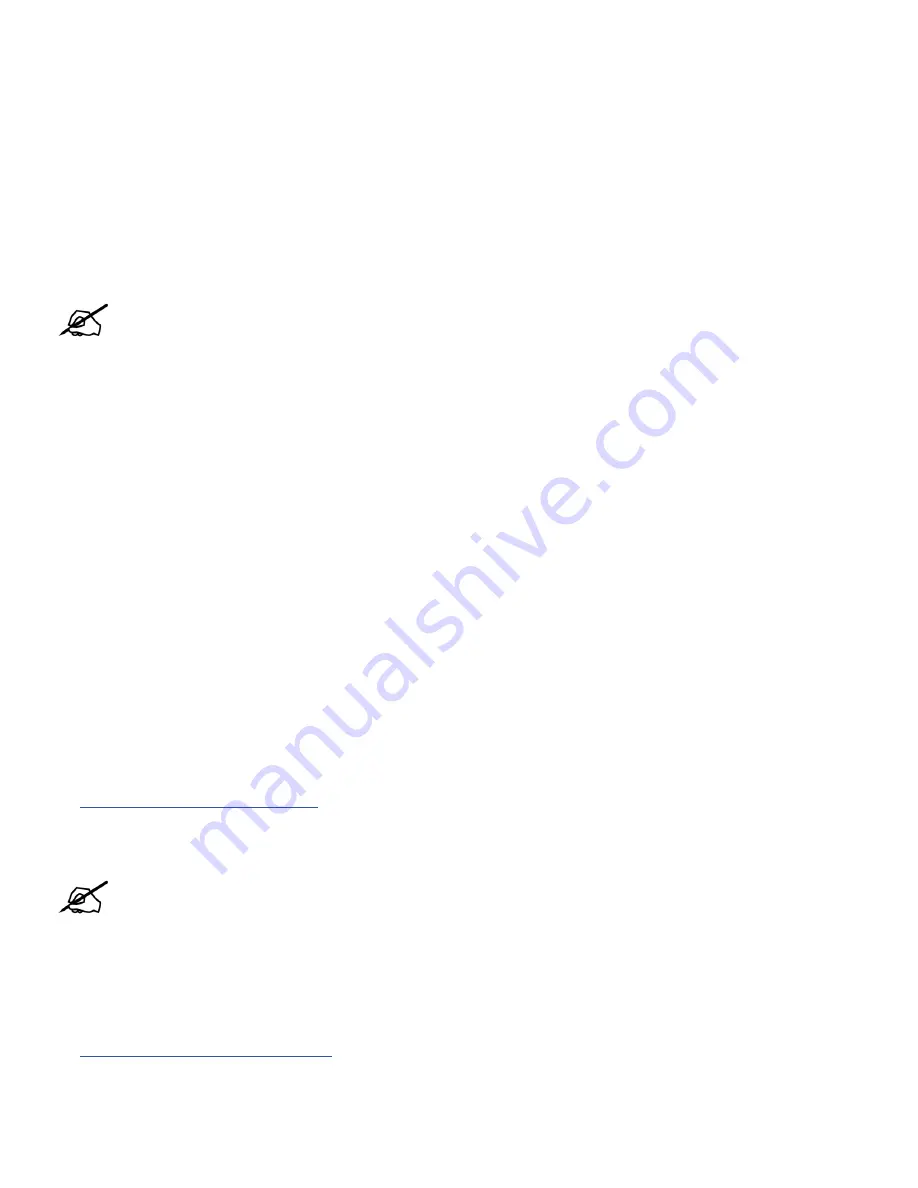
3D SYSTEMS, INC.
75-D059 REV_A
3
Interaction of Variables
Many of the print problems described involve variables that interact with each other . For example, excessive print bed heat or
excessive laser power can cause growth .
As the Print Continues
• The print bed piston indexes down, the parts are covered and begin to slowly cool .
• The mass and geometry of the parts influence the cooling rate. If the cooling rate is too high, the parts can develop post-
print curl or warp . If the cooling rate is too low, growth can occur .
• A part’s position in the print also influences the cooling rate. The first parts printed have the highest cooling rate. First-
order phase changes, such as solidification, occur isothermally; the top of these parts will not cool until the entire part has
solidified. This slows the cooling rate of parts subsequently built.
NOTE: A piston heater heats the bottom of the print bed piston and helps slow the cooling rate. The part
piston cylinder heater heats the print bed walls and is also used to slow the cooling rate and create a constant
temperature across the print bed.
After the initial nitrogen purge, there is make-up nitrogen gas flowing at a constant rate through the print chamber during the
print process as well as across the laser window and the IR sensor heads .
Cool-down Stage
• The cool-down stage allows the material, parts, and SLS system to cool enough to safely remove the print cake from the
print chamber .
• Nitrogen is required for this process and the inert level in the chamber needs to be maintained .
• The length of this stage depends on the size of the print . A larger print will take longer to cool down .
• When this stage ends the material and the SLS system are still
hot.
• Printed parts will be easier to break out when the part cake is still warm and when the surface of the print cake is at or above
50°C. Please refer to the Customer Information Bulletin (Tips & Info) document for more detailed information. You may
contact
your 3D Systems representative for help with maintaining the print cake surface temperature at 50
°
C.
• Removing the parts from the print cake too soon can cause the parts to warp and/or discolor .
• Some part geometries are more susceptible to post-print warp than others .
Condensation in the Process
The DuraForm TPU Elastomer contains a small amount of volatile material that vaporizes during processing . This material
condenses on cool surfaces in the SLS system print chamber .
See
“Crystals and Condensation” on page 14
for information on resolving problems with condensation .
• Heating the nitrogen gas flow across the laser window prevents the condensing material from depositing on the laser
window .
NOTE: It is normal to see some slight condensation (or film) on the laser window after a print. However,
excessive condensation on the laser window can block laser power which can cause weak or porous parts.
• Heating the IR sensor core and flowing nitrogen gas across the IR sensor head helps prevent condensation from forming
on the IR sensor lenses . Excessive condensation on the lenses will cause inaccurate readings of temperatures, leading to
hard or melted material in the print bed . The IR sensor should be inspected before each build and cleaned if necessary .
The laser window should be cleaned before each build.