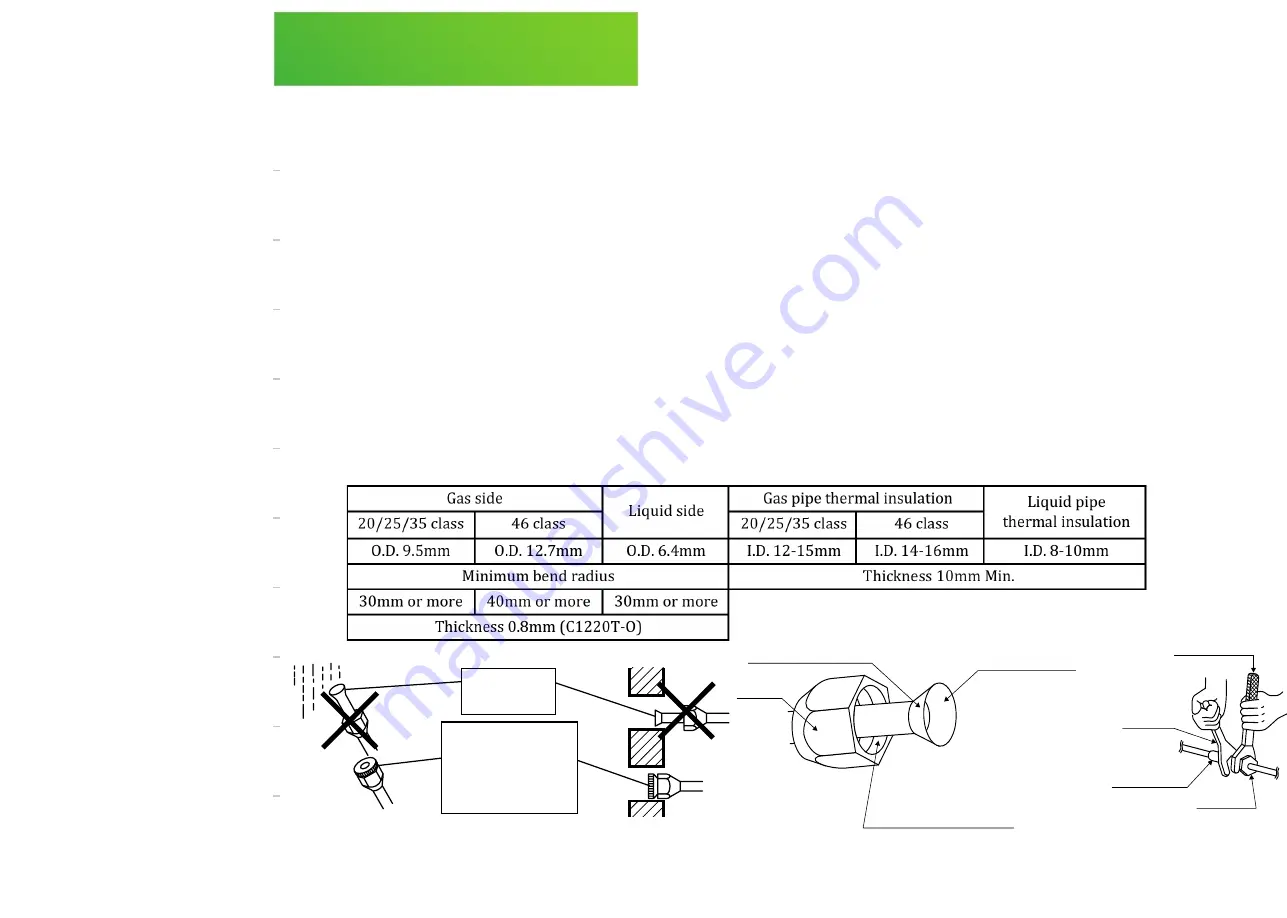
.
5.4
Copper
Piping
(see hand out in Zellabox)
1.
Cut the pipe ends with a pipe cutter
2.
Remove burrs with the cut surface facing downwards so
that the chips do not enter the pipe
3.
Put the flare nuts on pipe
4.
Flare the pipe
5.
Check that the flaring is properly made
6
. Never use old or pre-used pipes
Zellabox
Safety
Instructions
7. Do not use mineral oil on flared part
8.
Incomplete flaring may cause gas leakage
9.
Use flare nut fixed to unit
10.
Use torque wrenches when tightening the flare nuts
11.
Protect ends from dust
12.
Use pipe bender
10.
NEVER use pipes thinner than 0.8mm even when it is
available on the market.
Refrigerant Piping Work
1.
Flaring the pipe end.
1) Cut the pipe end with a pipe cutter.
2) Remove burrs with the cut surface facing
downward so that the chips do not enter the pipe.
3) Put the flare nut on the pipe.
4) Flare the pipe.
5) Check that the flaring is properly made.
1) Do not use mineral oil on flared part.
2) Prevent mineral oil from getting into the system as this would reduce the unit life.
3) Never use piping which has been used for previous installations. Only use parts which are provided with the unit.
4) Do never install a refrigerant drier to this unit.
5) The drying material may dissolve and damage the system.
6) Incomplete or improper flaring may cause refrigerant gas leakage.
WARNING
2.
Refrigerant piping.
1) Use the flare nut fixed to the main unit. (To prevent cracking of the flare nut by aged deterioration.)
2) To prevent gas leakage, apply refrigeration oil only to the inner surface of the flare. (Use refrigeration oil for R410A.)
3) Use torque wrenches when tightening the flare nuts to prevent damage to the flare nuts and gas leakage.
CAUTION
Align the centers of both flares and tighten the flare nuts 3 or 4 turns by hand. Then tighten them fully with the torque wrenches.
2-1. Caution on piping handling
1) Protect the open end of the pipe against dust and moisture.
2) All pipe bends should be as gentle as possible.
Use a pipe bender for bending.
2-2. Selection of copper and heat insulation materials
• When using commercial copper pipes and fittings, observe the following:
1) Insulation material: Polyethylene foam
Heat transfer rate: 0.041 to 0.052 W/mK (0.024 to 0.030 Btu/fth˚F (0.035 to 0.045kcal/mh˚C))
Refrigerant gas pipe’s surface temperature reaches 230˚F (110˚C) max.
Choose heat insulation materials that will withstand this temperature.
2) Be sure to insulate both the gas and liquid piping and to provide
insulation dimensions as below.
3) Use separate thermal insulation pipes for gas and liquid refrigerant pipes.
Flare nut tightening torque
Gas side
Liquid side
1/2 inch
5/8 inch
1/4 inch
36.5- 44.5ft • Ibf
(49.5-60.3N • m)
45.6-55.6ft • Ibf
(61.8-75.4N • m)
10.4 -12.7ft • Ibf
(14.2-17.2N • m)
Gas side
Liquid side
15/18/24 class
O.D. 1/4 inch (6.4mm)
Gas pipe thermal insulation
Thickness 0.393 inch (8mm) Min.
Thickness 0.031 inch
(0.8mm) (C1220T-O)
Thickness 0.039 inch
(1.0mm) (C1220T-O)
Thickness 0.031 inch
(0.8mm) (C1220T-O)
1-9/16 inch (40mm) or more 1-15/16 inch (50mm) or more 1-3/16 inch (30mm) or more
Minimum bend radius
24 class
O.D. 5/8 inch (15.9mm)
15/18 class
I.D. 0.551-0.630 inch
(14-16mm)
24 class
I.D. 0.630-0.709 inch
(16-20mm)
Liquid pipe thermal insulation
15/18 class
O.D. 1/2 inch (12.7mm)
15/18/24 class
I.D. 0.315-0.393 inch
(8-10mm)
(Cut exactly at
right angles.)
Remove burrs
Check
Flare’s inner
surface must
be flaw-free.
The pipe end must
be evenly flared in
a perfect circle.
Make sure that the
flare nut is fitted.
Set exactly at the position shown below.
A
Flaring
Die
A 0-0.020 inch (0-0.5mm)
Clutch-type
Flare tool for R410A
0.039-0.059 inch (1.0-1.5mm)
Clutch-type (Rigid-type)
0.059-0.079 inch (1.5-2.0mm)
Wing-nut type (Imperial-type)
Conventional flare tool
Do not apply refrigeration
oil to the outer surface.
Flare nut
Apply refrigeration
oil to the inner
surface of the flare.
Do not apply refrigeration
oil to the flare nut avoid
tightening with over torque.
[Apply oil]
Torque wrench
Piping union
Flare nut
Spanner
[Tighten]
Wall
If no flare cap is
available, cover the
flare mouth with
tape to keep dirt or
water out.
Be sure to
place a cap.
Rain
Gas pipe
Liquid pipe
Gas pipe
insulation
Liquid pipe
insulation
Finishing tape
Drain hose
Inter-unit wiring
Refrigerant Piping Work
1.
Flaring the pipe end.
1) Cut the pipe end with a pipe cutter.
2) Remove burrs with the cut surface facing
downward so that the chips do not enter the pipe.
3) Put the flare nut on the pipe.
4) Flare the pipe.
5) Check that the flaring is properly made.
1) Do not use mineral oil on flared part.
2) Prevent mineral oil from getting into the system as this would reduce the unit life.
3) Never use piping which has been used for previous installations. Only use parts which are provided with the unit.
4) Do never install a refrigerant drier to this unit.
5) The drying material may dissolve and damage the system.
6) Incomplete or improper flaring may cause refrigerant gas leakage.
WARNING
2.
Refrigerant piping.
1) Use the flare nut fixed to the main unit. (To prevent cracking of the flare nut by aged deterioration.)
2) To prevent gas leakage, apply refrigeration oil only to the inner surface of the flare. (Use refrigeration oil for R410A.)
3) Use torque wrenches when tightening the flare nuts to prevent damage to the flare nuts and gas leakage.
CAUTION
Align the centers of both flares and tighten the flare nuts 3 or 4 turns by hand. Then tighten them fully with the torque wrenches.
2-1. Caution on piping handling
1) Protect the open end of the pipe against dust and moisture.
2) All pipe bends should be as gentle as possible.
Use a pipe bender for bending.
2-2. Selection of copper and heat insulation materials
• When using commercial copper pipes and fittings, observe the following:
1) Insulation material: Polyethylene foam
Heat transfer rate: 0.041 to 0.052 W/mK (0.024 to 0.030 Btu/fth˚F (0.035 to 0.045kcal/mh˚C))
Refrigerant gas pipe’s surface temperature reaches 230˚F (110˚C) max.
Choose heat insulation materials that will withstand this temperature.
2) Be sure to insulate both the gas and liquid piping and to provide
insulation dimensions as below.
3) Use separate thermal insulation pipes for gas and liquid refrigerant pipes.
Flare nut tightening torque
Gas side
Liquid side
1/2 inch
5/8 inch
1/4 inch
36.5-44.5ft • Ibf
(49.5-60.3N • m)
45.6-55.6ft • Ibf
(61.8-75.4N • m)
10.4 -12.7ft • Ibf
(14.2-17.2N • m)
Gas side
Liquid side
15/18/24 class
O.D. 1/4 inch (6.4mm)
Gas pipe thermal insulation
Thickness 0.393 inch (8mm) Min.
Thickness 0.031 inch
(0.8mm) (C1220T-O)
Thickness 0.039 inch
(1.0mm) (C1220T-O)
Thickness 0.031 inch
(0.8mm) (C1220T-O)
1-9/16 inch (40mm) or more 1-15/16 inch (50mm) or more 1-3/16 inch (30mm) or more
Minimum bend radius
24 class
O.D. 5/8 inch (15.9mm)
15/18 class
I.D. 0.551-0.630 inch
(14-16mm)
24 class
I.D. 0.630-0.709 inch
(16-20mm)
Liquid pipe thermal insulation
15/18 class
O.D. 1/2 inch (12.7mm)
15/18/24 class
I.D. 0.315-0.393 inch
(8-10mm)
(Cut exactly at
right angles.)
Remove burrs
Check
Flare’s inner
surface must
be flaw-free.
The pipe end must
be evenly flared in
a perfect circle.
Make sure that the
flare nut is fitted.
Set exactly at the position shown below.
A
Flaring
Die
A 0-0.020 inch (0-0.5mm)
Clutch-type
Flare tool for R410A
0.039-0.059 inch (1.0-1.5mm)
Clutch-type (Rigid-type)
0.059-0.079 inch (1.5-2.0mm)
Wing-nut type (Imperial-type)
Conventional flare tool
Do not apply refrigeration
oil to the outer surface.
Flare nut
Apply refrigeration
oil to the inner
surface of the flare.
Do not apply refrigeration
oil to the flare nut avoid
tightening with over torque.
[Apply oil]
Torque wrench
Piping union
Flare nut
Spanner
[Tighten]
Wall
If no flare cap is
available, cover the
flare mouth with
tape to keep dirt or
water out.
Be sure to
place a cap.
Rain
Gas pipe
Liquid pipe
Gas pipe
insulation
Liquid pipe
insulation
Finishing tape
Drain hose
Inter-unit wiring
Please note: Pipe size is 9.5mm for cooling capacity 2kw up to 3.5kw (See enclosed
manual with condenser)
5 Single & Dual cooling
system
commissioning
steps:
12
Содержание Cubb
Страница 1: ...1 Zellabox Installation Manual...
Страница 20: ...Warning Fire Suppression System Information 20...