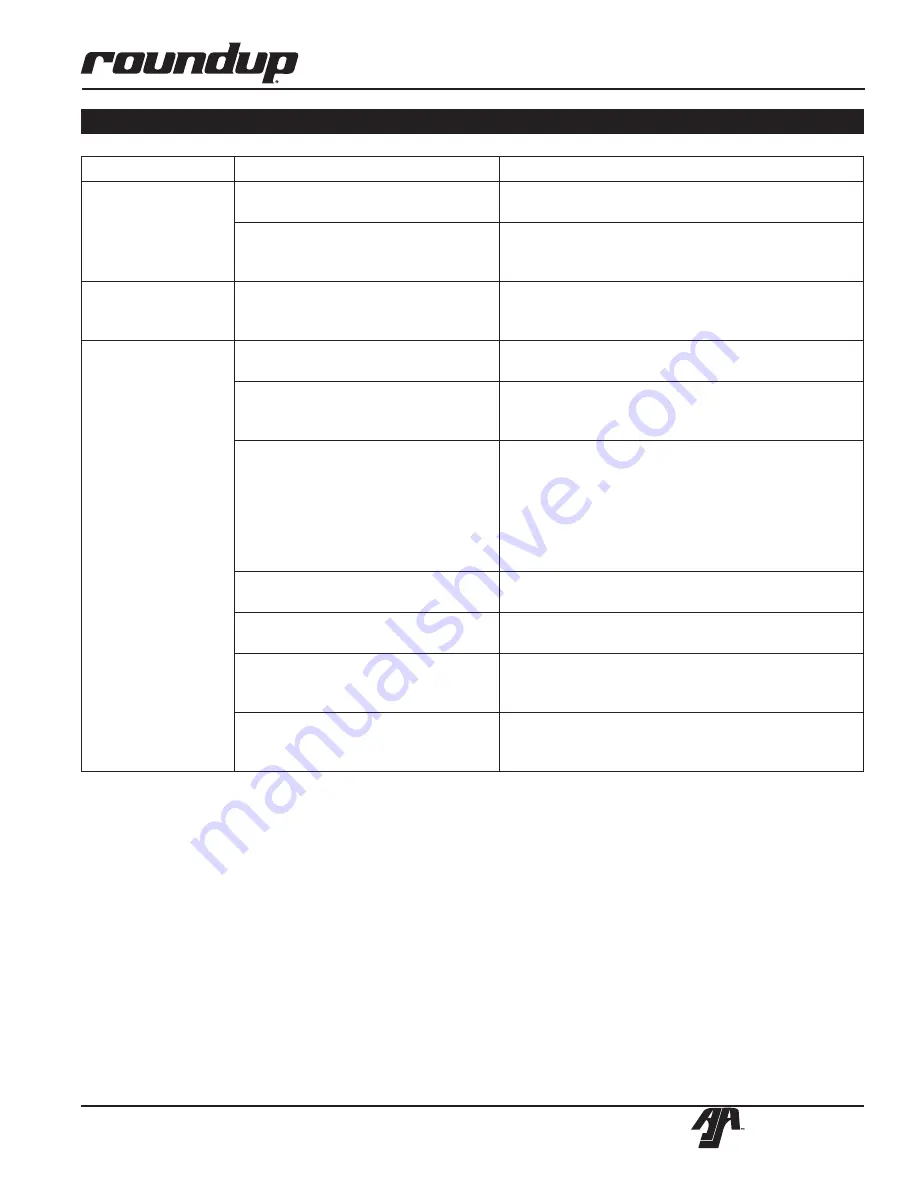
SURFACE STEAMER SS-400TT
13
P/N 1011073 Rev. H 12/13
McDonald’s
A.J. Antunes & Co.
TROUBLESHOOTING (continued)
Problem
Possible Cause
Corrective Action
Excessive
condensation in
Food Compartment.
Water pressure is too high.
Verify that the Water Pressure Regulator is set to
10 psi. Adjust accordingly.
Programming and or
SHOT
and
Intr
values were adjusted improperly
(Timer Models only).
Reprogram the
SHO
and
H2O
values as described
in the Programming section of this manual to factory
settings. See “Factory Resets.”
Excessive Steam
escapes from front
or sides of steamer.
Worn or damaged Bun Caps.
Replace Bun Caps.
Steam Generator’s
surface becomes
flooded (fills with
excess water).
Water Pressure Regulator is faulty or
not properly installed.
Verify that a Water Pressure Regulator is installed
and set to 10 psi. Adjust accordingly or replace.
Programming and/or the
SHO
value
was adjusted or changed improperly.
Reprogram the Control Board to the recommended
settings. Refer to the Programing section of this
manual. See “Factory Resets.”
Solenoid Valve is leaking due to
debris trapped inside the plunger.
Attempt to flush the debris out of the valve by
operating the unit on a number of cycles and then
letting it rest. If the unit still leaks, disassemble
the Solenoid Valve and clean out the plunger.
Reassemble the unit and test again. If a leak is still
present, replace the Solenoid Valves. Contact your
maintenance person or Authorized Service Agency.
Improper Daily/Monthly cleaning.
Follow the Daily/Monthly cleaning procedures
carefully.
The Generator surface temperature
is too low.
Verify that the Generator set point temperature is
between 400°F (204°C). See “Factory Resets.”
Insufficient or excessive calcium/
mineral deposits on the Generator
surface.
Verify that a thin layer of calcium/mineral deposits
is present on the Generator surface. Refer to the
Maintenance section of this manual.
Solenoid Valve is installed incorrectly. If the Solenoid Valve was replaced, verify that the
”IN” and “OUT” labels on the valve correspond to
the water flow.