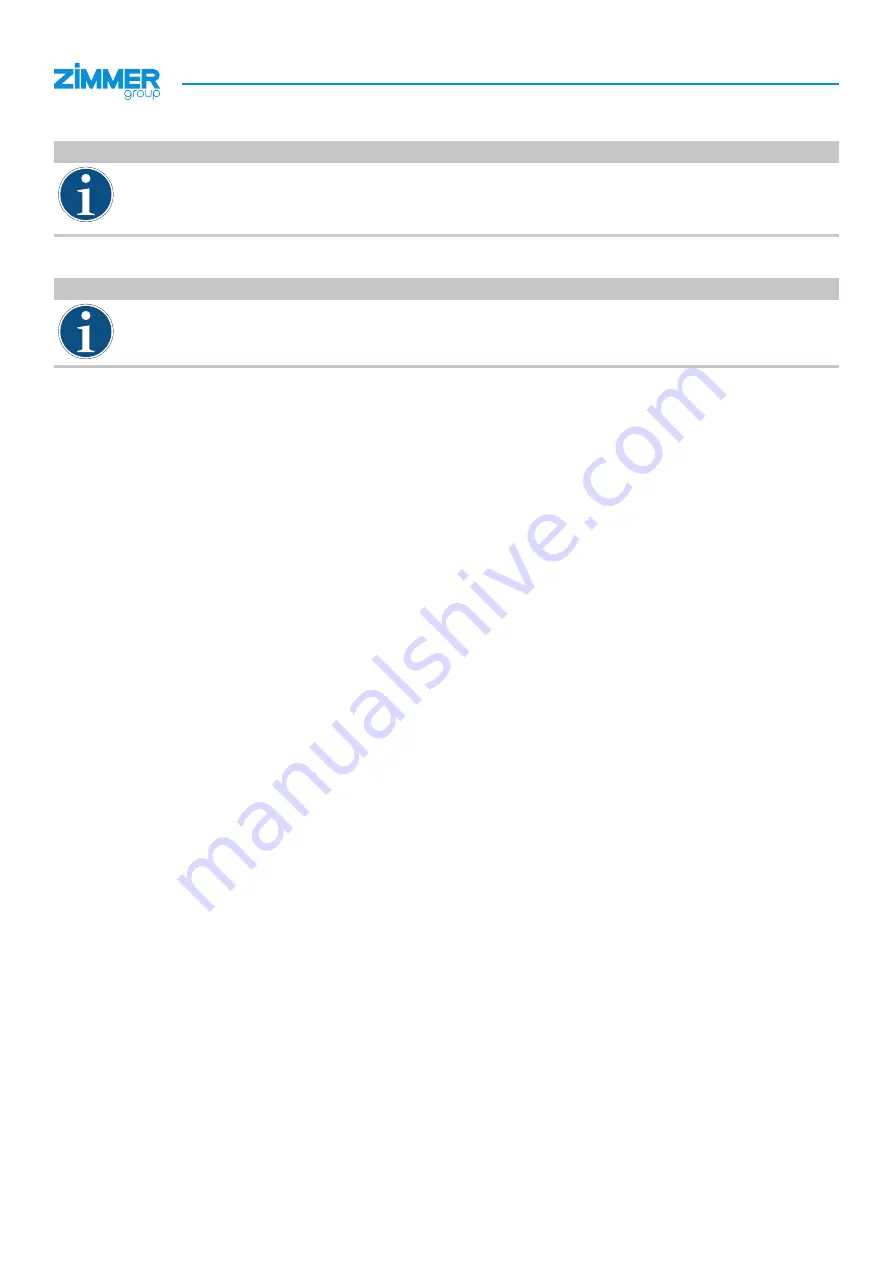
12
7 Technical data
INFORMATION
►
You can find the information in the technical data sheet on our website.
This data varies within the series, depending on the specific design.
►
Please contact Zimmer Customer Service if you have any questions.
8 Accessories/scope of delivery
INFORMATION
If any accessories not sold or authorized by Zimmer GmbH are used, the function of the product cannot be
guaranteed. Zimmer GmbH accessories are specifically tailored to the individual products.
►
For optional accessories and those included in the scope of delivery, refer to our website.
9 Transportation/storage/preservation
►
Transport and storage of the product must be done only with the original packaging.
►
If the product has already been installed on the superordinate machine unit, care must be taken during transport to
ensure that no unexpected movements can occur.
►
Before commissioning the product and after transport, check all power and communication connections as well as
all mechanical connections.
►
If the product is stored for an extended period, the following points are to be observed:
►
Keep the storage location as dust-free and dry as possible.
►
Avoid temperature fluctuations/observe and adhere to the temperature range.
►
Avoid wind/drafts/water condensation formation.
►
Cover the product with a weatherproof, tear-resistant foil to prevent dust.
►
Pack the product and do not expose it to direct sunlight during storage.
►
Clean all components. There must be no soiling left on the components.
►
Visually inspect all components.
►
Remove all foreign substances.
►
Properly remove potential corrosion spots.
►
Close electrical connections using suitable covers.
Zimmer GmbH • Im Salmenkopf 5 •
77866 Rheinau, Germany •
+49 7844 9138 0 • www.zimmer-group.com
INSTALLATION AND OPERATING INSTRUCTIONS:
HRC-03
DDOC00268 / h
EN / 2022-12-19