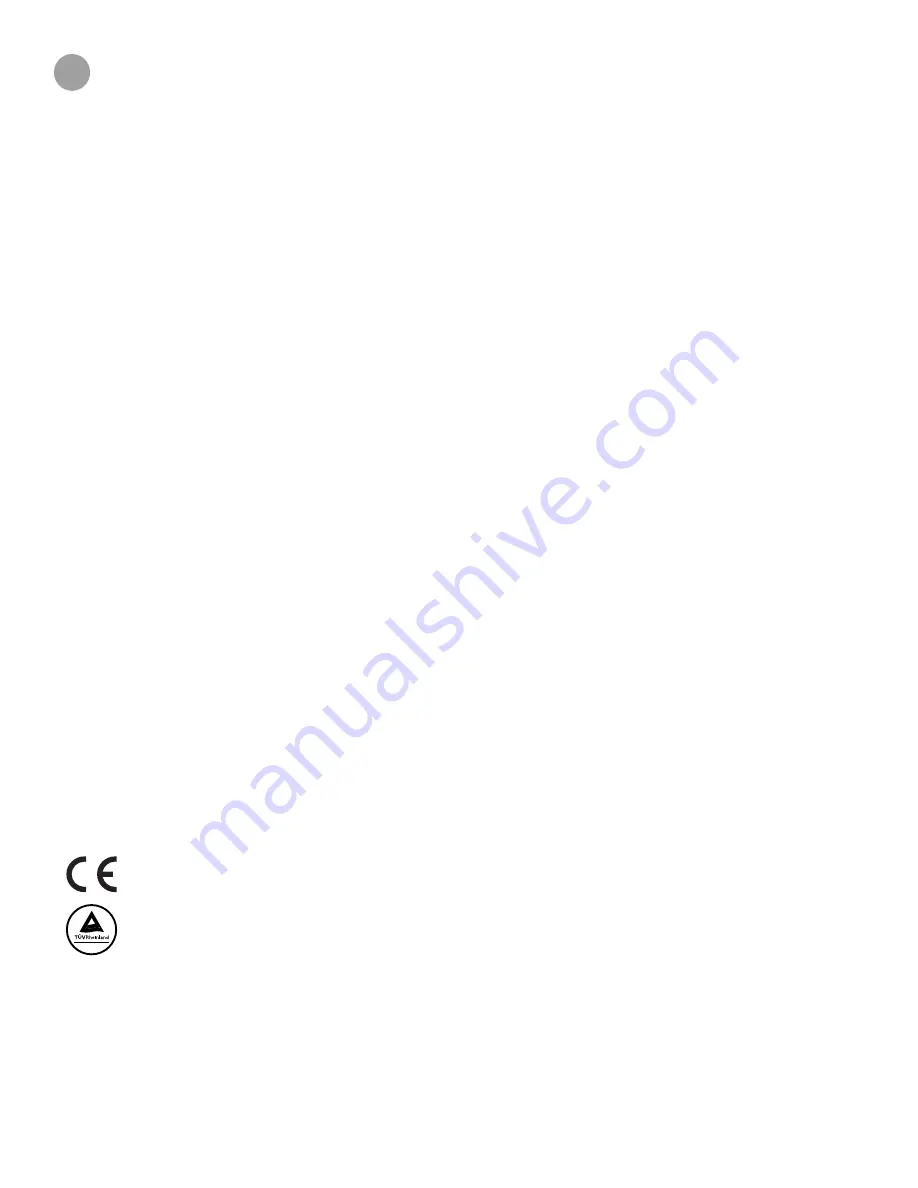
1
3D Systems, Inc.
1
INTRODUCTION
Thank you for purchasing the ProJet
®
1200 3D printer .
The ProJet 1200 professional 3D Printer produces small, detailed parts for casting, prototyping and end-use parts from 3-D solid
Computer-Aided Design (CAD) models . It is intended to be used as a 3-dimensional output device to communicate design intent with
durable, physical parts . Parts produced can be used in all phases of design, from a concept build to functional testing and assembly
verification. For example, a part can be used as a tool to communicate design intent, to verify the fit of a new or existing component part
or to create a rugged, plastic prototype of a new invention. Parts made on the ProJet 1200 are ideal for dental wax-ups, jewelry and
other castings, and durable, stiff parts are also great for plastic prototypes .
These parts are generated in the rapid prototyping (RP) environment under the control of the printer operators . It does not require a
special technical staff to supervise the system . All design and process considerations are compatible with an RP environment . The
three-dimensional solid parts that are printed consist of an ultraviolet (UV) curable material . The resin transfer mechanism provides a
controlled layer thickness of VisiJet® part material which is deposited and patterned using a proprietary imager technology which 3D
Systems
®
has developed . When creating the pattern, the VisiJet® material undergoes a phase change . This phase change converts
the liquid material into a solid polymer . When the print is complete, the part adheres to the print pad . This pad along with the part is
removed from the print platform and the part is cleaned and cured to provide a finished part.
COPYRIGHT
©2014 by 3D Systems
®
. All rights reserved .
Under the copyright laws, this user guide may not be copied, in whole or in part, without the written consent of 3D Systems . The ProJet
logo is a trademark of 3D Systems and is registered in the U .S . Use of this logo without the prior written consent of 3D Systems may
constitute trademark infringement and unfair competition in violation of federal and state laws .
Every effort has been made to ensure that the information in this manual is accurate . Other company and product names mentioned
herein are trademarks of their respective companies . Mention of third-party products is for informational purposes only and constitutes
neither an endorsement nor a recommendation .
The product described in this user guide incorporates copyright protection technology that is protected by method claims of certain U .S .
and foreign patents and other intellectual property rights that are owned by 3D Systems
®
. Reverse engineering is prohibited .
VisiJet
®
is a registered trademark of 3D Systems .
FCC NOTICE
This equipment has been tested and found to comply with the limits for a class “A” digital device, pursuant to Part 15 of the FCC Rules .
These limits are designed to provide reasonable protection against harmful interference . This equipment generates, uses, and can
radiate radio frequency energy and, if not installed and used in accordance with the instruction manual, may cause harmful interference
to radio communications . Operation of this equipment in a residential area is likely to cause harmful interference in which case the user
will be required to correct the interference at their expense.
COMPLIANCE
This equipment conforms with International Electric Committee (IEC) 60950-1 and meets the requirements of the applicable EC
directives .