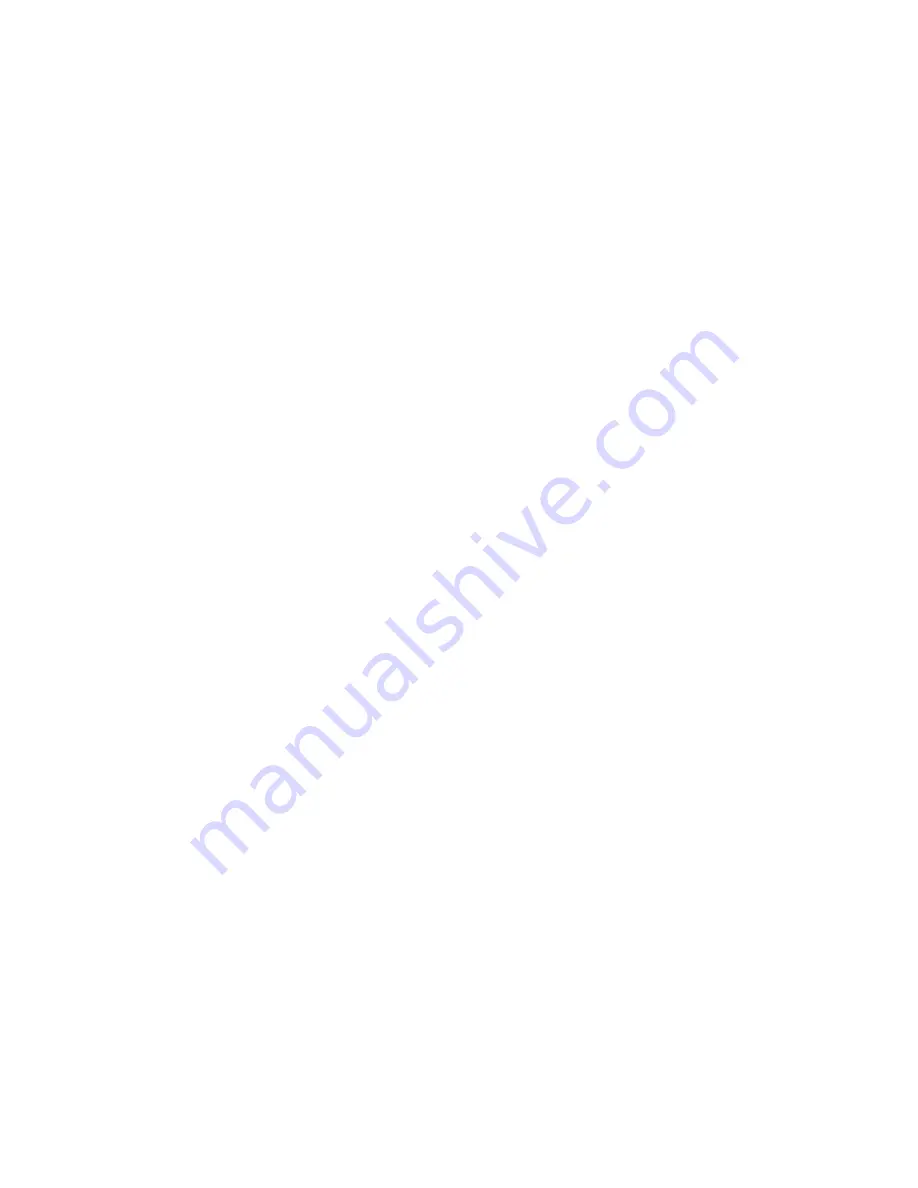
JOHNSON CONTROLS
78
FORM 160.67-O2
ISSUE DATE: 10/9/2020
SECTION 6 - MAINTENANCE
4.
After the tubes have been corked for 12 to 24
hours, it is recommended that two men working
at both ends of the evaporator carefully test each
tube – one man removing corks at one end and
the other at the opposite end to remove corks and
handle the leak detector. Start with the top row of
tubes in the section being investigated. Remove
the corks at the ends of one tube simultaneously
and insert the exploring tube for 5 seconds – this
should be long enough to draw into the detector
any refrigerant gas that might have leaked through
the tube walls. A fan placed at the end of the evap-
orator opposite the detector will assure that any
leakage will travel through the tube to the detec-
tor.
5. Mark any leaking tubes for later identification.
6.
If any of the tube sheet joints are leaking, the leak
should be indicated by the detector. If a tube sheet
leak is suspected, its exact location may be found
by using a soap solution. A continuous buildup of
bubbles around a tube indicates a tube sheet leak.
COMPRESSOR MAINTENANCE
Maintenance for the compressor assembly consists of
checking the operation of the oil return system and
changing the dehydrator, checking and changing the
oil, checking and changing the oil filters, checking the
operation of the oil heater, checking the operation of
the oil pump, and observing the operation of the com-
pressor.
Internal wearing of compressor parts could be a serious
problem caused by improper lubrication, brought about
by restricted oil lines, passages, or dirty oil filters. If
the unit is shutting down on COMPR OIL - HIGH
TEMPERATURE or COMPR OIL - LOW DIFFER-
ENTIAL PRESSURE, change the oil filter element.
Examine the oil filter element for the presence of alu-
minum particles. Aluminum gas seal rings can contact
the impeller and account for some aluminum particles
to accumulate in the oil filter, especially during the ini-
tial start up and first several months of operation. How-
ever, if aluminum particles continue to accumulate and
the same conditions continue to stop the unit operation
after a new filter is installed, notify the nearest Johnson
Controls office to request the presence of a Johnson
Controls Service Technician.
STEAM CONDENSER CONDENSATE PUMP
MAINTENANCE
While the pump is running, re-grease the pump bear-
ing with #2 lithium base petroleum grease. This should
be done after every 2500 hours of operation or every 6
months, whichever occurs first. Lubricate the motor
per the instructions on the nameplate.
STEAM CONDENSER VACUUM PUMP
MAINTENANCE
After approximately 3 years of operation, the rolling-
contact bearings and the adjacent spaces should have
the spent grease and other dirt deposits removed and be
repacked with fresh grease. The pump must be disas-
sembled for this procedure. UNIREX N3 or equivalent
grease per DIN51825-K3N must be used. Different
types of grease should not be mixed. Fill 50% of the
free hollow space in the deep-groove ball bearing at
the impeller end with grease. Fill the deep-groove ball
bearing at the motor end flush. Do not fill the bear-
ing caps as his could result in an excessive amount of
grease. When re-lubricating or replacing rolling-con-
tact bearings, inspect and replace any worn seals such
as the V ring.
TURBINE INTERNAL INSPECTION
To perform the thorough periodic inspections, it will
be necessary to remove the turbine cover. Housed un-
der that cover are diaphragms, the turbine rotor, nozzle
block, shaft seals, the stationary blade segment, and the
casing interior. Refer to SECTION 7 - STEAM PURI-
TY/TURBINE DEPOSITS for additional information.
Inspection of other parts, such as bearings, governor
and linkage, oil pump drive assembly, governor valve
and trip valve, can be accomplished without casing
cover removal.
Where turbines have a top exhaust, the inspection pro-
cedure is more involved since the exhaust pipe must
first be removed to provide the necessary free space
above the turbine. The casing cover can then be re-
moved by the following procedure:
It should be remembered that the casing assembly is
a pressure tight vessel and that all joints are necessar-
ily sealed to prevent steam leakage. These include the
main horizontal casing flange, gland case splits and
vertical surfaces.