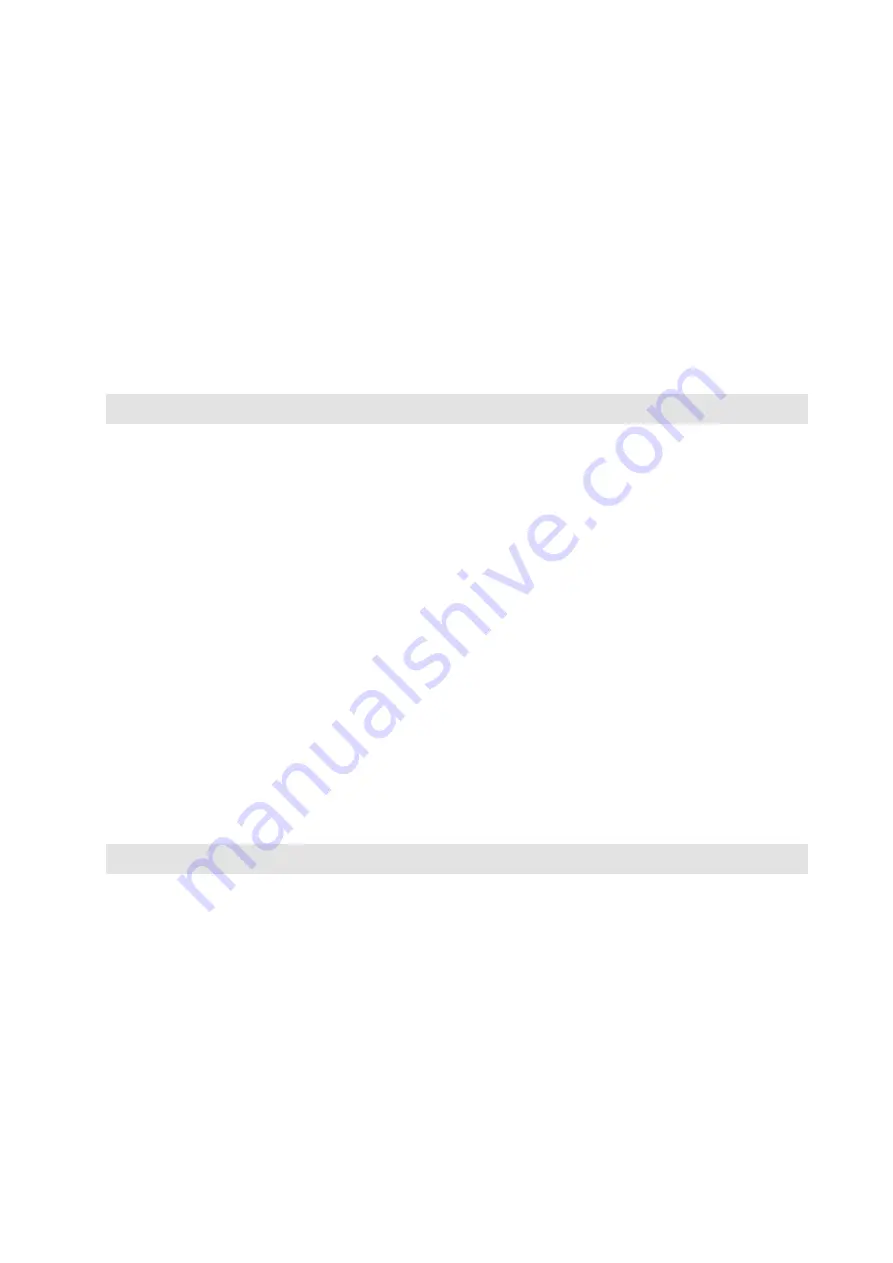
10
The motors consist of two parts:
a)
Power part – is used to draw the necessary torque to the valve and is composed of a single- or three-phase
asynchronous electric motor, countershaft gear box, planet gear box with output shaft, device for manual control
with a hand wheel and floating screw.
b)
Control (electronic) part onsisting of DMS2 or DMS2 ED electronic system is used to control the actuator. The individual
modules of both electronic systems and their functions are described in Chapter
ELECTRONIC OUTFIT.
Operation of the position-limit is derived from rotation of the output shaft via special mechanisms. Operation of the
torque-limit switches is derived from axial displacement of the
“floating worm”
of the manual control unit which is scanned
and transferred to the control box.
The tripping torque can be adjusted within the range specified in the table 1. Torque switches may be blocked when
actuator needs to produce a starting torque.
Showing position of the output shaft of the actuator can be either on site using mechanical indicators or display that
can be installed in the actuator or remotely via an analog output signal and the corresponding indicator. Indicator is not
included in the delivery.
8. ADJUSTMENT OF ELECTRIC ACTUATOR
Stop screws
The stop screws are used to limit the working stroke of the electric actuator to a required value in compliance
with and positions
“Closed“
or
“Opened“
of the piping fittings which do not have their own stops. The stop screws are
located on the external side of the electric motor where the external protective terminal is also fitted. When viewing
the stop screws, the right stop screw is intended for the position “Closed“ and the left one for the position
“Opened“.
Herewith, it is assumed that, when viewed in the direction to the local position indicator, the output shaft moves in the
clockwise sense if it rotates in the direction to
“Closed“.
Adjustment of the stop screws is carried out in such a way
that the stop screws are first released, the electric actuator with the piping fitting is moved to the position
“Closed“
and
the particular stop screw is rotated until there is a perceptible increased resistance as the screw strikes against the
contact plate of the output shaft of the electric actuator. The stop screw is secured by proper tightening of its safety nut.
Then, the output shaft of the electric actuator is turned to the position
“Opened“
and the stop screw is adjusted for the
position
“Opened“
in a similar way.
If a tight closure is required in the end position of the piping fitting and, hence, cutting-out of the electric actuator
by means of the moment switches the cutting-out moment should be transferred to the piping fitting. In such case the
particular stop screw is set so that the piping fitting is properly tight when the trips of the output shaft strike against the
stop screw with cutting-out of the moment switch. Herein, the position and moment switches are connected in series.
This can only be realized in the case when a tightly closed piping fitting is not required.
Clamp rings according to DIN 6799 are use to avoid removing of stop screws. These rings are removable only from
the inside of explosion-proof closure and may in no case be removed.
ELECTRONIC OUTFIT
The actuator is controlled with the electronic system
DMS2 or DMS2 ED. Both systems scan position of the output
shaft and torque of the electric actuator by contact-free magnetic sensors. Long service life is guaranteed for the
contact-free sensors that do not get mechanically worn.
The sensor of the output shaft position is absolute and does not require any backup power supply in case supply
voltage is disconnected during operation of the electric actuator. Both systems can be set and monitored by a computer
with controlling program
(set parameter can be backed up on a computer)
or manually without a computer
(for the
electronics
DMS2,
parameters can be manually set and it can be checked without computer only if the system is
equipped with a display and local control).
They contain diagnostic functions – error messages on the display, memory
of recent failures and number of occurrences of respective failures.
The more simple system
DMS2 ED substitutes the electro-mechanical board and/or provides for controlling
the electric actuator by input analog signal as in the version Control.
The system
DMS2 enables the electric actuator to be used for two-position and three-position regulation or to be
connected to the industrial bus bar Profibus.
Содержание MODACT MOKPED 100 Ex
Страница 2: ...ZPA Pe ky a s is certified company in accordance with ISO 9001 as amended...
Страница 50: ...50 NOTES...