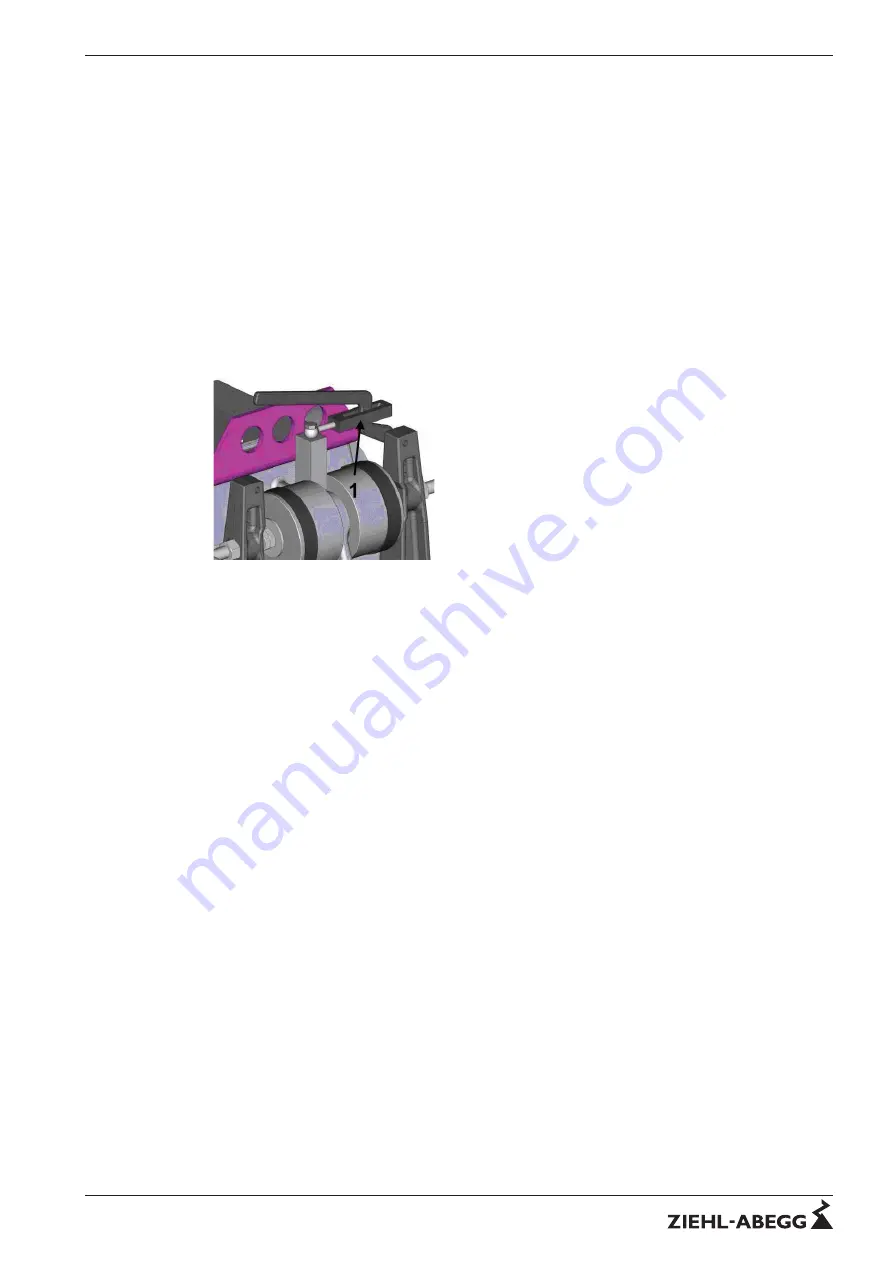
Testing the brake according EN 81-1
It is recommended to perform the tests when the car position is about in the middle of the shaft.
If a safety brake is additionally available, this must be bled for testing the operating brake. This is
possible with the bleeding screws provided.
Overload
The test shall be carried out whilst the car is descending at rated speed with 125 % of the rated load
and interrupting the supply to the motor and the brake.
Caution! To avoid overloading of the gear tooth system, the test load of 125 % may not be applied in
upward direction.
Failure of one brake circuit:
The test shall be carried out whilst the car is descending at rated speed with rated load.
To simulate failure of the brake circuit, it must be possible to keep the brake circuits open mechanically
separately even when opening the safety circuit. A special lever for hand releaser (1) is available for
this.
Picture 6.4.1: Bleeding brake circuits independently of each other
4 Levers for hand release
While performing this test the elevator has to be observed. If there should be no visible deceleration,
the open brake circuit has to be closed immediately! The elevator has to be put out of service and the
brake to be checked!
Testing the safety brake (if available)
As a protective device for the upward moving cabin against overspeeding:
The test is conducted with an empty cabin in upward direction. The operating brake must be kept
mechanically open for this test.
As protection against unintended movement of the cabin (A3):
Please follow the lift manufacturer
’
s instructions!
Testing the micro switches
According to their use as a make or break contact one microswitchcontact at a time has to be opened
or short circuited.
If there is a wrong or missing micro switch signal, a travel must not be started.
6.5
Pull out of safety gear
If the lift car loaded with rated load is caught by the trap due to a fault or during the TÜV inspection,
the trap device could be fairly tight. In such a case it is quite possible that the drive torque is
insuf
fi
cient to pull the lift car out of the trap.
A person may assist additionally at the hand wheel.
A block and tackle or similar must be used in case of insuf
fi
cient drive torque or insuf
fi
cient drive
capacity of the cables.
It is advisable to have a suitable block and tackle on hand for the TUEV inspection.
Note
Note that an overload in the car leads to an increase in the motor torque. 25 % overload results in
150 % of the required motor torque! As regulated drives are normally designed for a maximum torque
of ca. 170 - 200 %, only slight reserves are available during such special cases.
For that reason it is recommended, just as described in EN 81-1 Appendix D.2 j), to perform a TÜV
trap inspection in the door area so that the car can be unloaded there to relieve the drive.
2ULJLQDORSHUDWLQJLQVWUXFWLRQV
ZAS0
Start-up
A-TBA11_06-GB
Part.-No. 01008051-GB
20/72
Содержание ZAS0
Страница 1: ...6 OHYDWRU PDFKLQH ZLWK JHDU 2ULJLQDO RSHUDWLQJ LQVWUXFWLRQV 6WRUH IRU IXWXUH XVH 7 B 3DUW 1R 8...
Страница 36: ...9 2 Dimension sheets 2ULJLQDO RSHUDWLQJ LQVWUXFWLRQV ZAS0 Enclosure A TBA11_06 GB Part No 01008051 GB 36 72...
Страница 38: ...2ULJLQDO RSHUDWLQJ LQVWUXFWLRQV ZAS0 Enclosure A TBA11_06 GB Part No 01008051 GB 38 72...
Страница 40: ...2ULJLQDO RSHUDWLQJ LQVWUXFWLRQV ZAS0 Enclosure A TBA11_06 GB Part No 01008051 GB 40 72...
Страница 41: ...2ULJLQDO RSHUDWLQJ LQVWUXFWLRQV ZAS0 Enclosure A TBA11_06 GB Part No 01008051 GB 41 72...
Страница 42: ...2ULJLQDO RSHUDWLQJ LQVWUXFWLRQV ZAS0 Enclosure A TBA11_06 GB Part No 01008051 GB 42 72...
Страница 43: ...2ULJLQDO RSHUDWLQJ LQVWUXFWLRQV ZAS0 Enclosure A TBA11_06 GB Part No 01008051 GB 43 72...
Страница 45: ...2ULJLQDO RSHUDWLQJ LQVWUXFWLRQV ZAS0 Enclosure A TBA11_06 GB Part No 01008051 GB 45 72...
Страница 47: ...2ULJLQDO RSHUDWLQJ LQVWUXFWLRQV ZAS0 Enclosure A TBA11_06 GB Part No 01008051 GB 47 72...
Страница 48: ...2ULJLQDO RSHUDWLQJ LQVWUXFWLRQV ZAS0 Enclosure A TBA11_06 GB Part No 01008051 GB 48 72...
Страница 49: ...2ULJLQDO RSHUDWLQJ LQVWUXFWLRQV ZAS0 Enclosure A TBA11_06 GB Part No 01008051 GB 49 72...
Страница 50: ...2ULJLQDO RSHUDWLQJ LQVWUXFWLRQV ZAS0 Enclosure A TBA11_06 GB Part No 01008051 GB 50 72...
Страница 51: ...2ULJLQDO RSHUDWLQJ LQVWUXFWLRQV ZAS0 Enclosure A TBA11_06 GB Part No 01008051 GB 51 72...
Страница 53: ...2ULJLQDO RSHUDWLQJ LQVWUXFWLRQV ZAS0 Enclosure A TBA11_06 GB Part No 01008051 GB 53 72...
Страница 54: ...2ULJLQDO RSHUDWLQJ LQVWUXFWLRQV ZAS0 Enclosure A TBA11_06 GB Part No 01008051 GB 54 72...
Страница 55: ...2ULJLQDO RSHUDWLQJ LQVWUXFWLRQV ZAS0 Enclosure A TBA11_06 GB Part No 01008051 GB 55 72...
Страница 56: ...2ULJLQDO RSHUDWLQJ LQVWUXFWLRQV ZAS0 Enclosure A TBA11_06 GB Part No 01008051 GB 56 72...
Страница 58: ...2ULJLQDO RSHUDWLQJ LQVWUXFWLRQV ZAS0 Enclosure A TBA11_06 GB Part No 01008051 GB 58 72...
Страница 60: ...2ULJLQDO RSHUDWLQJ LQVWUXFWLRQV ZAS0 Enclosure A TBA11_06 GB Part No 01008051 GB 60 72...
Страница 61: ...2ULJLQDO RSHUDWLQJ LQVWUXFWLRQV ZAS0 Enclosure A TBA11_06 GB Part No 01008051 GB 61 72...
Страница 62: ...2ULJLQDO RSHUDWLQJ LQVWUXFWLRQV ZAS0 Enclosure A TBA11_06 GB Part No 01008051 GB 62 72...
Страница 63: ...2ULJLQDO RSHUDWLQJ LQVWUXFWLRQV ZAS0 Enclosure A TBA11_06 GB Part No 01008051 GB 63 72...
Страница 65: ...2ULJLQDO RSHUDWLQJ LQVWUXFWLRQV ZAS0 Enclosure A TBA11_06 GB Part No 01008051 GB 65 72...
Страница 66: ...2ULJLQDO RSHUDWLQJ LQVWUXFWLRQV ZAS0 Enclosure A TBA11_06 GB Part No 01008051 GB 66 72...
Страница 68: ...2ULJLQDO RSHUDWLQJ LQVWUXFWLRQV ZAS0 Enclosure A TBA11_06 GB Part No 01008051 GB 68 72...
Страница 69: ...2ULJLQDO RSHUDWLQJ LQVWUXFWLRQV ZAS0 Enclosure A TBA11_06 GB Part No 01008051 GB 69 72...
Страница 70: ...2ULJLQDO RSHUDWLQJ LQVWUXFWLRQV ZAS0 Enclosure A TBA11_06 GB Part No 01008051 GB 70 72...
Страница 71: ...2ULJLQDO RSHUDWLQJ LQVWUXFWLRQV ZAS0 Enclosure A TBA11_06 GB Part No 01008051 GB 71 72...