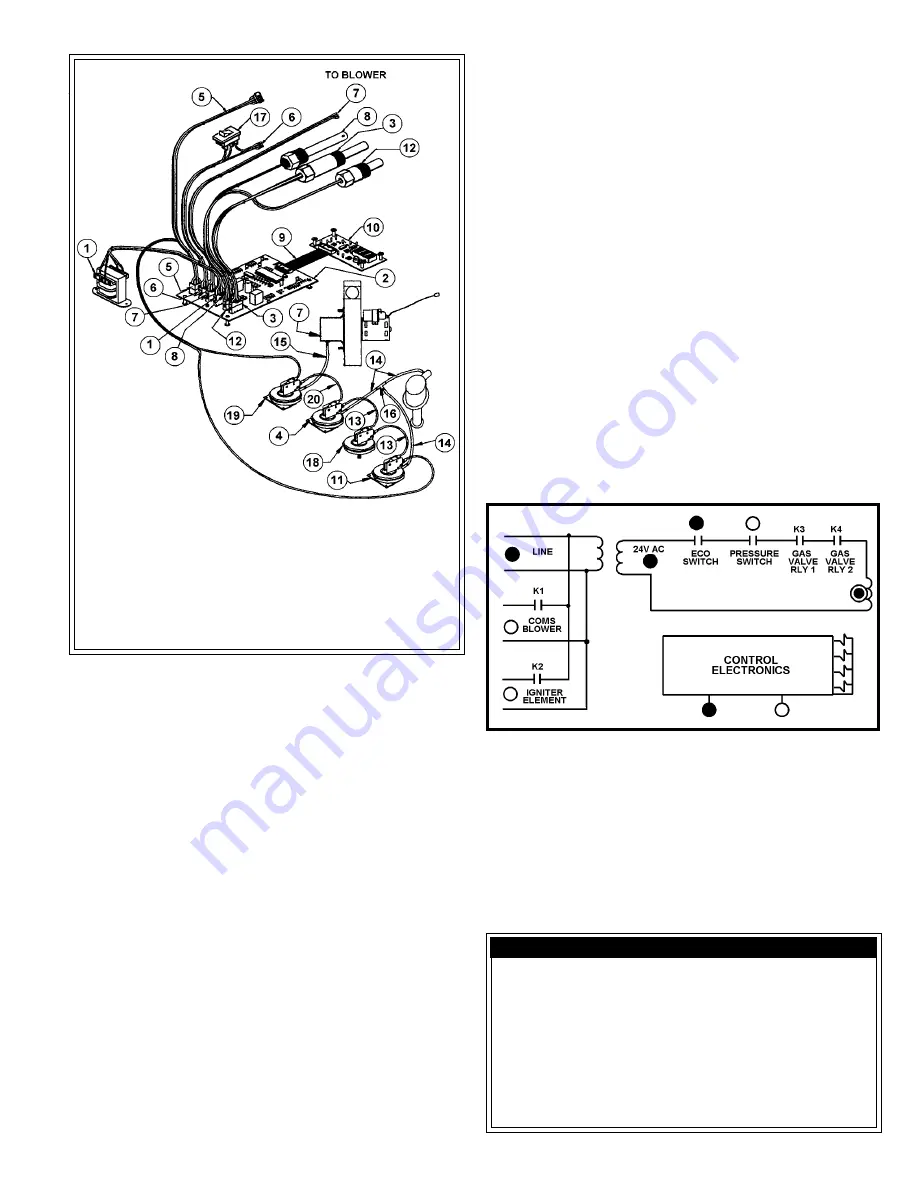
15
OPERATION
SEQUENCE OF OPERATION
Typical Control/Appliance Operating Sequence
1. When the control is powered, it should first display 0, then the input
line voltage (120), the calibration setting (12), then the actual water
temperature in the tank.
2. If the control determines that the actual water temperature inside the
tank is below the programmed temperature setpoint less the differential,
a call for heat is activated.
3. The control then performs selected system diagnostic checks. This
includes confirming the proper state of the air switch and ECO limit
device.
4. If all checks are successfully passed, the combustion blower is
energized for the pre-purge cycle.
5. When the pre-purge cycle is complete, power is applied to the ignitor
element for the ignitor warm-up period.
6. At the conclusion of the igniter warm-up period, the gas valve will open,
allowing gas to enter the burner chamber.
7. The igniter will remain on for a short predetermined time period, then will
be turned off.
8. After an additional 2 seconds, the control will monitor the flame sense
probe to confirm a flame is present. If a flame is not verified within this
time period, the gas valve will immediately be closed, and the blower will
continue to run for approximately 10 seconds. The control will then
return to step 2.
9. If a flame is confirmed, the control will enter the heating mode where it
will continue heating the tank water until the setpoint temperature plus
differential is reached. At this point, the gas valve is closed and the
control enters the post-purge cycle.
10.The combustion blower will run for the duration of the post purge cycle
to purge the system of all combustion gases. When the post purge
cycle is complete, the blower is de-energized and will coast to a stop.
11. The control will now enter the idle state while continuing to monitor the
internal tank water temperature and the state of other system devices.
If the temperature drops below the setpoint value less differential, the
control will automatically return to step 2 and repeat the entire operating
cycle. During this idle state, if the control detects an improper operating
state for external devices such as the ECO switch, vent switch, pressure
switch, etc., the appropriate LED(s) on the Display Board will be
illuminated indicating the nature of the fault.
SELF DIAGNOSTIC CONTROLLER
This controller is designed for ignition lockout after three consecutive failed
attempts to light. If lockout occurs, the display lights will match Figure 18.
Along with this, a numeric message will appear in the display. The following
list of ERROR CODES illustrates possible numeric failures.
FIGURE 18
GAS VALVE LED FLASHING
This condition results from a failure to establish burner ignition after three
successive trials. In such cases:
1. Investigate the possible cause and remedy any observations.
2. Momentarily depress the button on the display panel to reset the lockout
condition.
3. Confirm proper appliance operation.
FIGURE 17
14. Tubing-Pressure
15. Tubing-Pressure
16. Connector-Tubing
17. Switch-On/Off
18. Low Gas Pressure
Switch
19. Bocked Inlet Switch
20. Wire Assembly-Air
Flow Switch
ITEM DESCRIPTION
1. Transformer
2. Control Board
3. E.C.O./Temperature Probe
4. Blower Proving Air Switch
5. Low Voltage Cable Assembly
6. Line Voltage Cable Assembly
7. Blower/Motor Assembly
8. Igniter Assembly
9. Cable To Control Display Board
10. Control Display Board
11. Blocked Outlet Exhaust Switch
12. Lower Temperature Probe
13. Wire Assembly-Gas Pressure
Switch
Possible Cause
Remedy
1. Burner ground wire broken
1. Check wire and connection
or corroded
at burner
2. Connectors unplugged
2. Check connections
3. Igniter broken
3. Replace igniter
4. Flame probe faulty
4. Replace flame probe
5. Gas shut off
5. Turn on gas supply
6. Clogged gas valve
6. Replace gas valve
7. Faulty gas valve
7. Replace gas valve
8. Defective control
8. Replace control
9. Burner improperly adjusted
9. Adjust burner
10. Dirty burner
10. Clean burner