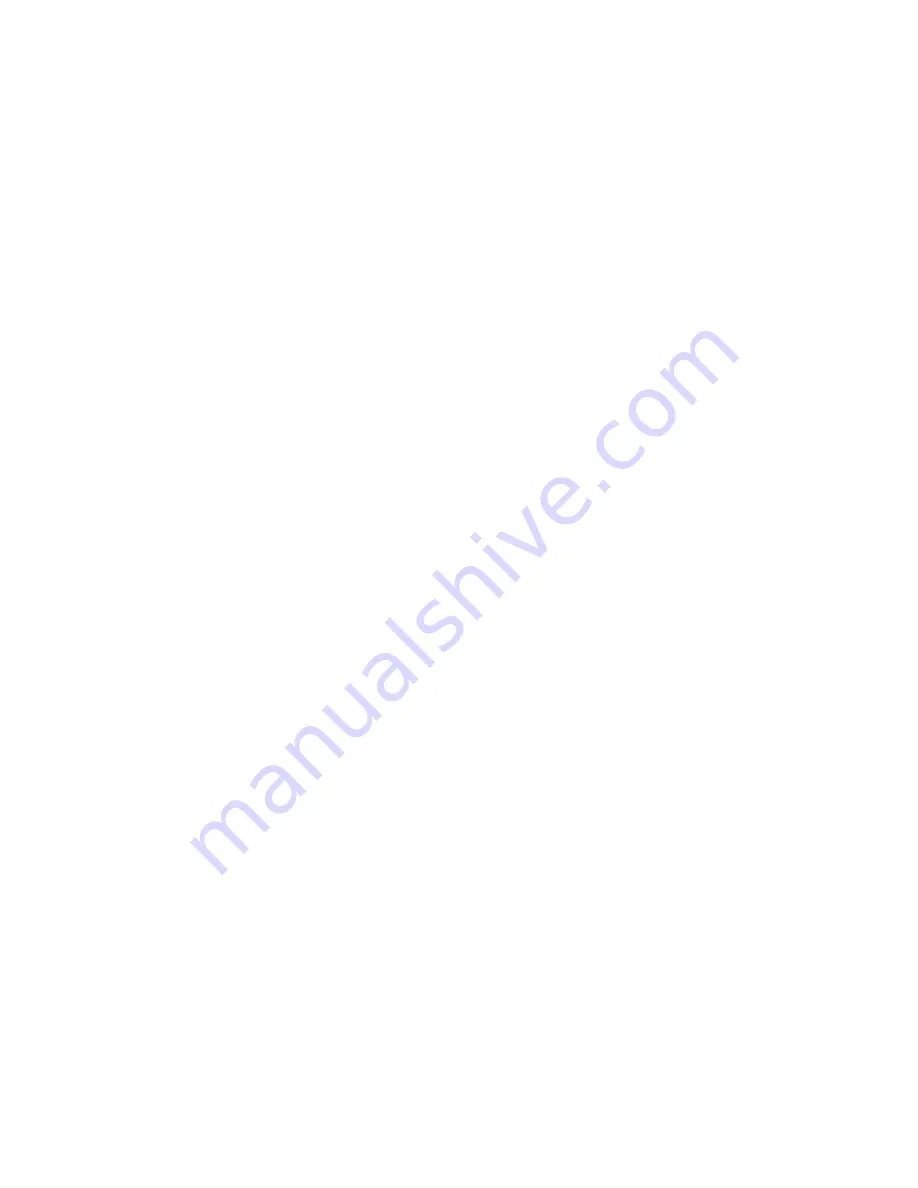
34
Should the control open, it will remain open until the pressure in the system is lowered to 300 psig. Tripping of the high
pressure control is normally due to:
1. Restricted condenser coil.
2. Overcharge of refrigerant.
3. Defective fan motor or fan capacitor.
4. Incorrect fan blade.
5. Fan motor internal overload tripping due to lack of lubrication or defective bearings.
To test the high pressure control: Install a high pressure gauge to the access valve or the liquid line valve. Disconnect the
condenser fan motor. Turn on the unit and observe the pressure on the gauge when the compressor trip off. The pressure
should be 350 ± 10 psig. Allow the system to remain off, until the gauge pressure drop to approximately 300 ± 10 psig and
reconnect the condenser fan motor. Reset the unit by putting off the thermostat and if the high pressure control has
closed, the compressor will restart.
LOW PRESSURE PROTECTION
To provide protection for the compressor in the event of refrigerant loss, a low pressure sensor is installed in the suction
line.
The control is preset to open when the suction pressure is 10 ± 5 psig. The contacts of the control will close when the
suction pressure rises to 30 ± 5 psig. To test the control for the correct pressure setting, install a compound gauge to the
gauge port on the suction service valve. "Front seat" the liquid valve and start the unit. Note the gauge pressure, when
the compressor stops.
To determine the cut-in pressure, allow the suction pressure to build slowly and observe the gauge pressure at the time
when contact closes. A good functional low pressure switch must have both cut-out and cut-in pressure within ± 2 psig.
PUMP DOWN CONTROL
A pump down control is a solenoid type valve installed in the liquid line to prevent the flow of refrigerant into the evapo-
rator during the off cycle. The valve is mounted in the liquid line refrigerant stream or at other suitable location in the liquid
line, but ahead of metering device.
Pump down operation takes place as soon as the signal for cooling is switched off. The system’s control closes the liquid
line solenoid valve while the compressor is continuously running to pump out a substantial portion of refrigerant in the
evaporator. The compressor will shut off when either the suction pressure goes down at a pre-set pressure of 25 psi or
at a pre-set timing of 10 seconds whichever is satisfied first. On call for the next cooling cycle, the solenoid valve will get
energized ahead of the compressor at a pre-set timing. This is to allow refrigerant to flow in the evaporator and thereby
increasing the suction pressure above the low pressure trip setting before the compressor starts.
A pump down control may be necessary on an installation where additional protection for the compressor is required to
prevent slugging of oil or liquid refrigerant.
Below are some conditions which may exist in an installation where additional protection is required:
1. Migration of refrigerant to the compressor during the off cycle.
2. Flooding, at start-up, due to improperly trapped lines or coil.
3. Suction line in slab or beneath ground forming a large trap.
4. Suction line in cool area causing refrigerant to condense during off cycle.
5. Where condensing unit is installed using existing coils and copper lines, or on a new installation where the above said
conditions exist that cannot be avoided, which could result in compressor damage.