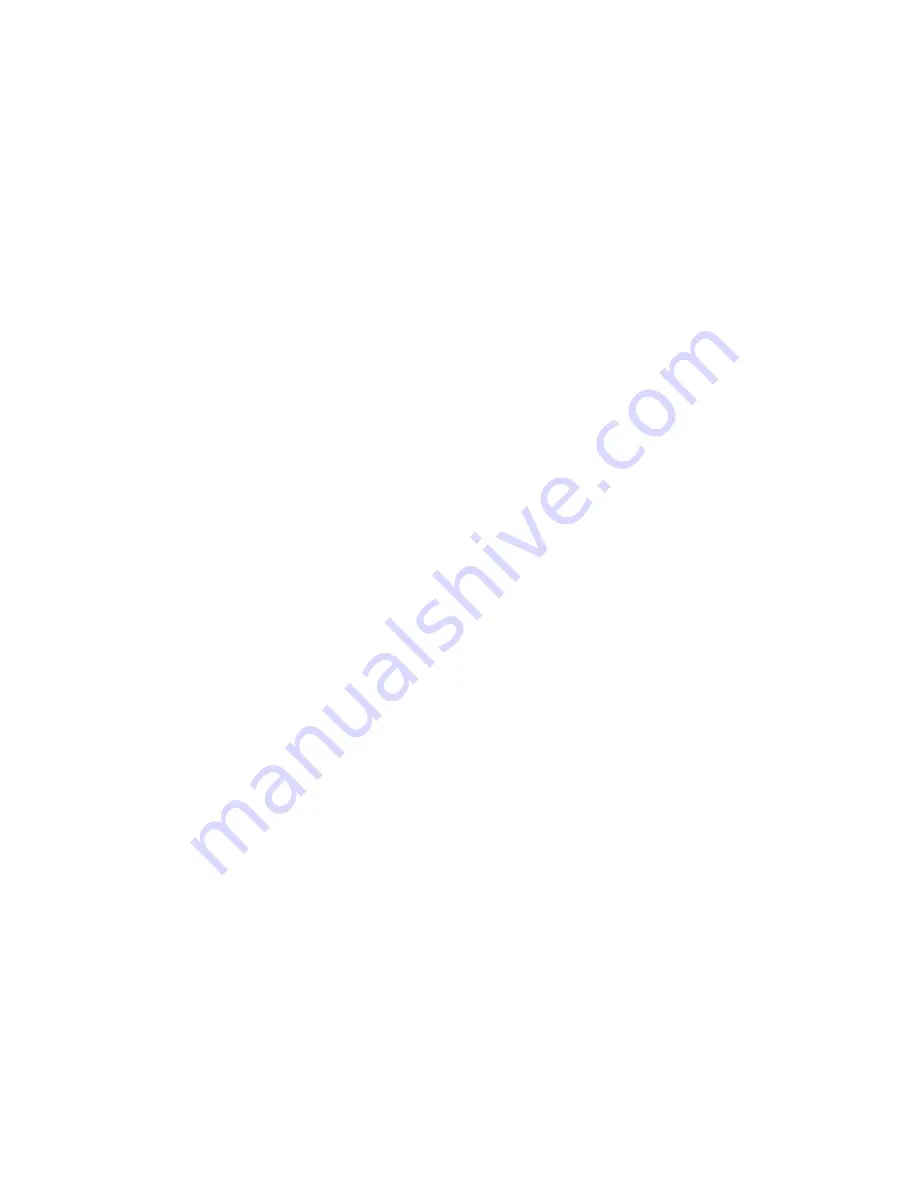
•
Duct Leakage Inside/Outside Building
•
Volume Dampers
•
Volume Damper Access Doors
•
Fire Dampers
•
Fire Damper Access Doors
•
Transfer Grilles/Door Grilles
•
Duct Insulation/Liner
•
Diffusers/Grilles
•
Duct Humidistat
•
Filter flag
CHECK-OUT & OPERATIONAL START-UP PROCEDURE
After the completion of inspection and check list, the following points should be covered before system is placed in operation.
1. Connect the manifold gauge to suction & discharge line service valves. Prepare recommended instruments for check-
ing Voltage, Amps, RPM, CFM, static pressure, etc.
2. Start the blower fan and condenser fan. Check the amperage against the nameplate ampere.
3. Start the compressor and observe the following points (on multiple compressor units, it is highly recommended to start
the compressors one by one to achieve careful observation for each compressor).
(a) Check compressor discharge and suction pressures. If not within system design limits, determine why and take
corrective action.
(b) Check liquid line sight glass and expansion valve operation. If there are indications that more refrigerant is required,
leak test all connections and system components and repair any leaks before adding refrigerant.
(c) Observe oil level in compressor crankcase sight glass (if available) and add oil as necessary to bring to recom-
mended oil level.
All compressors are charged with somewhat greater than the normal oil level required for adequate lubrication, in order
to provide some allowance for oil which will be circulating in the system during operation. Depending on the system
design, the amount of oil in the system at the time of compressor installation, oil lost due to leakage, etc., it may be
necessary either to add or remove oil from a system any time it is first placed in operation with a different compressor.
An abnormally low oil level may result in a loss of lubrication; while an excessively high oil level may result in oil
slugging and possible damage to the compressor valves or excessive oil circulation. The oil level may vary consider-
ably on initial start-up if liquid refrigerant is present in the crankcase, and the oil level should be checked with the
compressor running after having reached a stabilized condition.
(d) Thermostatic expansion valves must be checked for proper superheat settings. Recommended superheat is 15
0
F
to 20
0
F.
(e) Using suitable instruments, carefully check line voltage and amperage at the compressor terminals. Voltage must
be within ±10% of that indicated on the compressor nameplate. If high or low voltage is indicated, notify the power
company. The current normally should not exceed 110% of the nameplate rating. If amperage draw is excessive,
immediately determine the cause and take corrective action. On three phase compressor motors, check to see
that a balanced load is drawn by each phase.
(f) Carry out any necessary tests, recording airflow rates, entering/leaving temperatures, sound levels, outdoor tem-
peratures, supply airflow rates in occupied spaces and any other specified parameters.
29