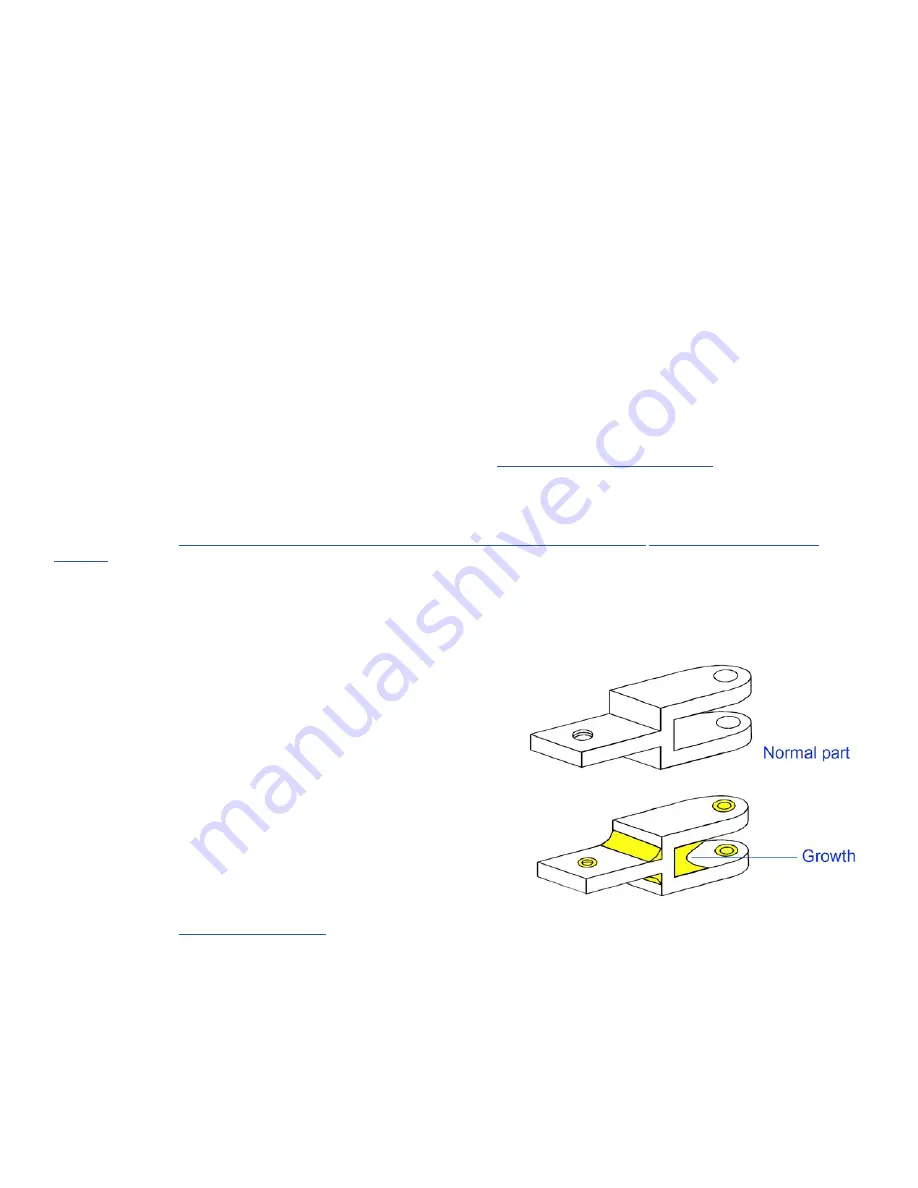
3D SYSTEMS, INC.
75-D059 REV_A
16
GLAZING, DURING PRINT
Description:
Small local regions of material melt on the print bed and cause the bed to glisten . This occurs during the print and
should be distinguished from the glazing point . The melting point of DuraForm TPU Elastomer occurs at approximately 1 to 2°C
above the glazing point .
Theory of Cause:
• The IR sensor is not calibrated correctly or is not clean .
• Uncorrected short feeding .
• The Part Heater Setpoint in the Print Profile is too high.
• The system is trying to reach the temperature setpoint too quickly .
Visual Signs:
All or part of the print bed begins to glaze . In extreme cases, the material melts completely .
Consequences:
Glazing can affect the uniformity of a layer of material. Parts can be difficult to remove from the print cake
during rough breakout . The cake can also shift in the print bed . In severe cases, the print cake may melt and become a solid
block .
Corrective Action:
If this condition is uncorrected and glazing becomes severe melting, you may not be able to continue the
print . You can try to reduce the print bed temperature until the print bed stops melting . If severe melting occurs, terminate the
print and remove the melted powder plug since it will affect the print setpoints through the next several inches .
There are several actions you can take to prevent glazing:
• In the Print Parameters Profile, reduce the Part Heater setpoint.
• In the Warm-up stage of the Print Profile, ramping the heater setpoints.
• Use Offline Calibration to make sure IR sensor is calibrated. See
“Offline IR Calibration” on page 4.
If you have performed all the preceding actions and melting still occurs, you may need to call certified service personnel to
calibrate
the IR sensor .
Related Problems:
“Crystals and Condensation” on page 14, “Melting, Print Bed” on page 17,
GROWTH
Description
: Growth occurs as material sinters on the part, slurring
features and altering part dimensions .
Growth is particularly apparent with small features or small holes . The
difference between growth and Bonus Z is that growth may occur on
any part edge while Bonus Z occurs only on downward-facing surfaces .
Theory
of
Cause
: The laser power may be excessive for thick cross-
sections, or the print bed temperature may be too high .
Visual
Signs
: Growth may not be apparent during the print .
Consequences
: If the part has detailed features, the features may blur .
Parts may be oversized. Parts may be difficult or even impossible to
break out .
Corrective
Action
: Reduce the Part Heater PID Setpoint parameter .
Reduce the Fill Laser Power parameter .
Related Problems: