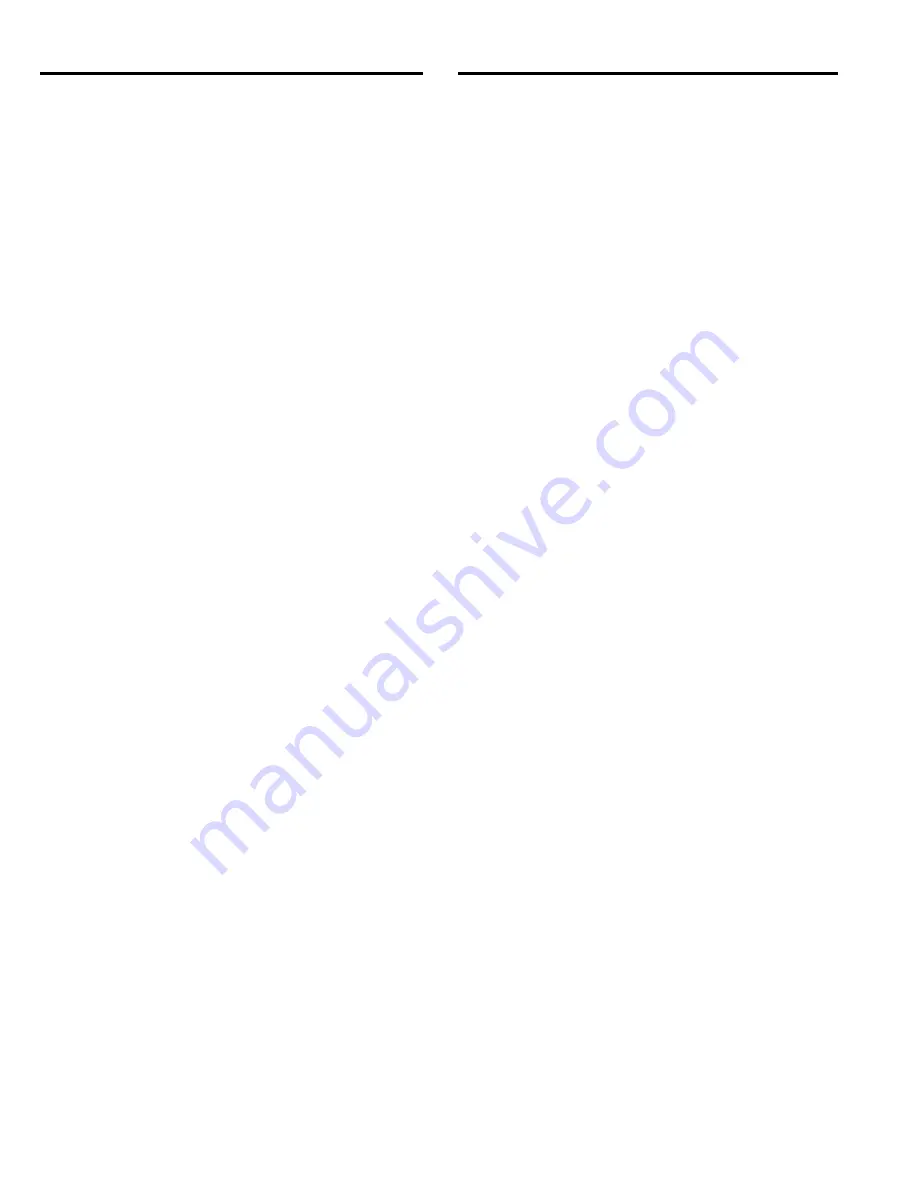
BNP
®
6012 and 7212 SUCTION BLAST CABINETS
Page 28
© 2019 CLEMCO INDUSTRIES CORP.
www.clemcoindustries.com
Manual No. 27723, Rev. B 04/19
8.3.7
Air jet out of adjustment. Check adjustment, per
Section 5.2.
8.3.8
Moist media. Frequent bridging or blockage in
the area of the metering valve can be caused by
moisture. Refer to Section 8.5.
8.4
Plugged nozzle
8.4.1
A damaged or missing reclaimer screen will
allow large particles to pass and block the nozzle.
Replace or reinstall as necessary.
8.4.2
Media mixture too rich. Adjust media-air mixture,
per Section 5.3.
8.5
Media bridging
8.5.1
Frequent bridging or blockage in the media
metering valve can be caused by damp media. Media
becomes damp from blasting parts that are slightly oily,
from moisture in the compressed air, or from absorption
from ambient air.
8.5.2
To avoid contaminating media from the
workpiece, all parts put into the cabinet should be clean
and dry. If parts are oily or greasy, degrease and dry
them prior to blasting.
8.5.3
Moist compressed air may be due to a faulty
compressor that overheats or pumps oil or moisture into
the air line, too long of an air line permitting moisture to
condense on the inside, or from high humidity. Drain the
air filter and receiver tank regularly. Ongoing problems
with moist air may require the installation of an air dryer
or aftercooler in the air-supply line.
8.5.4
Absorption. Some media types tend to absorb
moisture from the air, especially fine-mesh media in
areas of high humidity. Empty the media and store it in
an airtight container when cabinet is not in use.
8.5.5
A vibrator attached to the reclaimer hopper or
media metering valve may help to prevent bridging of
fine-mesh media.
NOTE: To avoid the possibility of
compressing media, a vibrator should be set up to
start when the foot pedal is pressed and stop when
the pedal is released.
8.6
Media surge
8.6.1
Heavy media flow. Adjust media-air mixture, per
Section 5.3.
8.7
Blockage in media hose
8.7.1
Media obstructions. Usually caused when the
media mixture is too rich. Adjust media-air mixture, per
Section 5.3.
8.7.2
Wet or damp media. Refer to Section 8.5.
8.8
Poor suction in media hose
8.8.1
Inadequate air supply. Refer to Sections 1.10
and 2.3.2, and make sure cfm and air hose requirements
are met.
8.8.2
Air jet needs adjustment. Check adjustment, per
Section 5.2.
8.8.3
Nozzle is worn. Replace if orifice diameter is
worn 1/16" or more from original size.
8.8.4
Blockage in media hose or nozzle. Refer to
Sections 8.4 and 8.7.
8.8.5
Air jet and nozzle combination may be wrong.
Refer to the table in Paragraph 1.10.1.
8.8.6
Air jet sleeve extends past end of air jet. Cut the
sleeve to align with the air jet.
8.8.7
Blast pressure too high. Adjust pressure, per
Section 5.1.
8.8.8
Nozzle inserted backward. The wider, tapered
end of the nozzle inserts into the gun toward the air jet.
8.9
Air only (no media) from nozzle
8.9.1
Low media level in reclaimer. Check media level
and replenish as needed.
8.9.2
Check for blockage in media hose; refer to
Section 8.7.
8.9.3
Poor suction in media hose; refer to Section 8.8.
8.9.4
Make sure the air hose and media hose are not
reversed; the green air hose attaches to the back of the
gun and the clear media hose attaches to the bottom of
the gun’s grip. Refer to Page 33, Figure 36.
8.10
Blowback through media hose
8.10.1
Blockage in nozzle. Remove the nozzle and
check for blockage.