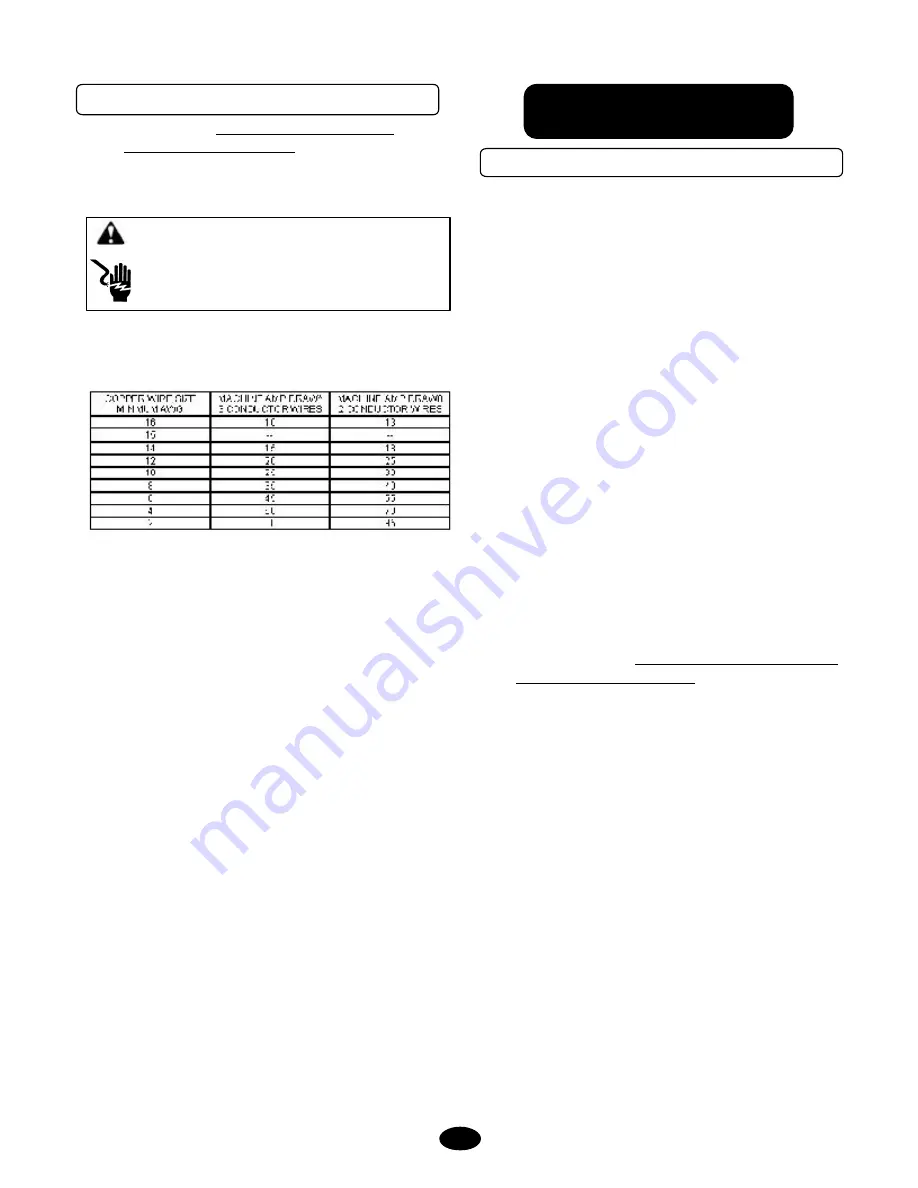
4
Supersedes 08-19-05 Z08-00481B
05-18-06 Z08-00481B
ELECTRICAL INSTALLATION
PRE START-UP
OPERATING
INSTRUCTIONS
WARNING: ELECTRICAL SHOCK HAZARD
AVERTISSEMENT: LE DANGER ELECTRIQUE DE CHOC
ADVERTENCIA:
CHOQUE ELÉCTRICO PELIGRO
1.
The first time the machine is operated, after
repairs have been made, or if the machine has set
for a period of time (30 days or more) follow the
following procedures.
A. Check the tension of the belt (if so equipped)
per instructions in
MACHINE
MAINTENANCE
.
B. Flush the machine per instructions in
MACHINE
MAINTENANCE
.
C. Install float tank drain plug (if so equipped).
D. Open float tank ball valve (if so equipped).
CAUTION:
Always use the factory supplied wash
hose with your machine.
Do not
substitute other
hoses as a potential safety problem may develop.
CAUTION:
If machine has been exposed
t o sub-freezing temperatures, it must be
thoroughly warmed to above freezing before
operating. Failure to warm machine can cause
damage to the pump packings and other
components.
2. Read and observe all items in “CLEANER
INSTALLATION”.
♦
Refer to the
MAINTENANCE
SCHEDULE
for any
maintenance to be performed before operation.
♦
ELECTRICAL
: Connect the machine to an
electrically grounded circuit that is fuse or circuit
breaker protected. Do not use any type of adapter.
If the correct type of receptacle is not available,
have one installed by a qualified electrician.
♦
OIL
LEVEL
: Check the oil level in the water pump.
♦
BELT
: Make sure belt tension and condition is as
specified in MACHINE MAINTENANCE.
♦
METERING VALVE (
if so equipped): Make sure
the metering valve is closed before operation. If air
enters the system through this valve, poor
performance and machine damage will occur. Refer
to the metering valve insert for proper operation.
♦
WATER
SUPPLY
: This machine must have a water
supply meeting or exceeding the maximum
discharge volume specified in the PERFORMANCE
section, and a minimum water inlet pressure of 40
PSI /12.1KGM.
♦
LIME:
Water containing large amounts of lime,
calcium or other similar materials can produce a
coating on the inside of the spray tip, impact nozzle
and coil pipe.
1.
ELECTRICAL
: Connect the machine to an
electrically grounded circuit that is fused or circuit
breaker protected. The circuit must match that
specified in the ELECTRICAL section under
MODEL
SPECIFICATIONS.
WARNING:
To reduce risk of electrocution, keep all
connections dry and off the ground. Do not
touch plug with wet hands.
CHART FIGURES ARE BASED ON NOT MORE THAN
100 FOOT
(Based on Ambient Temperature of 86°F (30°C)).
*Use Amp Draw indicated the same or higher than your
machine output.
EXAMPLE
: Machine Amp Draw 51, use 55 (2 Conductor).
The thermostat type of cord shall be C, PD, E, EO, EN, S,
SO, SRD, SJ, SJO, SV, SVO, SP.
The thermo set plastic types shall be ET, ETT, ETLB, ETP,
ST, STO, SRDT, SJT, SJTO, SVT, SVTO, and SPT.
2.
EXTENSION CORD:
The use of an extension cord
that has undersize wire compared to the amp draw of
your machine will adversely limit the starting load
carrying abilities of the motor and machines
performance. Use only 3-wire extension cords that
have 3-prong plugs and 3-pole cord connectors that
accept the plug from the product. Use only
extension cords that are intended for outdoor use.
These extension cords are identified by a marking
“Acceptable for use with outdoor appliances; store
indoors while not in use.” Use only extension cords
having an electrical rating not less than the rating of
the product. Do not use damaged extension cords.
Use an extension cord in good repair free of frays or
cracks in the outer covering. Do not abuse
extension cord and do not yank on any cord to
disconnect. Keep cord away from heat and sharp
edges. Always disconnect the extension cord from
the receptacle before disconnecting the product from
the extension cord.
Содержание 212 CD
Страница 1: ...Servic e Manua l Servic e Manua l g distribu com 212 CD p n N84201...
Страница 4: ......
Страница 17: ...Trigger Gun Wand...
Страница 21: ...Water Pump EXPLODED VIEW 12 06 05 Z08 05302 PARTS LIST 06 14 05 Z08 01242 6 3...
Страница 27: ...14 Pump Maintenance Record Electrical Schematic...
Страница 31: ......