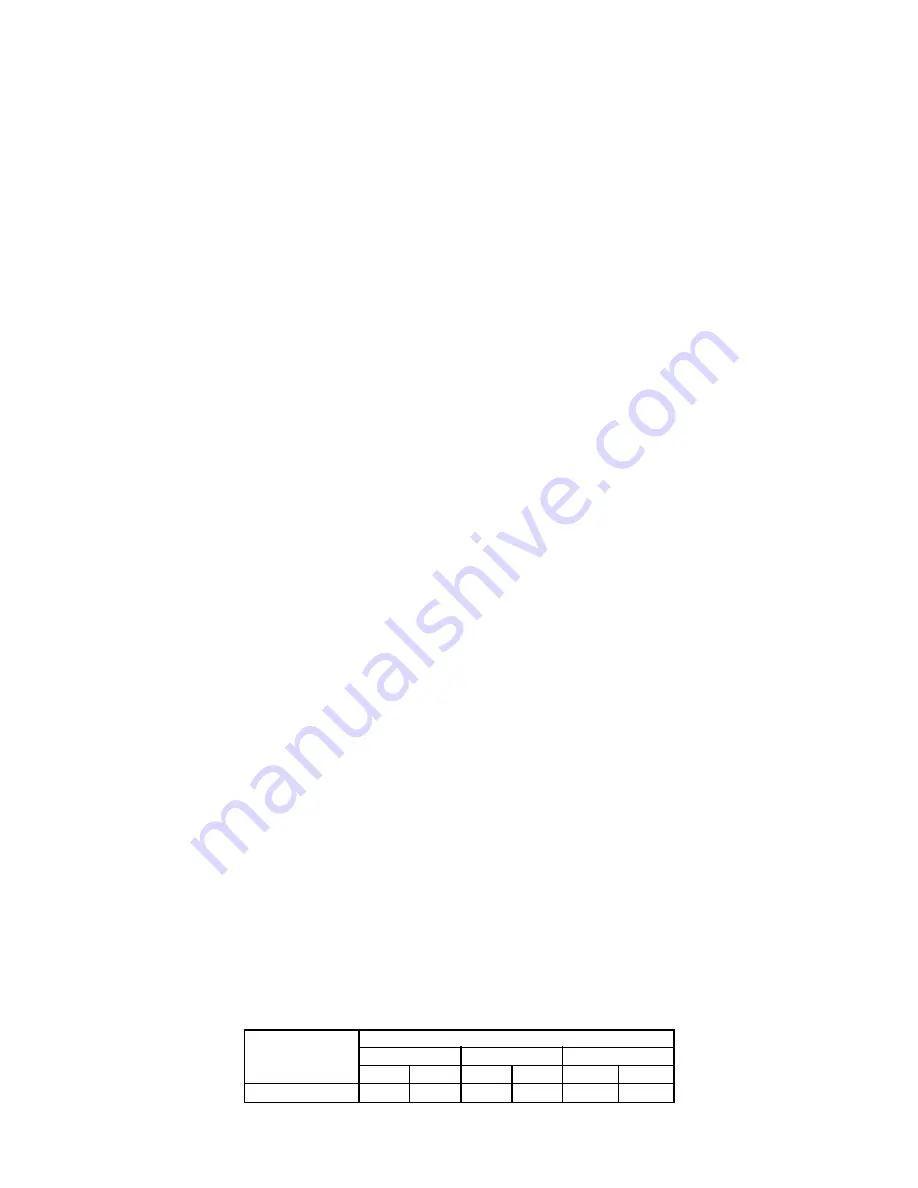
MOTOR CONTACTOR
The motor controller (contactor) is a load current carrying device which makes and breaks to start and stop the compres-
sor motor. The magnetic coil of the controller is energized to make and break the contactor contacts. Frequently, motor
contactors are subjected to quick cycling due to various causes. This may cause burned and/or sticking contacts and can
cause a compressor motor failure, even though the motor overload protectors trip and open the control circuit.
FAN MOTOR
The condenser fan motor is a single speed electrical motor with ball bearings, protected with an automatic reset internal overload.
CRANKCASE HEATERS
The function of the crankcase heater is to hold the compressor oil reservoir at a temperature higher than the coldest part
of the system. The low wattage heaters are energize continuously and it is not necessary to have them de-energize when
the compressor is operating.
Power must be supplied to crankcase heater for minimum of 12 hours prior to system start up. If power is off 6 hours or
more, crankcase heater must be on for 12 hours before operating the system. Failure to follow these instructions may
result in compressor damage.
Crankcase heaters are effective to retard migration of liquid refrigerant to the crankcase during off cycle. But they are not
a remedy for slugging or flood back due to liquid refrigerant accumulating in a trapped suction line, improper piping
practice, over feeding to the evaporator, leaking solenoid valve, etc.
In some cases where migration of refrigerant to the crankcase occurred due to long storage time, shutdown period,
defective components, etc. The crankcase heater may be ineffective. Such cases may be easily observed by high oil
level and cold crankcase. In these cases, it is highly recommended to front seat or close both suction and discharge
service valves of the compressor and release all liquid refrigerant from the compressor.
The liquid refrigerant dilutes the oil in the crankcase and the refrigerant rich oil will be pumped to the rods and the
bearings through the crankshaft. As the refrigerant boils off, there will not be enough oil for sufficient lubrication at the
bearings furthest from the oil pump. The center and rear bearings may seize or may wear enough to allow the rotor to
drop and drag on the stator causing it to short. Also the liquid refrigerant washes the oil off the pistons and cylinders
during the suction stroke causing them to wear during the compression stroke.
When the crankcase is filled with liquid refrigerant and the compressor starts severe agitation, oil foaming etc. will cause
major damage to the compressor.
Periodic checking for proper operation of crankcase heater is highly recommended.
LUBE OIL PROTECTION CONTROL
Pressure lubricated refrigeration compressors require a pressure protector in the event of an oil pressure failure. The
lube oil pressure protection control is factory set conforming to compressor manufacturer’s specification.
The control measures the net oil pressure available to circulate oil through the lubrication system. The positive displace-
ment oil pump circulates the refrigerant oil through the lubrication system. Since the oil pump is connected directly to the
compressor crankcase, the inlet pressure to the oil pump will always be the crankcase pressure. The oil pump outlet
pressure will be the crankcase pressure plus the oil pump pressure. Therefore, net oil pump pressure will always be the
pump outlet pressure minus the crankcase pressure.
The net oil pump pressure is sensed through a pressure transducer sending analogue signals to the unit’s microproces-
sor board. The control is set to trip or stop the compressor when oil differential pressure goes down at a pre-set level and
time delay setting. Trip settings for low oil pressure and time delay can be changed in the unit’s controller. Factory set
values for low oil pressure trip is at 30 psi after a time delay of 180 seconds.
VOLTAGE MONITOR
This device protects the motors in the unit from faults such as; under or over voltage, unbalance & phase reversal of the
power supply. When the device sensed such faults, it will cut-off the supply in the control circuit thereby cutting off power
to the motors. The voltage monitor will re-set automatically when power is brought back to it’s normal conditions.
31
LINE VOLTAGE
RANGE
UNDER VOLTAGE
TRIP
90%
190 - 480 VAC
TRIP & RE-SET VOLTAGE (% OF SET POINT)
OVER VOLTAGE
PHASE IMBALANCE
RE-SET
93%
TRIP
110%
RE-SET
107%
TRIP
6%
RE-SET
4.5%