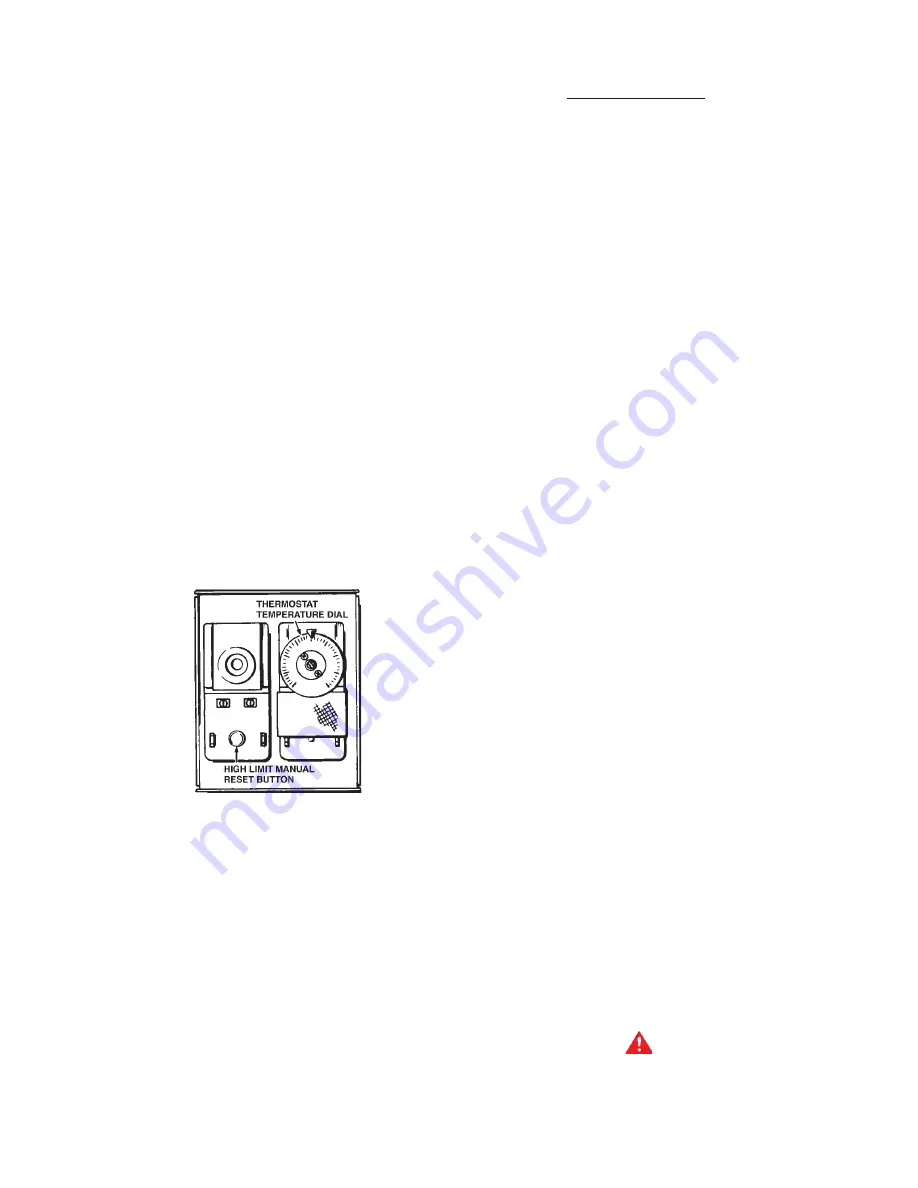
5
The input reduction is primarily achieved by reducing the size of
the main burner orifices. To do this, the main burner orifices
require replacement with orifices sized for the particular installation
elevation. Correct orifice sizing and parts may be obtained from
the manufacturer. See the REPLACEMENT PARTS section of
this manual. When ordering, be sure to state the model number
and the altitude of the location where the heater is being
installed.
Upon completion of derating of the heater, adjustment to the gas
pressure regulator may be required. See ADJUSTMENT
PROCEDURE in this manual for inlet and manifold pressure
requirements.
Also, due to the input rating reduction required at high altitudes,
the output rating of the appliance is also reduced and should be
compensated for in the sizing of the equipment for applications.
FEATURES
HIGH LIMIT SWITCH (E.C.O.)
The dual bulb controller ((fig. 1) contains the high limit (energy
cutoff) sensor. The high limit switch interrupts main burner gas
flow should the water temperature reach 205°F (96°C).
In the event of high limit switch operation, the appliance cannot
be restarted unless the water temperature is reduced by at least
20°F (11°C) and the high limit reset button on front of limit control
(fig.1) is depressed.
DUAL-BULB THERMOSTAT (COVER REMOVED)
FIGURE 1
Continued manual resetting of high limit control, preceded by
higher than usual water temperature is evidence of high limit switch
operation. The following is a possible reason for high limit switch
operation.
•
A malfunction in the thermostatic controls would allow the gas
valve to remain open causing water temperature to exceed
the thermostat setting. The water temperature would continue
to rise until high limit switch operation.
Contact your dealer or servicer if continued high limit switch
operation occurs, to determine the reason for operation.
CIRCULATING PUMP
A circulating pump is used when a system requires a circulating
loop or there is a storage tank used in conjunction with the heater.
Refer to the piping diagrams at rear of manual for electrical
hookup information and install in accordance with the latest
version of the National Electric Code ANSI/NFPA No. 70.
Only all bronze circulators are used with commercial water heaters.
Although circulators are oiled and operated by the manufacturer
some circulators must be oiled again before operating. Please
refer to manufacturer’s instructions.
DISHWASHING MACHINE REQUIREMENT
All dishwashing machines meeting the National Sanitation
Foundation requirements are designed to operate with water flow
pressures between 15 and 25 pounds per square inch. Flow
pressures above 25 pounds per square inch, or below 15 pounds
per square inch, will result in improperly sanitized dishes. Where
pressures are high, a water pressure reducing or flow regulating
control valve should be used in 180
0
line to the dishwashing
machine, and should be adjusted to deliver water between these
limits.
The National Sanitation Foundation also recommends circulation
of 180
0
F water. Where this is done, the circulation should be
very gentle so that it does not cause any unnecessary turbulence
inside the water heater. The circulation should be just enough to
provide 180
0
F water at the point of take-off to the dishwashing
machine. Adjust flow by means of the plug cock in the circulating
line.
INSTALLATION INSTRUCTIONS
REQUIRED ABILITY
INSTALLATION OR SERVICE OF THIS WATER HEATER
REQUIRES ABILITY EQUIVALENT TO THAT OF A LICENSED
TRADESMAN IN THE FIELD INVOLVED. PLUMBING, AIR
SUPPLY, VENTING, GAS SUPPLY AND ELECTRICAL WORK
ARE REQUIRED.
UNCRATING
Uncrate the heater by removing the outside mat and top locator.
The shipping pallet must be removed from the unit. It may be
possible to simply unbolt the base from the pallet and, with the
help of 2 or more persons, work the unit off the pallet. Some
units will be too heavy and will require the use of jacks or lifting
equipment to safely remove the pallet and move the unit into
position. Be careful when moving this heater. It will tip over
easily.
The heater is shipped with a burner and draft control. The burner
and draft control are shipped in separate cartons. They should
be installed as received without any alterations.
Discard the shipping crate and packaging cartons in an appropriate
manner.
LOCATING THE HEATER
WARNING
THERE IS A RISK IN USING FUEL BURNING APPLIANCES
SUCH AS GAS WATER HEATERS IN ROOMS, GARAGES OR
OTHER AREAS WHERE GASOLINE, OTHER FLAMMABLE
LIQUIDS OR ENGINE DRIVEN EQUIPMENT OR VEHICLES ARE
STORED, OPERATED OR REPAIRED. FLAMMABLE VAPORS