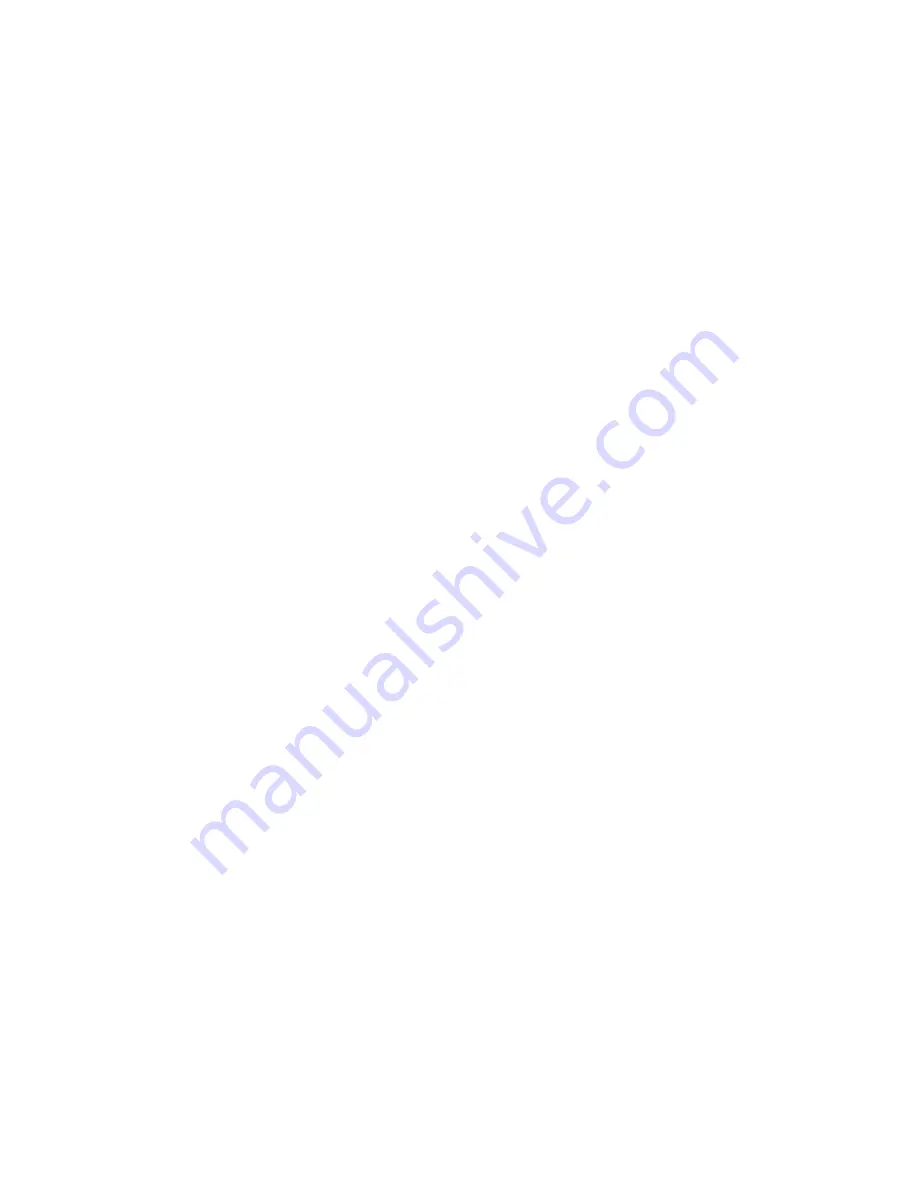
REFRIGERATION
COMPRESSOR
Scroll compressors are used as standard for models CNX150 - CNX300 and semi-hermetic reciprocating compressors
are standard for models CNX360 - CNX2M00 except for model CNX2M40 available with semi-hermetic compact screw
compressors. All compressors are conforming to ARI 540. The compressors are equipped with internal motor protection;
factory installed crankcase heater and rubber vibration isolators for quiet and efficient operation. As an option, semi-
hermetic compressor can be fixed on anti vibration mounting (spring type) along with suction & discharge line vibration
eliminators. Oil pressure control is provided on units with semi-hermetic compressor only. Each compressor has lock-out
devices to protect it from short cycling when tripped by safety controls. Each compressor has separate condenser coil
with safety controls. Sight glass and filter dryer are standard for all models.
Semi-hermetic Compressor:
These Semi hermetic reciprocating compressors are accessible –hermetic type. Compressor and motor are enclosed in
a hermetically sealed housing, with out shaft seal. The compressors are equipped with an oil sight glass through which
the oil quantity and its conditions in the crankcase can be observed. These compressors can be disassembled in the field
for service.
Refrigerant-cooled motor –compressors have an oil pressure lubrication system. This system is supplied by a positive
displacement oil pump, working in either direction. It is protected by a screen and is made accessible for quick oil
pressure checking by a Schrader check valve. The use of oil pressure control safeguards the lubrication system. These
compressors can be provided with capacity control (optional). The use of unloading provides optimal part load capacities.
Semi-hermetic compact twin screw Compressor:
All compressors are compact semi-hermetic twin screw of the high capacity and efficiency due to its perfect profile form
ratio 5:6. Simple and robust construction with slider control valve for capacity unloading, suction/discharge shut-off
valves, check valve in discharge gas outlet, oil sight glass, oil fill/drain service valve, directly flanged-on three stage oil
separator with long-life fine filter 10 microns mesh size, robust axial bearings in tandem configuration, suction gas filter,
internal pressure relief valve and manual lock-out electronic protection system for thermal motor winding temperature,
phase reversal, discharge gas temperature protection controls
.
Scroll Compressors:
Scroll Compressors are used in some of these units. The major benefits being:
1.
Low Sound Level
: Quieter operation because of no dynamic suction and discharge valves action.
2.
Low vibration and discharge pulses.
3.
High Energy Efficiency
: Because of high volumetric efficiency it minimize pressure and heat transfer losses.
4.
High Capacity
: Due to its high mass flow and high compression ratios.
5.
High Durability
: With its robust design, few moving parts, low motor strains, large internal volume for liquid handling
makes this compressor highly reliable.
6.
High Charge Limit
: Therefore, lower applied costs as no suction accumulator required, no need for pump down
system and check valve in discharge line.
Low capacity can be caused by inefficient compressor, that is, the compressor does not pump sufficient quantity of
refrigerant, even though a full charge is available in the system.
Electrical and mechanical tests should be performed to determine if the compressor is defective. If the compressor is found
to be all right but the electrical components are defective, remove and replace the defective electrical components only.
Below are some tests that should be performed on the compressor to determine, if the compressor is defective.
1. Test compressor motor winding for ground.
2. Test compressor motor windings for continuity.
3. Test that compressor motor will run both without a load and under a load.
4. Test the current or ampere drawn.
5. Observe sound level of compressor.
To establish that the compressor suction and discharge valves are operating and holding properly, attach gauges to the
liquid and suction service valves. "Front seat" the liquid service valve.
32