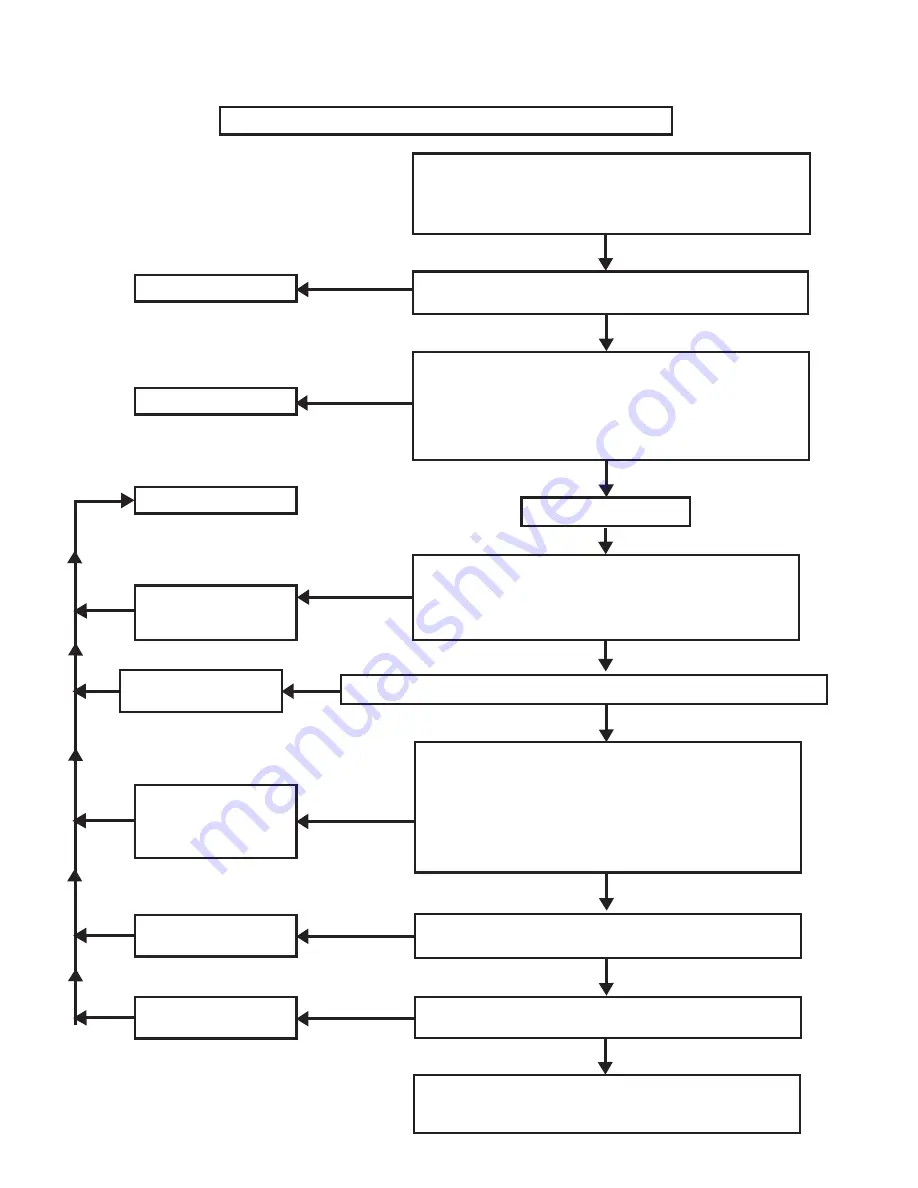
34
CHECKING HONEYWELL S-8600H OR S-8600M
INTERMITTENT IGNITION CONTROLS
SPARK AT PILOT BURNER BUT PILOT WILL NOT LIGHT
Ensure all manual shutoff valves are fully open; all filters are
clean; all gas connections are gas tight; pilot tubing is not damaged,
obstructed or kinked; and pilot orifice is unclogged. Check for air in gas
line, purge (bleed) line if necessary.
Are the wires securely attached to the pilot operator on the gas control
and to the PV & MV/PV terminals on the ignition module?
Install a pressure gauge in the pilot tubing line between the gas control
and the pilot burner assembly. Ensure that the pilot adjustment screw
(under cap) is adjusted to a position that will permit gas to flow.
Is pilot gas flowing during ignition attempt?
Turn off power supply.
Is ignition cable firmly plugged into pilot assembly and module?
Is ground wire firmly attached to pilot assembly and GND terminal on
module?
Are ignition cable and ground wire in good condition (not brittle, burnt, or cracked)?
Ensure ground strap is the closest metal to the igniter/sensor
rod (electrode) to prevent the spark from shorting out to
other metal parts (pilot screen, pilot shield, etc.).
Ignition cable must not touch metal surfaces or current
carrying wires.
Is there a 1/8” gap between ground strap and electrode?
Is ceramic insulator surrounding the electrode in good
condition (not cracked or broken)?
Is there excessive draft conditions that may cause pilot
burner ignition problems?
Correct draft problems in a manner that would ensure
adequate combustion and ventilation air and proper
pilot burner performance.
YES
YES
YES
YES
YES
YES
YES
NO
NO
NO
NO
NO
NO
NO
Attach wires firmly.
Replace gas control valve.
Turn on power supply.
Securely connect
cable and/or ground
wire.
Replace pilot burner
and/or ground wire.
Carefully bend down-
wards top of ground
strap to achieve
1/8” spark gap.
Replace pilot burner.
Replace ignition
module.
YES
YES