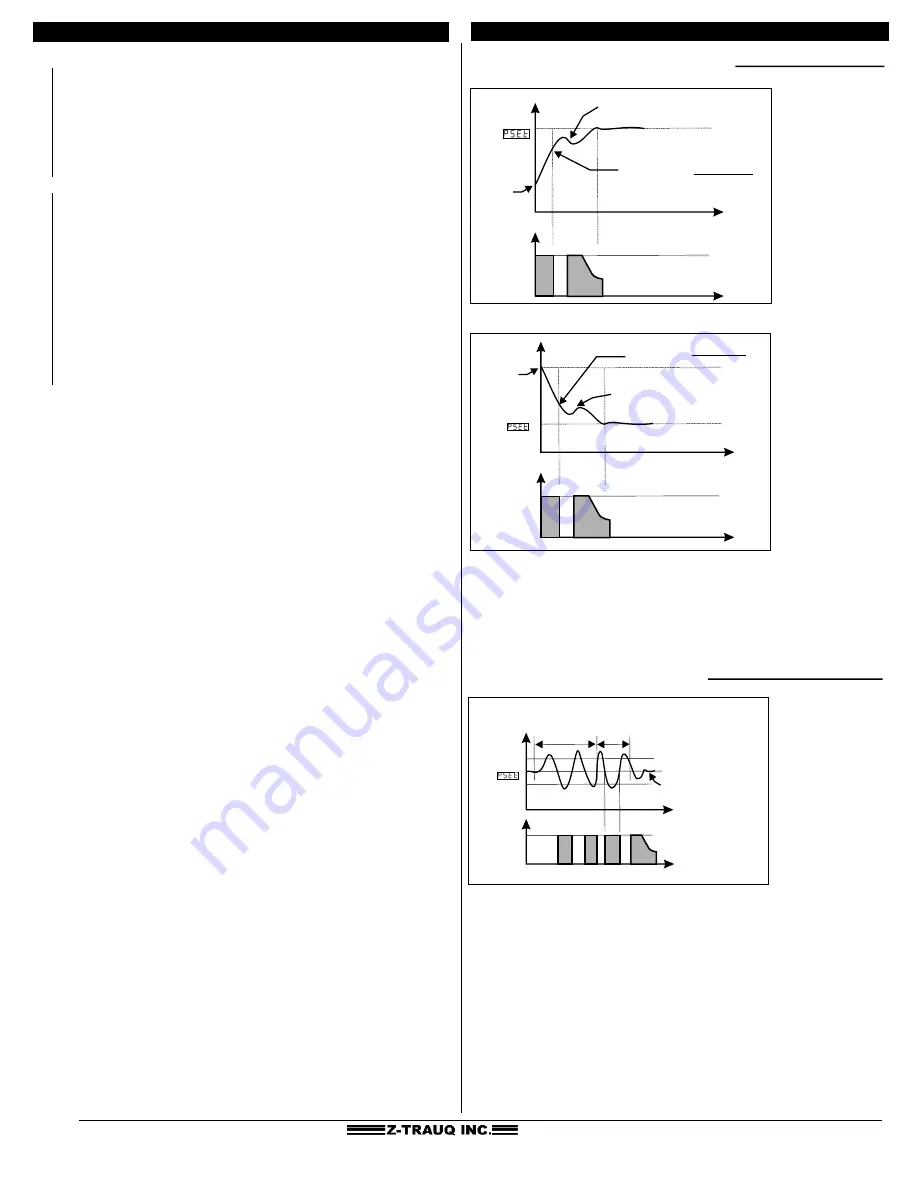
Passwords (PASS ConF)
opps
Operator password (0 to 9999).
Tcps
Technician password (0 to 9999).
SAdr
Slave Address from 1 to 247
Communication Configuration (Comm Conf)
BAud
Baud Rate: 0- 1200
1- 2400
2- 4800
3- 9600
4- 19200
Prty
Parity
0- none
1- ODD
2-EVEN
StPb
Stop Bit
0- 1 stop bit
1- 2 stop bit
Manufacturer’s Calibration Page (PASS CAL) - Factory Set
Explanations
Firstly, the control form must be PID in order for this tuning method to operate.
PID coefficients
save to
memory.
parameter is
changed
t
PID coefficients
save to
memory.
parameter is changed
t
If the tunn parameter is
Stun or At.St, step response
tuning is selected. When
t h e d e v i c e i s f i r s t
energized, the actual value
is compared to the set
value. If the set value is
greater than the actual
value, the process output is
enegized until the
start value+((set value)/2)
is reached. The process
output is reduced to 0% and
the device ensures that the
temperature has begun to
fall. The
are calculated and
d
If the tuning is
completed successfully,
the tunn
from Stun to NO or At.St o Atun depending on the original choice.
If the set value is less than
the actual value and the
cooling PID is selected, the
process output is energized
until the
start
value-((set
value)/2)
is reached
.
The process
output is reduced to 0% and
the device ensures that the
temperature has begun to
rise. The
are calculated and
d
If the tuning is
completed successfully, the
tunn
from Stun to NO or At.St o
Atun depending on the
original choice.
During tuning, the set value
can not be changed. Step
response is canceled without changing the PID set values when any of the following conditions
applies: the heating PID is canceled during Heating step response; when the cooling PID is canceled
during Cooling step response; when there is a sensor break error or when the step response tuning
operation can not be completed within 8 hours (the AT LED flashes. The error can be cleared with the
“SET” button). If the power to the device is removed and reapplied, the device carries out step
response tuning again.
Firstly, the control form must be PID in order for this tuning method to operate.
The user can decide at any
time to use this tuning
method by selecting Atun
or At.St for the tunn
parameter in the run list.
After changing the set
value, if the difference
between the newly defined
and former set values is
g r e a t e r t h a n t h e
proportional band
+/-(scale x P-Ht)/1000
if
heating or heating/cooling
or
+/-(scale x P-CL)/1000
if cooling, the contoller
will automatically start this
function.
In the event that the actual value moves outside the set value by
+/-Strn
3 times while the device is
executing the PID control, the Attn parameter becomes YES and tuning is started.
If the Attn parameter is YES, the device begins tuning from the point where it stands at that moment. If
the heating and cooling PIDs are selected together, or if only the heating PID is selected, Heating Limit
Cycle is performed; if only the cooling PID is selected Cooling Limit Cycle is carried out. If the Limit
Cycle operation can not be completed within 8 hours, tuning is cancelled and the Attn parameter
becomes NO. The PID parameters remain as they were before this failed session.
If Heating Limit Cycle is being done, tuning is performed according to
set-((set temperature)/4),
if
cooling Limit Cycle is being done, tuning is performed according to
set+((set temperature)/4)
.
At the end of tuning the Attn parameter becomes NO and the PID parameters are saved to memory.
If a sensor break error occurs, the tuning operation is paused until the sensor connection is re-
established. When the sensor connection returns to normal, the tuning operation is recommenced. If
the Limit Cycle tuning operation can not be completed within 8 hours the tuning operation is cancelled
(the AT LED flashes. The error can be cleared with the “SET” button).
While the tuning operation is under way, the Process Set Value (PSEt) can not be changed.
P.5
1-877-798-7287
Process
Value
Time
During
Atun
operation
100%
Process
Output
Control is
unstable
PID coefficients are
determined and system
becomes stable.
Process Set
Value ( )
Time
LIMIT CYCLE TUNING (Auto Tune)
Process
Value
Time
100%
Process
Output
Stun
Start
Value
PID coefficients are determined
and system becomes stable.
Start Value + [ ( Set Value) ]
2
Process Set
Value ( )
Time
STEP RESPONSE TUNING (Self Tune)
Process
Value
Time
100%
Process
Output
Stun
Start
Value
Process Set
Value ( )
Start Value - [ ( Set Value) ]
2
PID coefficients are determined
and system becomes stable.
Time
ESM 7750 v10R7
SU-L
SV min. limit. Adjustable from min. scale to
SU
-u
value . It’s the minimum value of
the operation scale.
out3
Output configuration (
heat
,
cool
,
Lout
)
Con3
Control type (ON/OFF or PID)
HYS3
Hysteresis value 0% to 50% of FS (expressed in degrees)
tm3
Minimum OFF time (0.0 to 100.0 seconds). Active in on.off control
Lou3
0=Alarm output
1=Manual / Automatic data output
2=Sensor break alarm
3=Output active when PV is outside operating range
4=Output activates at end of R/S 5=Analog input module sensor break alarm
6=PV of second input is <LoL1 / 2 or >uPL1 / 2
aLt3
Alarm type:
0-Process high alarm
1-Process low alarm
2-Deviation high alarm
3-Deviation low alarm
4-Deviation band alarm
5-Deviation range alarm
6=Heater failure alarm (CT input module must be installed)
NOTE: 2,3,4,5,are not available if Lou3
…
0.
aLH3
Alarm hysteresis. Active if output 3 is alarm output. If ALS3=0 or there is no second
sensor input, adjustment is 0 - 50% of process input scale (uPL-LoL).
If ALS3=1and an analogue input is present, then it can be adjusted from 0 to 50% of
the input module’s scale.
If a CT input module is installed and ALt3=0006, adjust from 0.0 to 20.0A.
SU-u
SV max. limit. Adjustable from
SU-L
value to max. scale. It’s the maximum
value of the operation scale.
HYn3
Mode of Hysteresis
0=SV+(HYS/2) and SV-(HYS/2)
1=SV and SV+HYS or SV and SV-HYS
Output - 3
If Module 1 or 2 is EMI-410, EMI-430, EMI-440 or EMI-450 (continued)
RTS1 / 2
Selection of sensor type and scale (see Table 1)
UNT1 / 2
°C=Centigrade
°F=Fahrenheit
LoL1 / 2
Minimum value of second sensor input range
uPL1 / 2
Maximum value of second sensor input range
IPu1 / 2
Module 1 / 2 PV offset ±10% of FS1. Added to the input reading in degrees
iFL1 / 2
Module 1 / 2 Input signal filtering time. (From 0,0 to 900,0 secs)
rES1 / 2
Determines whether the measured value is the result of the input on
terminals 1,2, 3 or from the input module. Visible only when decimal point
and unit parameters are the same for both inputs. If YES, then analogue
input module
’
s value is used as the Set Value. If NO, then SV=PSET
Parameters
UAS1 / 2
Selection of sensor type and scale. (See Table1)
DPN1 / 2
Analogue input module decimal point position
0 = 9999
1 = 999.9
2 = 99.99
3 = 9.999
ICA1 / 2
Analogue input module calibration
type
0 = None
1 = Dual point
ICL1 / 2
Minimum value for dual point calibration
ICH1 / 2
Maximum value for dual point calibration
uNT1 / 2
°C=Centigrade
°F=Fahrenheit
U=Other units
LoL1 / 2
Minimum value of second sensor input range
uPL1 / 2
Maximum value of second sensor input range
Ipu1 / 2
Module 1 / 2 PV offset ±10% of FS1. Added to the input reading.
iFL1 / 2
Module 1 / 2 Input signal filtering time. (From 0
.
0 to 900
.
0 secs)
rES1 / 2
Determines whether the measured value is the result of the input on
terminals 1,2, 3 or from the input module. Visible only when decimal point
and unit parameters are the same for both inputs. If YES, then analogue
input module
’
s value is used as the Set Value. If NO, then SV=PSET
I
SL1 or
I
L2=
1
f
I
S
If
I
L
L2=
S
1=
or
IS
2
General Configuration (Genn ConF)
Su-L2
Second sensor SV min. limit. Adjustable from min. scale to
SU
-u
2
value .
It’s the minimum value of the operation scale.
SU-u2
Second sensor SV max. limit. Adjustable from
SU-L
2
value to max. scale.
It’s the maximum value of the operation scale.
ALS3
Alarm sensor selection. If output 3 is an alarm output and an analogue module is
installed:
0 = Alarm in accordance with input sensor (on terminals 1,2,3)
1 = Alarm in accordance with analogue input module (1 or 2)
Alarm delay from fault 0.0 to 9999 seconds
Aon3
Alarm reset from fault 0.0 to 9998 seconds.
For high limit with manual reset only, select 9999. Display will read LtCH to indicate
latch feature has been selected.
AoF3
ULtt
Motorized valve travel time can be adjusted from 5 to 600 sec.
ULHY
Min. activation time of motorized valve and is adjustable from 0.1 to 5.0%.
eg. If ULtt=100s and ULHY=1.0% then the minimum activation time is (100s*1%) or
1 second.
Содержание ESM 7750
Страница 2: ...17 18 output 3...