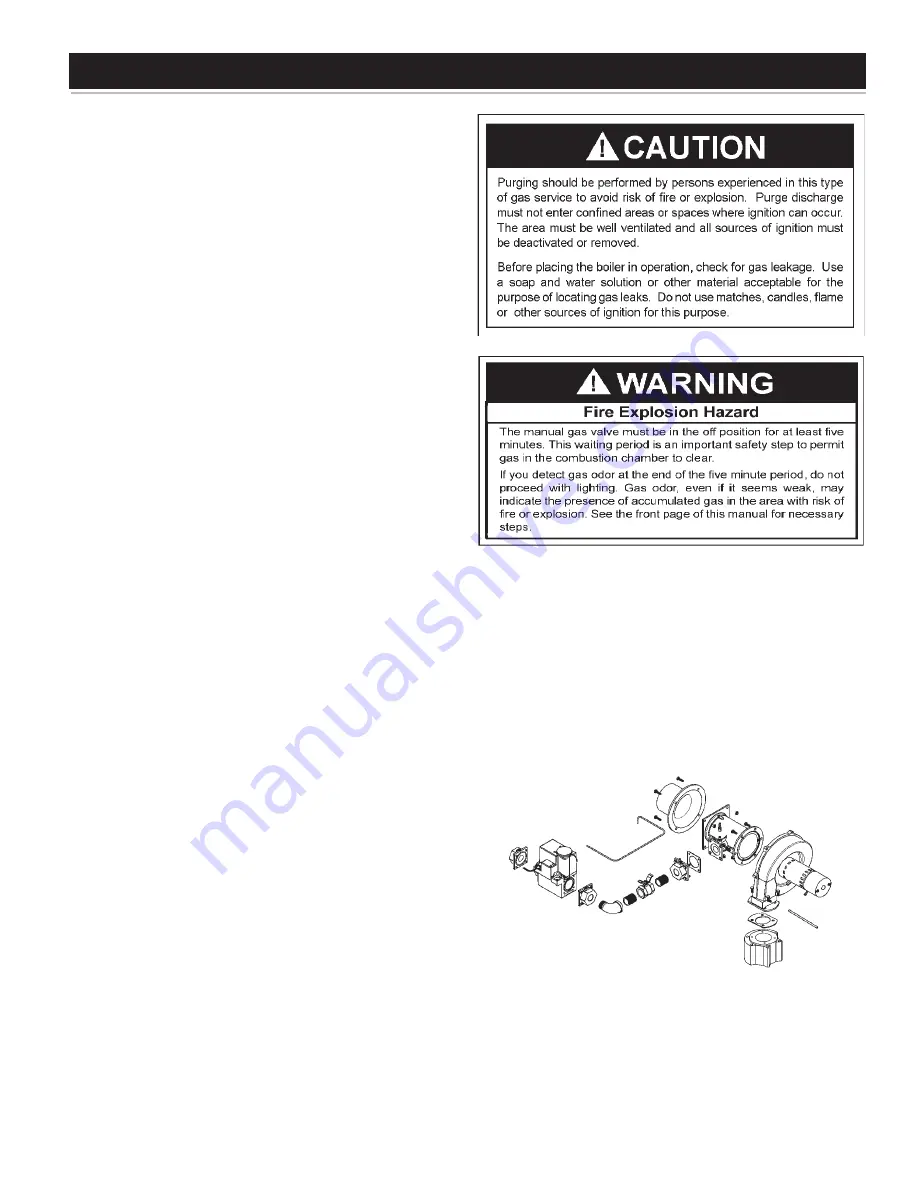
33
OPERATION
IMPORTANT
Only qualified personnel shall perform the initial firing of the boiler.
At this time the user should not hesitate to ask the service agent
any questions regarding the operation and maintenance of the unit.
If you still have questions, please contact the factory or your local
A.O. Smith representative.
Lighting and Operating instructions are included with this manual.
By using these instructions, the user may be able to make minor
operational adjustments and save unnecessary service calls.
However the user should not attempt repairs, but should contact
a service technician or gas supplier.
GENERAL
Never operate the boiler without first making sure the boiler and
system are filled with water, in addition:
For hot water supply installations:
• Make sure a temperature and pressure relief valve is installed at
the boiler and, if used, the storage tank. Also check for leaks.
For heating boiler installations:
• Make sure that the boiler and system have been purged of air
and checked for leaks.
Also be sure to check the gas piping for leaks before beginning the
initial firing of the boiler.
FILLING AND PURGING OF HEATING BOILER
INSTALLATION
1. Fast fill system through bypass until pressure approaches
desired system pressure. Close bypass valve and permit
pressure to be established by the pressure reducing valve.
2. Vent all high points in system to purge system of air.
Provisions should be made to permit manual venting of radiators
or convectors.
FILLING HOT WATER SUPPLY BOILER
INSTALLATION
1. Close the system’s drain valve by turning handle clockwise.
2. Open a nearby hot water faucet to permit the air to escape.
3. Fully open the cold water inlet pipe valve allowing the boiler
and piping to be filled.
4. Close the hot water faucet as water starts to flow.
5. The boiler is ready to be operated.
PURGING GAS LINE
Gas line purging is required with new piping or systems in which
air has entered.
INLET GAS PRESSURE
The inlet gas pressure is measured by removing the 1/8” NPT Plug
located on the main gas manifold which is upstream of the unit’s gas
valve, and insert a 1/8” NPT hose barb fitting to be connected to a
manometer or pressure gauge. Once pressure has been checked and/
or adjusted, replace the plug and check for leaks. The maximum value
specified in the table must not be exceeded. The minimum values,
shown in Table 1, must be maintained under both load and no load
conditions (static and firing conditions). The combination gas valves
supplied with the boiler are for low pressure service.
If upstream
pressure exceeds 14.0” W.C., an intermediate gas pressure
regulator of the lockup type must be installed.
FIGURE 19. GAS TRAIN ASSEMBLY.
Summary of Contents for VF VB 500
Page 3: ...3 GENERAL SAFETY...
Page 30: ...30 Wiring Diagram FIGURE 17 CONNECTION DIAGRAM...
Page 31: ...31...
Page 32: ...32 FIGURE 18 SCHEMATIC DIAGRAM VB VW 500 750 1000 SCHEMATIC DIAGRAM...
Page 36: ...36 LIGHTING OPERATION INSTRUCTIONS FOR MODELS VB VW 500 750 AND 1000...
Page 48: ...48 notes...
Page 49: ...49 notes...
Page 50: ...50 notes...