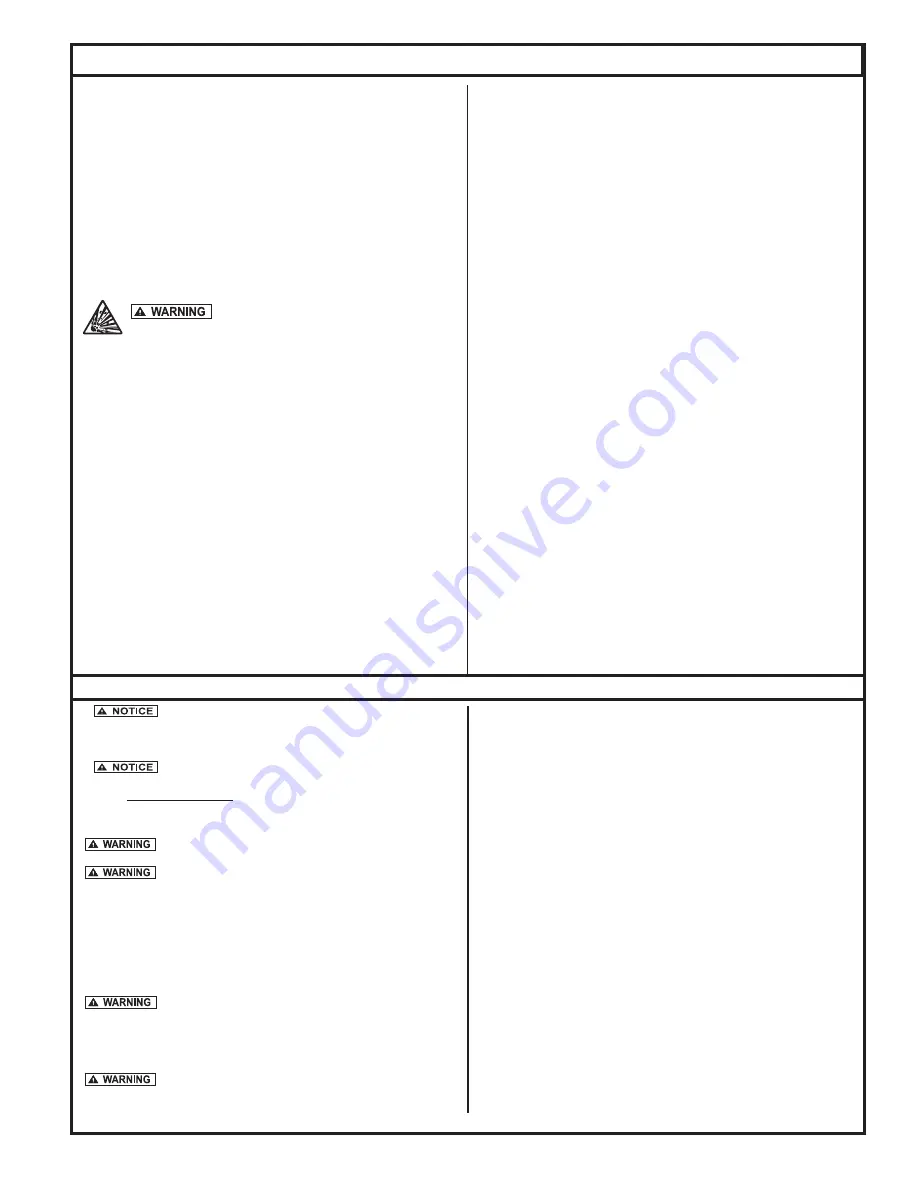
7
© Copyright 2022 Zoeller
®
Co. All rights reserved.
Operation
GENERAL
Zoeller pumps are lubricated and tested at the factory prior to shipment and
require minimum pre-start-up maintenance.
Maximum liquid temperature of a continuous operating pump liquid for this model
pump must not exceed 104 °F (40 °C). For longest service life all pumps should be totally
submerged on long pumping cycles. Maximum submerged depth is 50'.
These units are not designed to handle liquids other than water or sewage. If
pump is used in water contaminated with heavy, viscous, or abrasive materials,
the warranty will be voided.
NAMEPLATE DATA
The nameplate, located on the top of pump, indicates specific information about
the construction of the pump. The model number, date code, and serial number
information should be recorded on the front page in the “Owner’s Information”
section of this manual.
If the pump is repaired in the field, its explosion
proof rating may be voided.
SHORT TERM STORAGE
If pump is to be stored, the following is advised:
• Store pump inside whenever possible or cover with some type of protective covering.
• Tape or seal in plastic bag the terminal ends of wire leads.
• Pump is to be stored in an upright position. Seal leaks that occur in storage
to a pump laying on its side will not be repaired under warranty.
• The impeller should be rotated every six months in order to keep the seals
lubricated and not develop a permanent set.
If panel is to be stored, the following is advised:
• Store the panel inside whenever possible and leave in the shipping box.
• All openings shall be sealed.
• Store in an upright position.
• Do not stack anything on top of panel.
START-UP PROCEDURE
Before placing the equipment into operation the following should be checked:
• Correct pump rotation (3 Phase units only).
• Clean pit.
• Panel dry, securely installed and properly sealed.
• Floats positioned properly.
• Discharge valves open.
• 3/16” vent hole drilled in pipe between check valve and pump.
Once the above has been verified proceed with the following checks:
• Pump power cables properly connected to panel.
• Float cables properly connected in an intrinsically safe panel.
• Conduit connections to panel are properly sealed.
• Thermal overload adjustments made in the panel.
• After installing the pump into the containment area, with adequate submer-
gence, open the discharge valve fully. Start the unit using manual controls.
If flow is appreciably less than rated performance, pump may be air locked.
To expel trapped air, jog the unit several times, using the manual controls.
• Have a qualified electrician take voltage and current measurements on the
black wire of single phase or all three power wires of three phase with the
pump running. Record these readings in the space provided in the
“Owner’s
Information”
section on page 1 of this manual for future reference.
After the preoperational functional test has been completed, system is ready for
operation. Zoeller requires completing a Start-up Report (ZM1074) whenever a
system is started for the first time or after a system has had a significant change
take place (i.e. pump replacement, overhaul, etc..). A copy of the Start-up Report
should remain with the system for future reference.
ADJUSTMENT PROCEDURE
Pumps: No adjustments are required other than assuring correct rotation.
Panels: The thermal overloads in the panel must be set to the F.L.A. rating
on the pump nameplate (or refer to pump data sheet).
Floats:
Refer to the system drawing for desired location of each float function.
Valves: Discharge valves should be placed in the fully open position. Systems
should not be operated for extended periods of time with the discharge
valves partially closed due to damaging the valve.
SHUTDOWN PROCEDURES
If a system is shutdown for more than six months, the following is recommended:
Pumps: If pit is to remain dry, then the pump can remain in the pit. With the
pump in the pit, it should be operated for five minutes once every three
months. If the pit is to remain wet, the pump should be removed and
stored as noted above.
Panels: The panel should have all openings sealed to prevent moisture and dust
from entering the enclosure. Prior to restarting system, the panel should
be inspected for presence of moisture and any loose connections.
Valves: Consult the valve/actuator supplier for information concerning these
systems components.
Maintenance
Repair and service must be performed by a firm approved by
Zoeller Company. The firm must be certified to work on explosion proof motors
if motor housing, adapter or cord cap is repaired. Contact Zoeller Technical
Service Department regarding warranty issues.
If repair to the motor housing, adapter or cord cap is
disassembled or repaired by a firm not certified to work on explosion proof mo
-
tors, the explosion proof rating is void and the cCSAus approval tag
MUST BE
REMOVED FROM THE PUMP.SAFETY PROCEDURES.
SAFETY PROCEDURES
For your protection, always disconnect pump and panel from its
power source before handling.
Never enter the basin until it has been properly vented and
tested. Any person entering a basin should be wearing a harness with safety rope
extending to the surface so that they can be pulled out in case of asphyxiation.
Sewage water gives off methane and hydrogen sulfide gases, both of which
can be highly poisonous.
Installation and checking of electrical circuits and hardware should be performed
by a qualified electrician.
Pump is never to be lifted by power cord.
Unit must be flushed and disinfected, inside and out, prior to
servicing.
GENERAL SYSTEM INSPECTION
Before the system is placed into operation, a system Start-up Report should be
conducted by a qualified technician.
Wiring and grounding must be in accordance with the national
electrical code and all applicable local codes and ordinances.
LUBRICATION PROCEDURES
No lubrication is required.
If pumps are to be stored for more than six months, refer to short term storage
procedure in the Operation section.
PREVENTIVE MAINTENANCE
Preventive maintenance is recommended to ensure a long service life from the
product. Provided is a suggested maintenance schedule.
Every month:
• Check for proper and unobstructed float operation.
• Listen for proper check valve operation.
• Duplex Units - Check for even operating times. Uneven times indicate a
defective unit, float switch or control.
• Inspect the panel for any presence of moisture in enclosure, loose connections, and
general component condition. check out location and condition of float switches.
Every year:
• In addition to the monthly checks, the basin should be inspected and cleaned.
Any defective components should be replaced. Inspect and remove any sand,
debris, or mud present in the pump basin assembly.
Every two years:
• Inspect power cables for damage or wear. Replace immediately if damage or
wear is detected,
• Inspect impeller for damage or wear. Replace as required by a Zoeller
Authorized Service Station.
DOUBLE SEAL PUMPS
• Double seal pumps offer extra protection. During every inspection of the unit,
check the control panel seal failure for a warning. Whenever the seal leak is
activated, indicating that the lower seal has failed, the pump should be removed
and serviced in order to avoid damage to the motor.