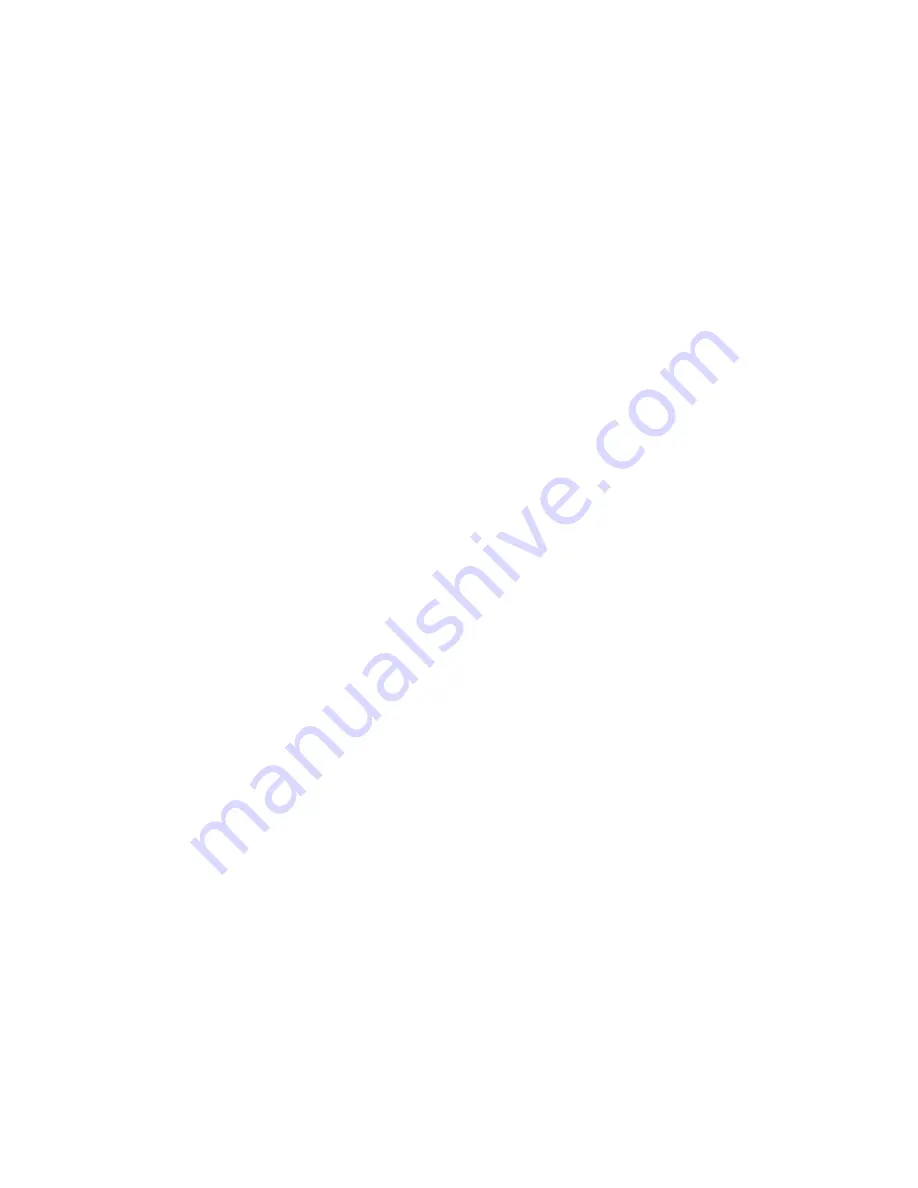
JOHNSON CONTROLS
50
FORM 160.67-O2
ISSUE DATE: 10/9/2020
SECTION 3 - SYSTEM COMPONENTS DESCRIPTION
GENERAL
The YORK Model YST Centrifugal Liquid Chiller
Unit is completely factory-packaged including; the
evaporator, refrigerant condenser, compressor, steam
turbine, lubrication systems, power panel, control cen-
ter, and all interconnecting unit piping and wiring. The
steam condenser package is shipped separately and
suitable for direct mounting onto the chiller or mount-
ing along side the chiller. (Refrigerant and oil charges
shipped separately unless optional condenser isolation
valves are ordered.)
Chillers can also be shipped dismantled when required
by rigging conditions, but generally it is more econom-
ical to enlarge access openings to accommodate the
factory assembled unit. Chillers shipped dismantled
MUST be field assembled under the supervision of a
Johnson Controls representative, but otherwise instal-
lation will be as described in this instruction.
COMPRESSOR VARIABLE GEOMETRY
DIFFUSER (VGD)
Certain YORK compressors are equipped with a Vari-
able Geometry Diffuser (VGD). It is used to reduce ro
-
tating stall conditions and associated stall noise. Stall
may occur at low load conditions with high head. A me-
chanical ring, located in the diffuser passage after the
impeller discharge, is mechanically operated through
linkages via an electric actuator like that used to op-
erate the pre-rotation vanes. It is closed (extended) to
narrow the diffuser gap. It is opened (retracted) to open
the diffuser gap. An internal actuator end switch pre-
vents travel beyond the fully open or closed positions.
In response to a stall condition, the ring is closed as
much as necessary to eliminate the stall. Since stall is
caused by reduced gas flow through the compressor,
narrowing the diffuser gap reduces the cross sectional
area through which the gas flows, thereby increasing
the gas velocity through the compressor.
A stall pressure transducer mounted in the discharge
scroll of the compressor, detects the pressure pulsa-
tions created by the stall noise in the compressor dis-
charge and outputs DC voltage pulsations to the stall
detector board in the OptiView™ Control Center. This
board converts the voltage pulsations into an analog
voltage that represents the magnitude of the stall noise.
This analog voltage is displayed on the Variable Ge
-
ometry Diffuser Screen as “Stall Detector Voltage”
and is input to the Microboard where it is compared to
the Low Limit and High Limit setpoint thresholds to
determine if the stall noise is acceptable or unaccept-
able. The control logic manipulates the VGD actuator
as necessary to eliminate the stall noise.
Refer to the
OptiView™ Control Center Service Instructions Form
160.67-M1 for additional details.
COMPRESSOR LUBRICATION SYSTEM
To provide the required amount of oil under the neces-
sary pressure to properly lubricate these parts, a motor
driven submersible oil pump is located in a remote oil
sump.
Lubrication oil is force-fed to all bearings, gears and
rotating surfaces by the variable speed drive pump
which operates prior to startup, continuously during
operation and during coastdown.
There are main points within the unit which must be
supplied with forced lubrication as follows:
1. Compressor Drive Shaft (Low Speed)
a. Shaft seal.
b. Front and rear journal bearings – one on
each
side of driving gear.
c. Low speed thrust bearing (forward and re-
verse).
2. Compressor Driven Shaft (High Speed)
a. Forward and reverse high speed thrust bear-
ing.
b. Two journal bearings.
3. Speed Increasing Gears
a. Meshing surfaces of drive and pinion gear
teeth.
There is a price option to add dual oil filters on both the
compressor and KD steam turbine. (The KG turbine
has no oil filter.) This provides the capability of chang-
ing the oil filters while the system is in operation. The
external oil sump is vented to the compressor suction
to permit refrigerant gas that is boiled off by the elec-
tric heater in the oil to equalize back to the system.