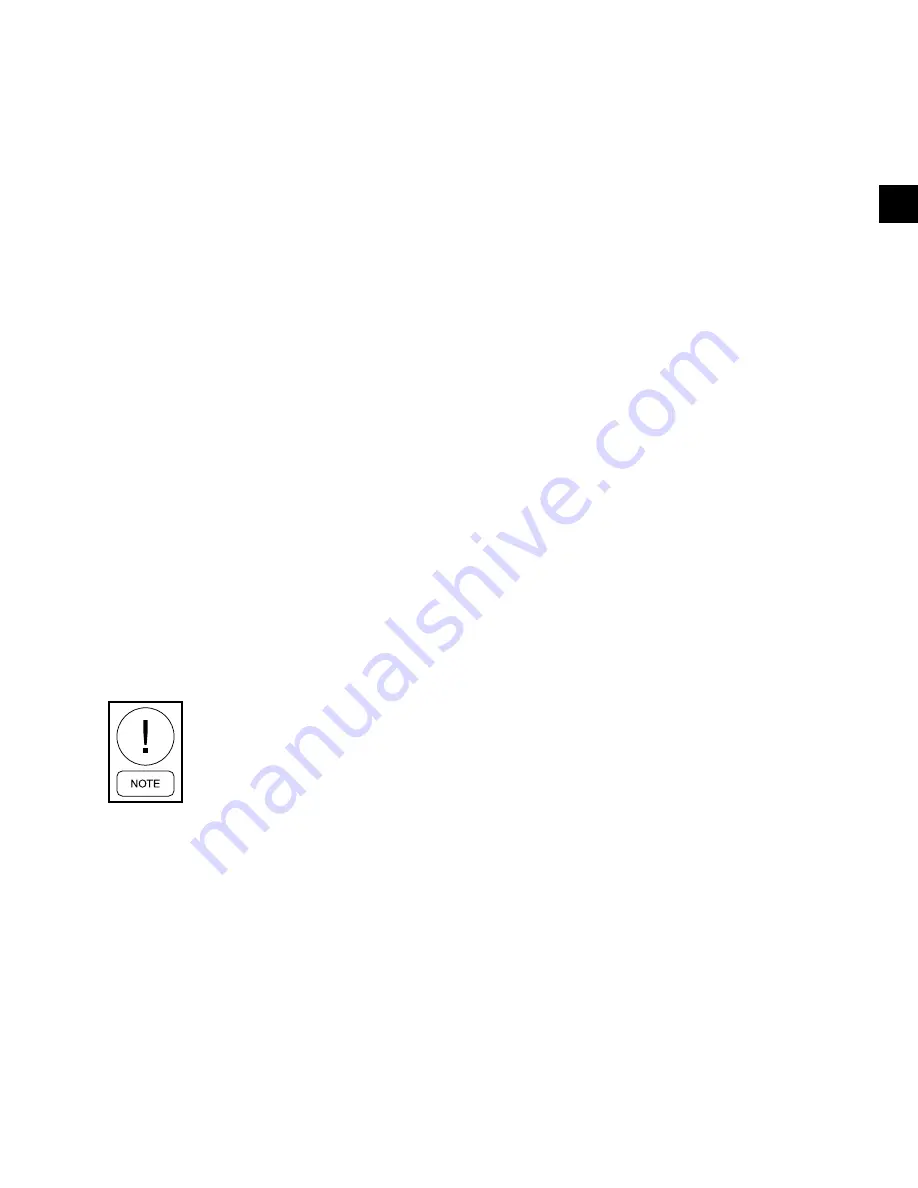
JOHNSON CONTROLS
53
SECTION 3 - SYSTEM COMPONENTS DESCRIPTION
FORM 160.67-O2
ISSUE DATE: 10/9/2020
3
Blanket insulation is furnished on the steam chest and
barrel of the turbine for operator protection.
The turbine speed is controlled by a governor valve
which is integrated with the chiller controls. The valve
is made of stainless steel with stainless steel seats and
designed to control flow throughout the entire op-
erating range of the turbine. The system employs an
overspeed governor designed to close an independent
high performance butterfly trip valve with a pneumatic
actuator when the turbine speed exceeds 110 percent
of the maximum continuous operating speed of the tur-
bine. Activation of the independent trip valve activates
a limit switch on the trip valve linkage which is con-
nected to the chiller control center to initiate a shut-
down sequence and close the governor valve.
STEAM TURBINE INLET VALVES
The turbine requires a main steam block valve (sup-
plied by others) for isolation which remains closed
during the slow roll warm-up. This main block valve
should also be supplied upstream of the automated
valve (supplied by YORK) on Auto-Start design sys-
tems. A smaller valve called a slow roll bypass valve,
bypasses the main block valve and is opened to begin
the slow rolling warm-up. This valve is manual on
standard systems and is an automated valve on systems
with Auto Start. The main block valve is opened fully
when operating speed is reached and the bypass valve
Sequence Of Operation on page 26
of this manual for more details.
Chillers manufactured after December
2006 are NOT supplied with separate
automatic slow roll bypass and main inlet
steam valves.
For speed and overspeed control the turbine has two
additional valves in the steam supply. Both are auto-
matic valves. The governor valve is used to control the
turbine speed automatically from the control panel.
The other valve is the fast acting butterfly trip valve
which is operated by the chiller control center, the me-
chanical overspeed device, or the manual trip device
that can by actuated by the operator. Refer to the fol-
lowing TURBINE GOVERNOR AND OVERSPEED
CONTROLS section in this manual for additional de-
tails.
TURBINE BEARINGS
The turbine bearings perform two functions. The jour-
nal bearings support the rotor’s weight and the thrust
bearings protect the turbine against any type of exces-
sive axial displacement. These bearings are lubricated
by a pressurized or ring oil lubrication system.
The journal bearings on all turbines are of the hydro-
dynamic type, which means they operate by means of
an oil film between the contact surfaces to eliminate
metal-to-metal contact. The bearings are steel backed,
Babbitt lined, split sleeve type. The design is such that
the bottom half is removable with the shaft in place.
The normal clearances on the bearings are 0.005 to
0.007 inch for turbines with ring oil lubrication and
0.006 to 0.008 inch for turbines with pressure lubrica
-
tion.
The thrust bearings on KD turbines are double act-
ing thrust collars or multi-segmented tilting pad type.
Thrust collars are simply two rings, one at each side
of the journal bearing, holding the shaft in place. The
multi-segmented tilting pad type is self-adjusting so
that the thrust is equally divided among all the shoes
on either side of the collar. The thrust bearing is acces-
sible and removable without lifting the top half of the
turbine casing.
The thrust bearings on KG turbines are antifriction ball
bearings. They should be replaced each 20,000 hours
or when indicated by vibrations. The thrust bearing is
accessible and removable without lifting the top half of
the turbine casing.
TURBINE LUBRICATION SYSTEMS
Two types of lubrication are supplied on steam turbines
furnished on YST systems. The smaller turbine design,
KG, has an integral lube system and is used for designs
up to 1700 HP. The larger turbine design, KD, has an
external lube system and is used for designs above
1700 HP.