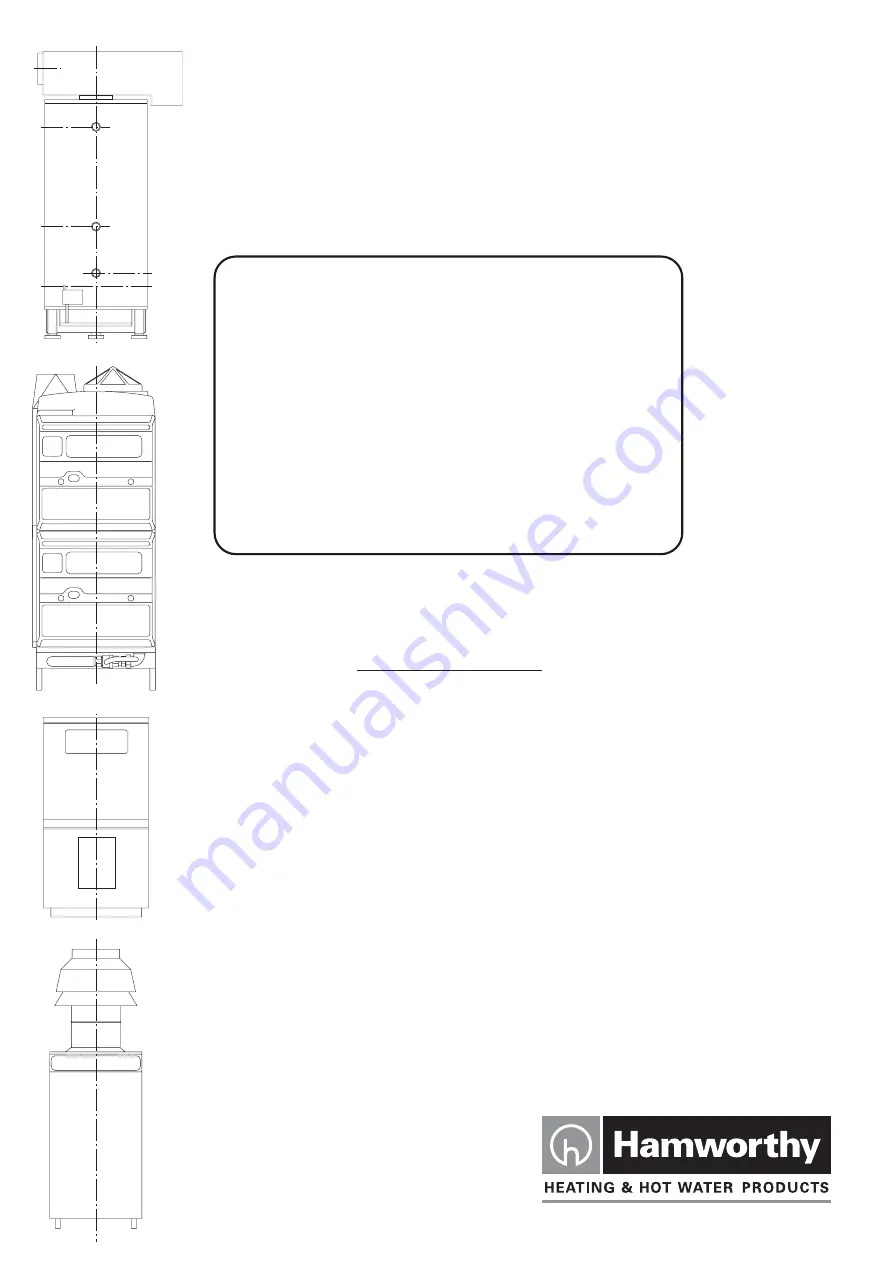
IMPORTANT NOTE
THESE INSTRUCTIONS MUST BE READ
AND UNDERSTOOD BEFORE INSTALLING,
COMMISSIONING, OPERATING OR
SERVICING EQUIPMENT
Wessex Modu
Max
100 Series Boilers
Non Condensing & Condensing
Fully Modulating, Pre-Mix, Gas Fired, Modular
Boilers for Heating and Domestic Hot Water
Installations
Installation, Commissioning
and Servicing Instructions
NATURAL GAS
I
2H