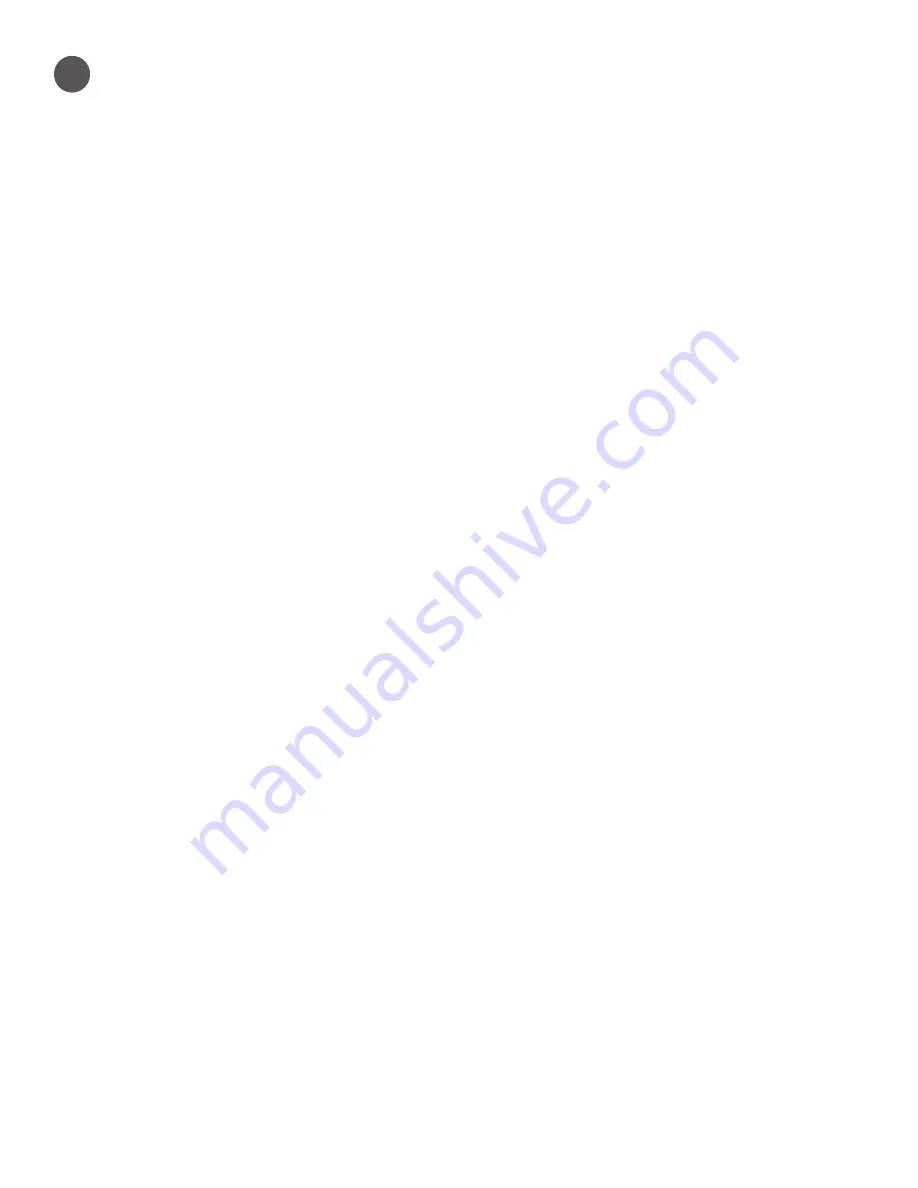
3D SYSTEMS, INC.
75-D059 REV_A
21
5
APPENDIX A - LEGAL NOTICES
COPYRIGHT AND CORPORATE IDENTITY
This document is copyrighted and contains proprietary information that is the property of 3D Systems . The licensed user, in the
name of whom this document is registered (the “Licensed User”) does not have the right to copy, reproduce, or translate this
document in any way or to any media without the prior written consent of 3D Systems . No copies of the document may be sold
or given to any person or other entity .
LIMITATIONS OF WARRANTY AND LIABILITY
This information is provided by 3D Systems for the convenience of its customers . It is believed to be reliable, but NO
REPRESENTATIONS, GUARANTEES OR WARRANTIES OF ANY KIND ARE MADE AS TO ITS ACCURACY, FITNESS FOR A PARTICULAR
USE OR THE RESULTS TO BE OBTAINED THEREFROM . The information is based in whole or in large part on laboratory work
and does not necessarily indicate performance in all conditions . Notwithstanding any information provided by 3D Systems
or its affiliates, the customer remains fully responsible for determining which federal, state or local laws or regulations, or
industry practices are relevant to activities in which it engages, as well as assuring that those laws, regulations or standards are
complied with under actual operating conditions, and 3D Systems undertakes no responsibility in these areas .
IN NO EVENT WILL 3D SYSTEMS BE RESPONSIBLE FOR DAMAGES OF ANY NATURE, INCLUDING SPECIAL OR CONSEQUENTIAL
DAMAGES, RESULTING FROM THE USE OF OR RELIANCE UPON THIS INFORMATION . THE CUSTOMER ASSUMES ALL RISK
RESULTING FROM THE USE OF THIS INFORMATION .
Customers’ use of the materials that follow is an acknowledgment of its agreement to the foregoing . Any customer not
wishing to be bound should return this material to 3D Systems . Nothing contained herein is to be considered as permission,
recommendation, nor as an inducement to practice any patented invention without permission of the patent owner .
TRADEMARKS AND REGISTERED TRADEMARKS
DuraForm is a registered trademark of 3D Systems, Inc .