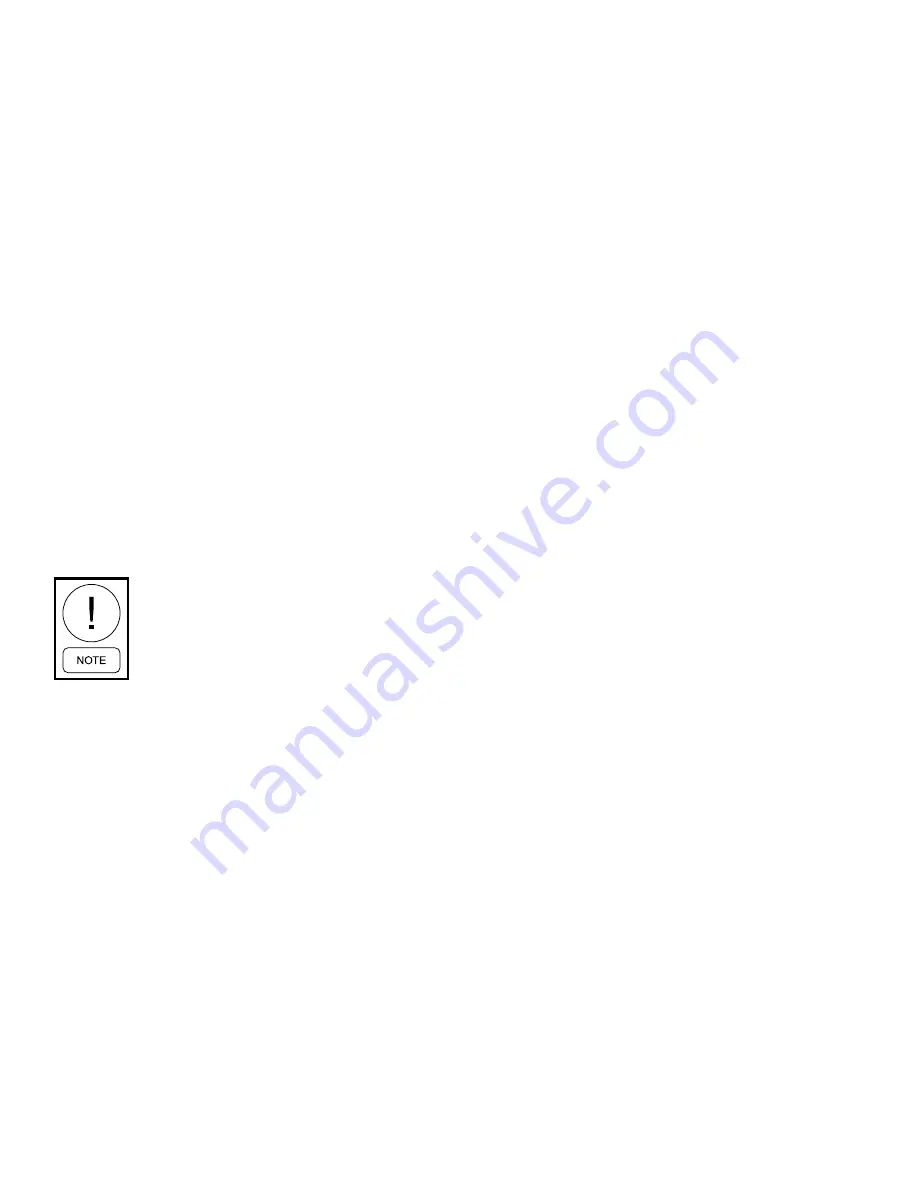
JOHNSON CONTROLS
56
FORM 160.67-O2
ISSUE DATE: 10/9/2020
SECTION 3 - SYSTEM COMPONENTS DESCRIPTION
•
Steam finds its way to the bearing housings, con
-
denses there and contaminates the oil.
•
Efficiency is reduced since escaped steam produc
-
es no useful work.
• Each pound of steam lost requires adding one
pound of make-up water to the boiler.
• Excessive leaks cause an unpleasant working at-
mosphere.
The gland leak-off system for non-condensing appli-
cations and the gland seal system for condensing ma-
chines, are used to minimize leaks. This is achieved
with a system that permits steam leakage where the
gland seals make contact with the shaft, using the pres-
sure differential between them as an effective seal. A
leak-off connection, just before the exterior inactive
seals, is designed so steam reaching that point will run
through it instead of the seals.
Gland seals can either be of the segmented carbon ring
type, the labyrinth type or a combination of both. Un-
less one of these two types is specifically mentioned in
this section they will simply be referred to as “gland
seals”.
Carbon Ring Type Glands Have Excel-
lent Sealing Capabilities When New But
Are Subject To Wear. They Should Be
Replaced Every One To Three Years. Note
That They Lose Effectiveness When The
Pressure Differential Is Excessive.
Usually, a single leak-off system is enough to seal
those turbines operating with moderate temperatures
and pressures. If a more effective seal is necessary, or
if the working pressures are higher, a double leak-off
system is used.
In these cases, leak-off connections closer to the cas-
ing (interior leak-offs) are connected to the same pipe
and to a header with a steam pressure of 10-20 PSI
(non-condensing turbine) or 1-5 PSI (for condensing
machines). Exterior connections are either piped to the
atmosphere or to an evacuation device.
The best system for any specific application depends
upon the pressures involved, the required efficiency,
and the availability of low pressure lines at the instal-
lation site.
Gland Seal System: Standard YST
Condensing Turbines
Turbines are equipped with a gland seal system similar
to that of non-condensing machines, although the func-
tion is different. The purpose of the sealing system is
to keep outside air from leaking into the casing since
it would reduce the vacuum and cause a loss of power.
The system is not as effective when the machine is
standing idle as when it is operating.
The exhaust pressure in the casing is always below
atmospheric pressure. In the majority of condensing
turbines, the casing pressure is also below atmospheric
when operating without load but rises above atmo-
spheric, in proportion to the increase in power, when a
load is added. As load is applied, steam from the inlet
gland will escape through the leak-off and supply seal-
ing to the exhaust gland.
As the amount of steam moving through the leak-off
connection rises, the excess leak-off steam is dis-
charged to the atmosphere or some evacuation device.
Gland Seal Wear
As time goes on, the normal wear of the seals will re-
sult in more steam passing out the leak-off line to sew-
er. The steam required to seal the exhaust gland may
go up some, but not as much as the increase in leakage
from the steam gland. Eventually the seals will wear to
the point where there will be more steam trying to leak
to sewer than the line can handle without causing some
backpressure on the seal steam header. This will cause
condensate to start dripping from the exhaust gland. At
that time, the leakage will be excessive from the steam
gland and the seals should be replaced.
Gland Seal Leak-Off Piping
Where the rotor shaft passes through the turbine cas-
ing, packing glands of the segmented carbon ring or
labyrinth type are provided. These have leak-off con-
nections piped to a common point.
From This Point,
The Customer Must Provide Suitable Piping Of A
Size Indicated On The Outline Drawing.
If it is necessary to run the pipe for a long distance the
size should be increased so that back pressure does not
build up on the packing gland. This pipe must slope
down from the connection point to avoid forming a wa-
ter trap and must not contain a shut-off valve.
A small amount of steam will pass through this line at
all times. The amount of steam passing through the line
will depend upon the amount of back pressure.