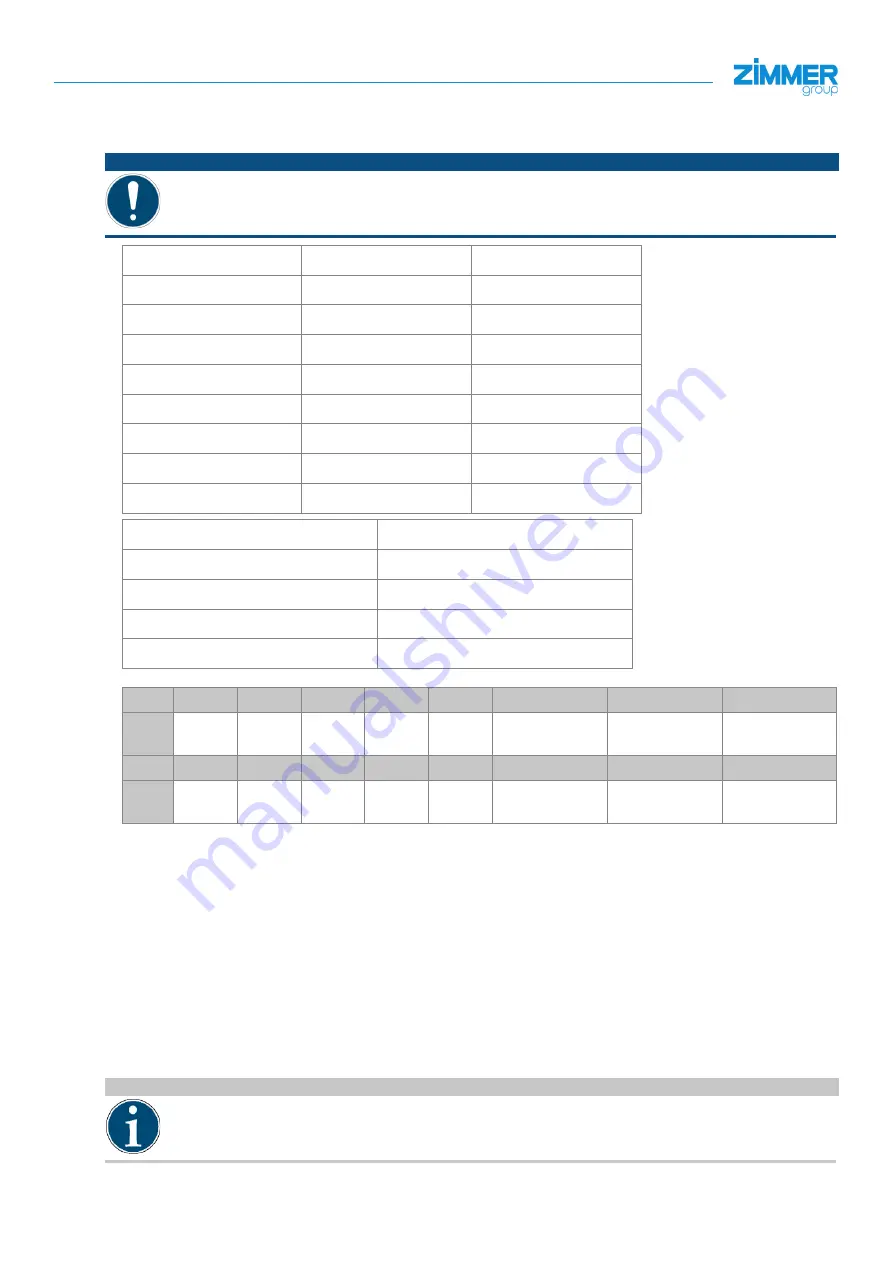
INSTALLATION AND OPERATING INSTRUCTIONS:
2-jaw parallel gripper, hybrid, HRC-04 series
19
Zimmer GmbH
●
Im Salmenkopf 5
●
77866 Rheinau, Germany
●
+49 7844 9138 0
●
+49 7844 9138 80
●
www.zimmer-group.com
DDOC00269 / d
EN / 3/31/2020
8.3 Parameter
8.3.1 „ControlWord“ parameter
NOTICE:
In the „ControlWord“ parameter, only one single bit or the value 0 may be set at a time. Only the values
listed in the following table are valid:
Parameter
Decimal value
Hexadecimal value
Data transfer
1
0 x 1
WritePDU
2
0 x 2
ResetDirectionFlag
4
0 x 4
Teach
8
0 x 8
Adjust
128
0 x 80
MoveToBase
256
0 x 100
MoveToWork
512
0 x 200
ErrorReset
32768
0x8000
Name
"ControlWord"
Data format
UINT16
Permission
Write
Transfer
Cyclical
Value range
0 to 65535
„ControlWord“ structure:
Bit 15
Bit 14
Bit 13
Bit 12
Bit 11
Bit 10
Bit 9
Bit 8
Byte 1
“Error
Reset” -
-
-
-
-
"MoveToWork" "MoveToBase"
Bit 7
Bit 6
Bit 5
Bit 4
Bit 3
Bit 2
Bit 1
Bit 0
Byte 0
"Adjust" -
-
-
"Teach" "ResetDirection-
Flag"
"WritePDU"
"Datatransfer"
Bit 0: „Datatransfer“
►
Setting this bit causes the gripper to accept the data transmitted in the process data („Workpiece-
No“ = 0) or the data stored in the workpiece data records („WorkpieceNo = 1 to 32) as the active
data set.
Bit 1: „WritePDU“
►
Setting this bit communicates to the gripper that it should write the current process data to the
selected tool recipe.
Bit 2: „ResetDirectionFlag“
► Setting this bit informs the gripper that the direction flag needs to be reset.
►
This makes a repeated movement to a position possible.
►
This is logical during a switchover of workpiece recipes.
Bit 3: „Teach“
►
Setting this bit informs the gripper to save the current position as the „TeachPosition“ in the selec-
ted „WorkpieceNo“.
INFORMATION:
This only works if there is no „0“ that is transmitted in the workpiece number!