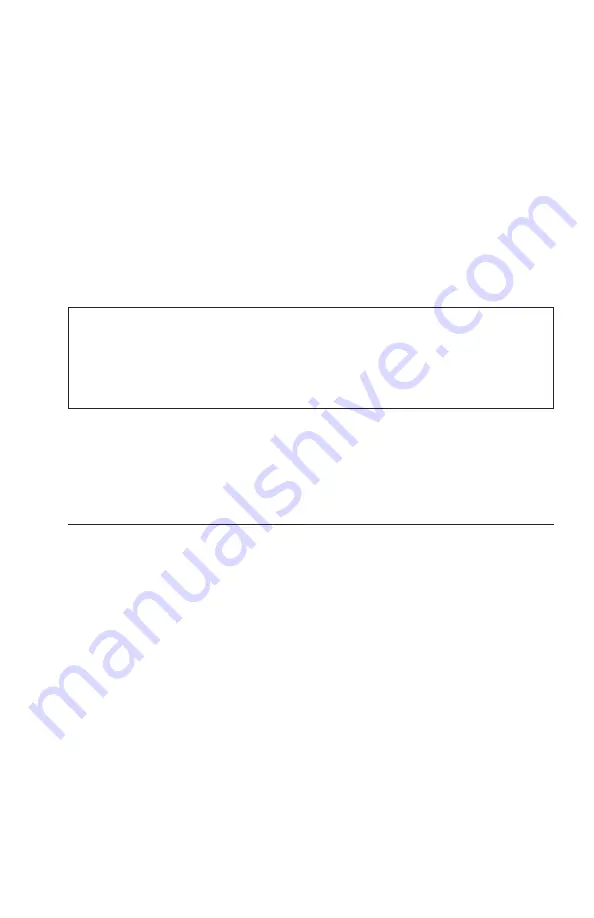
31
Mechanical cleaning
: In order to sand the silver anode along the shaft
of the sensor, simply hold the sensor in a vertical position. Wet the
sanding disc and gently wrap it around the sensor and twist it a few
times to lightly sand the anode (the goal is to simply sand off any
build-up without scratching or removing layers of the anode itself).
Usually, 3 to 4 twists of the sanding disc are sufficient to remove
deposits. However, in extreme cases, more sanding may be required
to regenerate the original silver surface.
After completing the sanding procedure, repeatedly rinse the electrode
with clean water and wipe with lens cleaning tissue to remove any grit
left by the sanding disc. Thoroughly rinse the entire tip of the sensor
with distilled or deionized water and install a new membrane.
IMPORTANT
: Be sure to: (1) Use only the fine sanding discs
provided and (2) Sand as mentioned in the above procedures.
Not adhering to either of these instructions can damage the
electrodes.
i
If this procedure is unsuccessful, as indicated by improper sensor
performance, contact YSI Technical Support or the Authorized dealer
where you purchased the instrument.
Galvanic Sensors – Model # 605202
We recommend that the Sodium Chloride (NaCl) solution and the
membrane cap be changed at least once every 60 days during regular
use. In addition, the NaCl solution and membrane should be changed
if (a) bubbles are visible under the membrane; (b) significant deposits
of dried electrolyte are visible around the membrane; and (c) if the
sensor shows unstable readings or other sensor-related symptoms.
The Galvanic dissolved oxygen sensor is continuously reducing
oxygen even when the display of the instrument is not active. This
factor allows the sensor to be used with no warm-up period as soon as
the instrument is powered on (instant on DO). However, because the
sensor is “on” all the time, some solid from the oxidation of the zinc
anode will form in the electrolyte within 1-2 weeks of activation. Small
amounts of the solid will generally cause no performance problems,
but excessive amounts may result in jumpy dissolved oxygen readings.
The rate of solid formation is dependent on the type of membrane
installed. The formation of solids based on membrane type typically
form more rapidly with 5913 (1.25 mil PE), and less rapid with 5914 (2
mil PE).