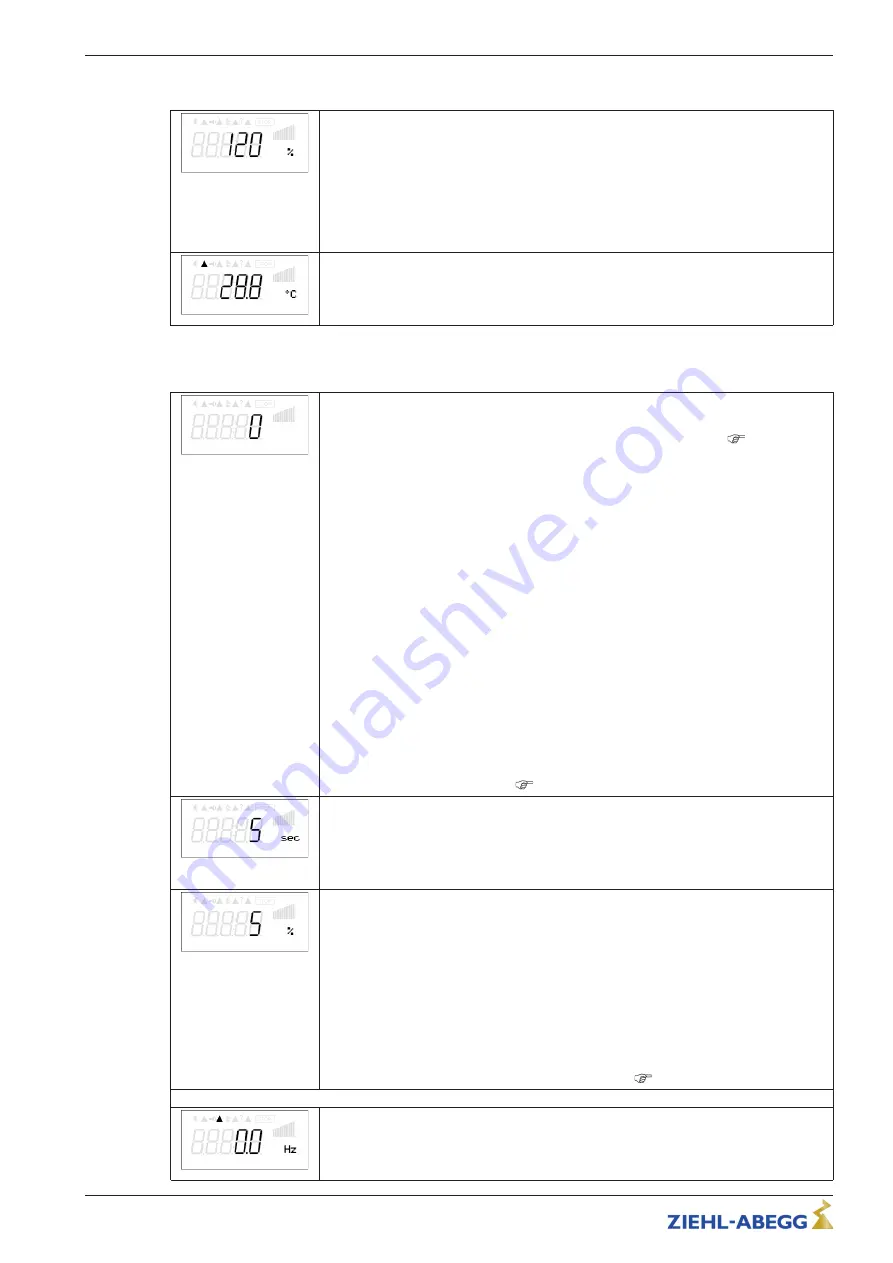
9.12.7
Setting Current limit
Current limit
As an additional safety function the device has a current limit, this can be adapted if
necessary.
The setting refers to the motor rated current of the device (100 % = setting: MotorRa-
tedCurr.).
On exceeding the percentage value set here, the modulation is reduced until the set
current is set again. This prevents overloading of the motor.
Setting range: 100...130 %
Factory setting: 120 %
E1 Actual
Active current limit is signaled by a bright triangle in the display
9.12.8
Setting brake function
DC brake mode
DC brake mode
Setting function of DC-brake for frequency inverters.
For units that come with a factory engaged DC brake mode (if extant,
DC brake
mode setting), simultaneously activating the
“
DC brake mode
”
only makes sense in
exceptional cases.
0
= no brake function (factory setting).
1
= brakes before start (before modulation is returnd)
If, under certain circumstances, the modulation switches back on while the motor is still
rotating fast, this can result in a re-supply of the inverter
’
s
“
overcurrent disconnection
”
.
The brake function can be activated to prevent this. This is then always active for an
adjustable period before triggering starts. I.e., the brake function is always initiated
before modulation after has it returned to
“
0
”
. The suitable adjustments depend on the
centrifugal force of the motor and the conditions in the installation.
2
= Special function, brakes before stop (as soon as modulation
“
0
”
).
The motor does not run out up to stop. The motor is braked actively, as soon as no
modulation is present (Setpoint =
“
0
”
or Enable =
“
OFF
”
).
Test required. The
“
min. speed
”
adjustment must be set to
“
0
”
.
Attention! With the frequently one behind the other following DC bracings it can come
to strong heating up of the motor.
To prevent any overheating, motor protection in the form of a temperature limiter
installed in the motor is required (
motor protection).
DC brake time
DC brake time
Maximal length of DC-brake for frequency inverters.
If the braking is activated, the d.c. brake torque is active for this time.
Setting range: 0...250 sec.
factory setting: 5 / 10 sec. (depending on device type)
DC brake level
DC brake level
Direct-current level, generated for braking. The higher this value, the greater the
braking e
ff
ect.
The setting
“
DC brake level
”
refers in % to the value set in
“
MotorRated Curr.
”
.
Setting range: 0...50 % / 25, 50, 75, 100 % (depending on device type)
factory setting: 5 / 25 % (depending on device type)
The setting is dependent on the size of the fan/motor. Attention! Too high values can
lead to a considerable braking e
ff
ect.
Same setting a
ff
ects also the function
“
Motorheating
”
(
IO Setup).
Frequency
Active brake mode is signaled by a bright triangle in the display.
Operating Instructions
Icontrol
–
model series FXDM
Programming
L-BAL-E036-GB 2022/47 Index 011
Part.-No.
80/108