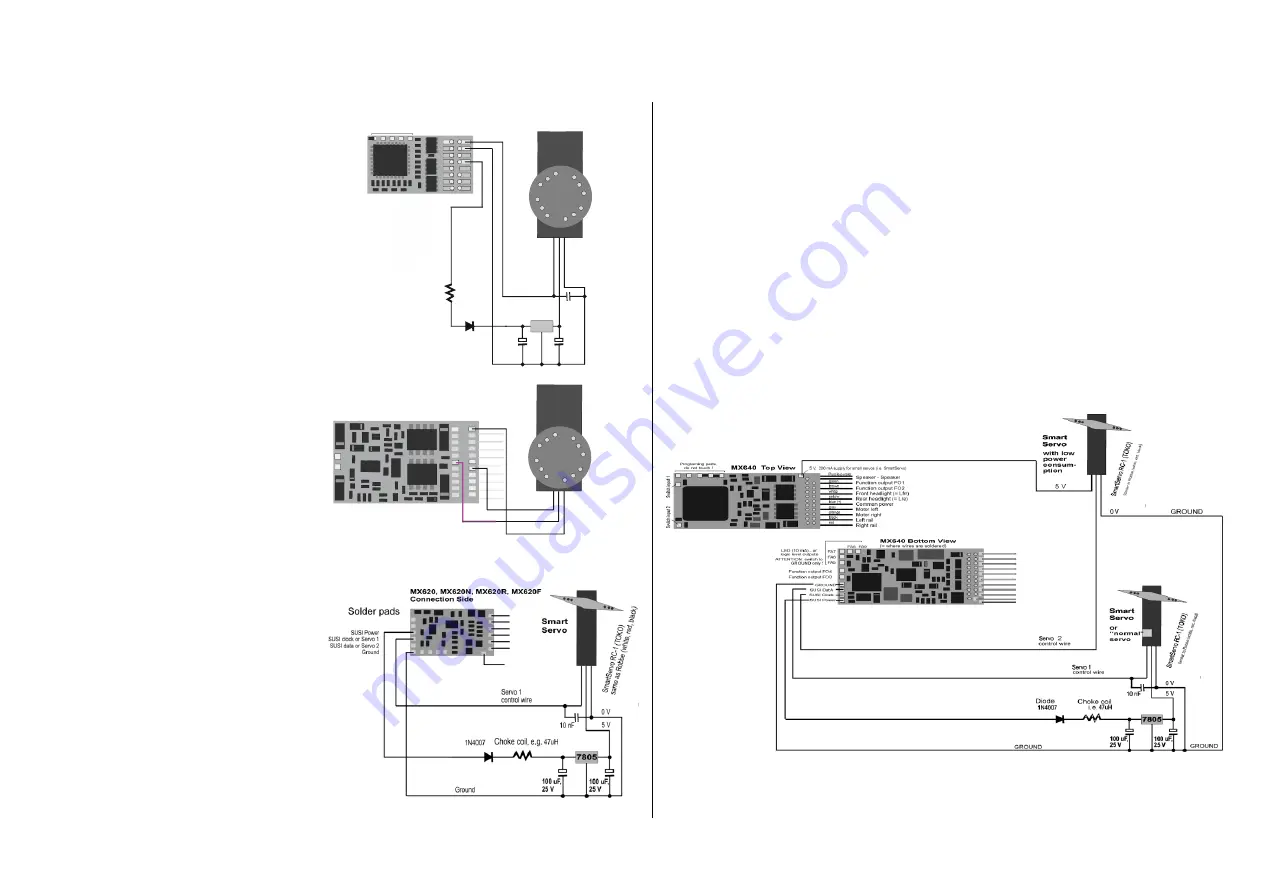
Non-Sound Decoder MX600 - MX638 and Sound Decoder MX640 - MX659 Page 57
Connecting servo and
SmartServo motors:
2 servo control outputs are available on the
MX620, MX630, MX632 and MX640 de-
coders for the control of commercially
available servo motors or
SmartServo RC-
1
(Manufactured by TOKO Corp. Japan).
The corresponding solder pads or pins on
the 21-pin or PluX connector can be used
alternatively for SUSI or as logic level out-
puts or as demonstrated here for servo con-
trol.
The SUSI and logic level functions are not
available if the servo mode is activated
(through CV’s #181 and 182, see below);
this is also true for the function outputs FO5
and FO6 on the MX632.
The models
MX632W
and
MX632WD
also
contain a
5V power supply
to power ser-
vos directly; the 5V supply on the
MX640
is
limited to 200mA.
For other decoder types, the 5V must be
supplied by an external voltage regulator
such as the readily available LM7805; con-
nected as shown in the drawing.
The outputs can be activated for servo con-
trol duty with CV’s #181 and CV #182 (the
value in each must be different than 0).
With the help of CV #181 and #182, the
servo functions can be mapped to various
function keys (plus direction) and selected
for control with either one or two function
keys.
CV’s #161 to #169 define the servos end
positions and rotating speed, see CV ta-
ble.
CV #161 also defines the appropriate ser-
vo protocol. “Normal” for most servos is
positive pulses (which is also the default
setting); furthermore a selection can be
made whether the servo is powered only
while it is being moved or remains pow-
ered at all times. The latter should only be
used if the servo position could change by
outside mechanical influences.
Connecting MX640 and MX642 to servo and SmartServo motors:
Two servo connections are provided on the MX640 for commercially available servos and SmartSer-
vo RC-1 (Manufacturer: TOKI Corp., Japan). These are normally the
SUSI outputs
but can also be
used
as servo outputs
instead.
The connections are in the form of either solder pads or part of the
21-pin socket, depending on the decoder type. Each output can be connected directly with a servo
control wire.
“Energy-saving” servos (max. 200mA) can be powered directly by the MX640!
For servos with higher energy consumptions, the 5V operating voltage must be supplied by an exter-
nal voltage regulator such as the readily available LM7805 as shown in the drawing.
The outputs can be activated for servo control duty with CV’s #181 and CV #182 (the value in each
must be different than 0). With the help of CV #181 and #182, the servo functions can be mapped to
various function keys (and direction) and selected for control with either one or two function keys.
CV’s #161 to #169 define the servos end positions and rotating speed, see CV table.
The appropriate servo protocol can be selected with CV #161. “Normal” for most servos is positive
pulses (which is also the default setting); furthermore a selection can be made whether the servo is
powered only while it is being moved or remains powered at all times. The latter should only be used
if the servo position could change by outside mechanical influences.
For the
SmartServo:
Bit 1 of CV #161 must always be set, that is CV #161 = 2!
5 V
0 V
Servo
1
control wire
S ervo
R
ob
be
: w
hi
te
, r
ed
, b
la
ck
G
ra
up
ne
r:
O
ra
ng
e,
re
d,
b
ro
wn
7805
1N4007
10 uF,
5 V
0
100 uF,
V
10
5 V
0 V
Servo 1
control wire
S ervo
10 F
n
choke coil,
z.B. 47uH
R
ob
be
: w
hi
te
, r
ed
, b
la
ck
G
ra
up
ne
r:
O
ra
ng
e,
re
d,
b
ro
wn
Ground
( 0 V)
Positive
P rogram m i
pads ,
ng
!
do not t ouc h
M
6 0 To p S id e
X
3
M X 6
To p S id e
3 2 W
Servo 2
. . 1
Purple
Ground
Servo 2 Servo 1