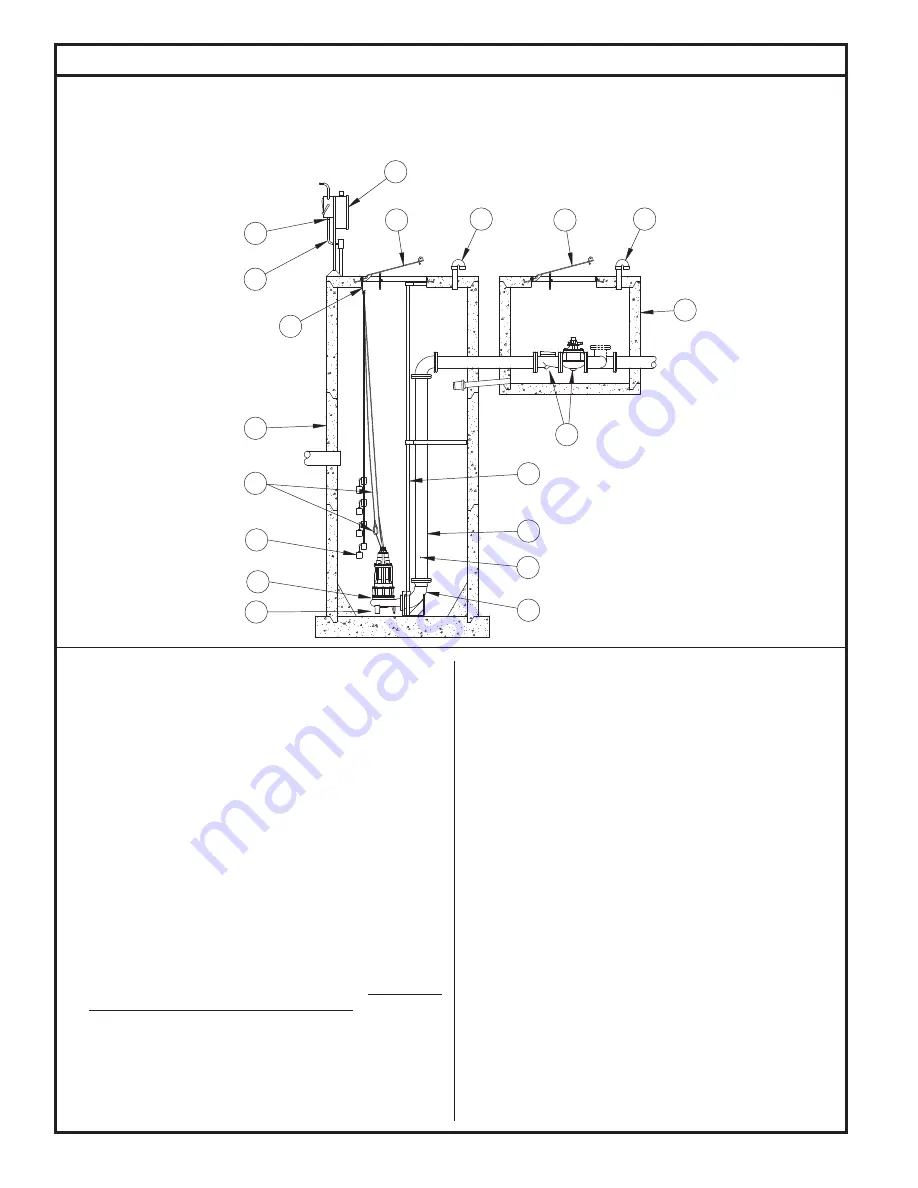
4
© Copyright 2022 Zoeller
®
Co. All rights reserved.
All installations must comply with all applicable electrical and plumbing codes, including, but not limited to, National Electrical Code, local, regional, and/
or state plumbing codes, etc.
TYPICAL OUTDOOR CONCRETE BASIN WITH VALVE BOX AND HINGED ACCESS COVERS
Typical Sewage/Waste Pumping System Installation
7
4
4
7
3
16
1
10
6
12
9
6
13
2
10
14
15
8
11
ZEPA0621
(1) Electrical wiring and protection
must
be in accordance with the National
Electrical Code per NEC articles 500 through 503 for installation in Class
I, Division 1, Group C & D Group C & D Class I, Zone 1, Groups IIA & IIB
locations, and any other applicable state and local electrical requirements.
(2) Install proper full flow check and shut-off valve.
(3) Install proper controls. (Outdoor panels
require
NEMA 3R or 4X enclosure).
Intrinsically safe level sensors are required.
(4) All installations
require
a basin cover to prevent debris from falling into the
basin and to prevent accidental injury.
(5) Cords must be properly sealed per NEC articles 500 through 503 for installation
in Class I, Division 1, Group C & D Group C & D Class I, Zone 1, Groups IIA
& IIB locations, to prevent moisture and gases from entering the control
panel.
(6)
When check valve is installed,
drill a 3/16” diameter hole in the discharge
pipe below the check valve even with the top of the pump. NOTE: The hole
must be below the basin cover and cleaned periodically. Water stream will
be visible from this hole during pump run periods. Also a vent hole is drilled
in the pump housing. Be sure that this hole is cleared during any servicing.
(7) Vent gases and odors to the atmosphere through vent pipe per Local and
State codes.
(8) Secure power cord to avoid entanglement with variable level float switch
mechanism.
(9)
Do not
reduce pump discharge pipe below 4” IPS size.
(10) Basin
must
be in accordance with all applicable codes
and specifications. Basin must be sized to allow a minimum 3 minute
lapse time between starts.
(11) Pump must be level and the tethered variable level float switch must be
free and not hang up on pump or pit peculiarities.
(12)
If
a rail system is used, it should be non-sparking. Discharge elbow
must
be firmly anchored to the bottom of basin. In fiberglass basin, the bottom
will need to be reinforced if the discharge elbow is used.
(13)
If
a rail system is used, it should be non-sparking. The guide rails
are schedule 40 pipe. Brass, stainless steel or galvanized steel is
recommended.
(14) Install choker and cable for lifting pump from pit.
(15) Basin must be clean and free of debris after installation.
(16) Cords must be properly sealed to prevent moisture and gases from
entering the control panel.