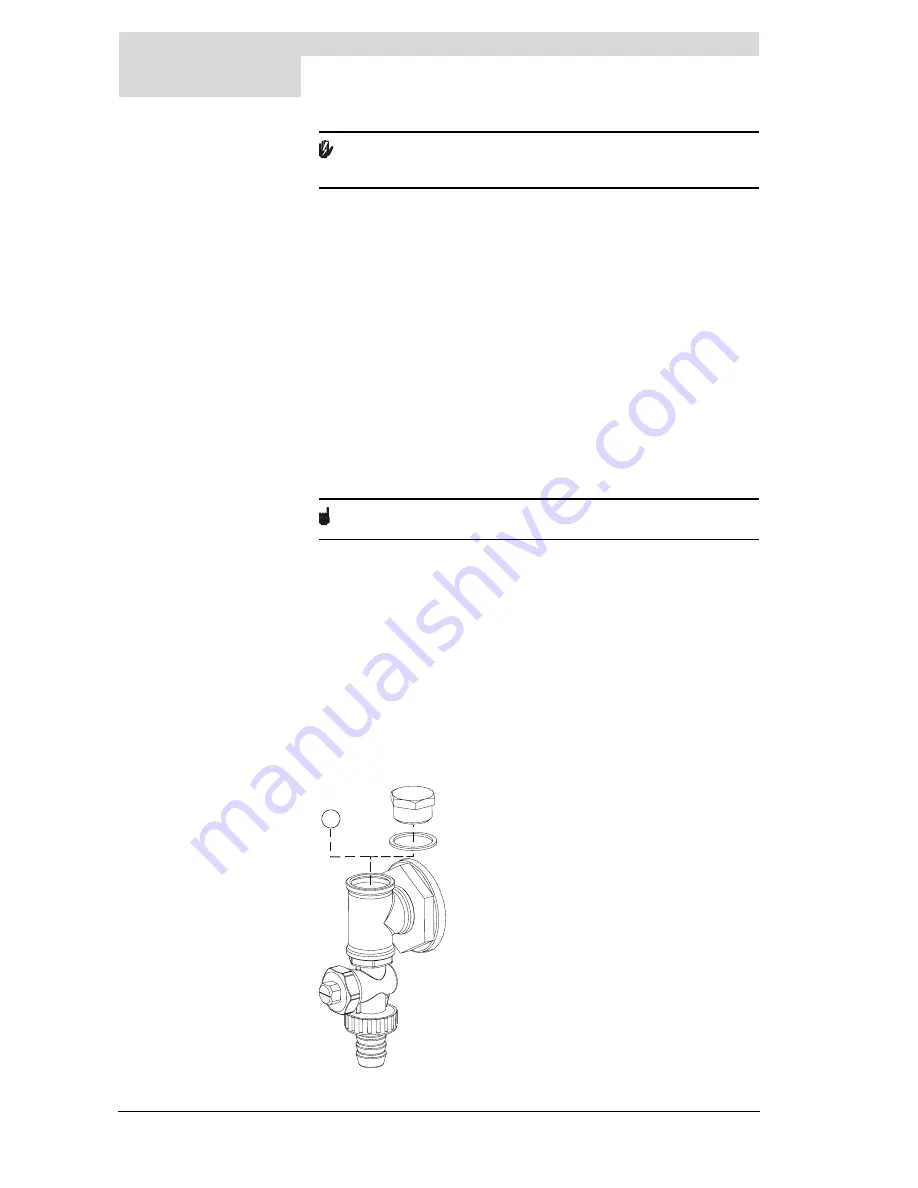
Installation
24
Instruction manual ADMR
3
is
3.6
Water connections,
Vented
Warning
The installation should be carried out by an authorised installation engineer,
in compliance with general and local regulations
(1.3 "Regulations")
.
3.6.1
Cold water side
See (A) in the installation diagram
(3.5 "Installation diagram")
.
1. Fit an approved stop valve (4) on the cold water side between the cold water
head tank (18) and the appliance, as required by
regulations
(1.3 "Regulations")
.
3.6.2
Recirculation pipe
You can install a top to bottom circulation pump to prevent water stacking in the
boiler.
1. Optional: depending on the draw-off pattern, fit a recirculation pipe
(Ø 22 mm), a stop valve (11) and a top to bottom circulation pump (7).
2. Fit a non-return valve (5).
3. Fit a stop valve (11).
3.6.3
Hot water side
See (B) in the installation diagram
(3.5 "Installation diagram")
.
Note
Insulating long hot water pipes prevents unnecessary energy loss.
1. Fit the T&P valve (3).
2. Optional: fit a temperature gauge (12) so you can check the temperature of
the tap water.
3. Fit a stop valve (4) in the hot water outlet pipe, for use when servicing.
4. If a circulation pipe is required, continue further by installing the circulation
pipe
(3.6.5 "Circulation pipe")
.
3.6.4
Drain valve
1. Fit the standard drain valve (9) supplied with the appliance.
2. If applicable, fit a circulation pipe
(3.6.5 "Circulation pipe")
.
If not, fit the blind threaded plug and gasket (C) supplied with the drain valve,
as shown in the figure.
C
IMD-0122 R1
Summary of Contents for ADMR-115
Page 4: ...4 Instruction manual ADMR gis...
Page 8: ...Table of contents 8 Instruction manual ADMR...
Page 12: ...Introduction 12 Instruction manual ADMR 1 gis...
Page 38: ...Installation 38 Instruction manual ADMR 3 is...
Page 56: ...Shutting down 56 Instruction manual ADMR 10 gis...
Page 64: ...Main menu 64 Instruction manual ADMR 11 gis...
Page 78: ...is Instruction manual ADMR 78...
Page 80: ...Maintenance frequency 80 Instruction manual ADMR 14 is...
Page 86: ...Performing maintenance 86 Instruction manual ADMR 15 s...
Page 94: ...Appendices 94 Instruction manual ADMR 17 is...
Page 96: ...Instruction manual ADMR 96...