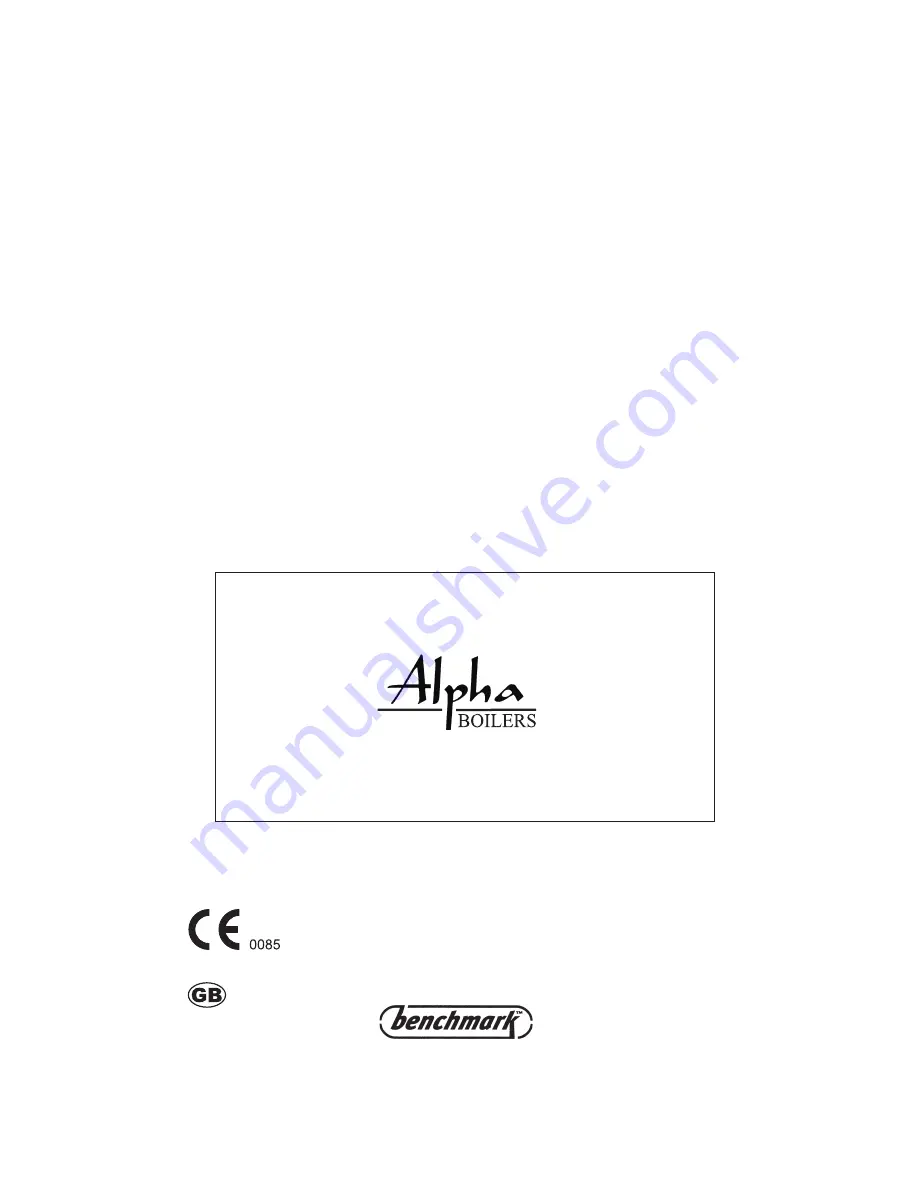
Installation and Servicing
Instructions
Alpha CD18S/24S/30S
Wall Mounted, Fan Assisted, Room Sealed, Gas Fired,
High Efficiency Condensing System Boiler Range
Nepicar House, London Road,
Wrotham Heath, Sevenoaks,
Kent TN15 7RS
For Technical help or for Service call ...
ALPHA HELPLINE
Tel: 0870 3001964
Alpha CD18S
G.C. No. 41 532 06
Alpha CD24S
G.C. No. 41 532 02
Alpha CD30S
G.C. No. 41 532 08
*HEJEID/=I
Service Listed
For use with Natural Gas only
Leave these instructions with the User
Summary of Contents for Alpha CD18S
Page 29: ...29 9 1 ILLUSTRATED WIRING DIAGRAM Alpha CD18S 24S 30S Wiring Diagrams 9 WIRING DIAGRAMS ...
Page 30: ...30 Alpha CD18S 24S 30S Wiring Diagrams 9 2 FUNCTIONAL FLOW WIRING DIAGRAM ...
Page 32: ...32 10 2 FAULT FINDING SOLUTIONS A to E Alpha CD18S 24S 30S Fault Finding ...
Page 33: ...33 Alpha CD18S 24S 30S Fault Finding 10 3 FAULT FINDING SOLUTIONS F to K ...