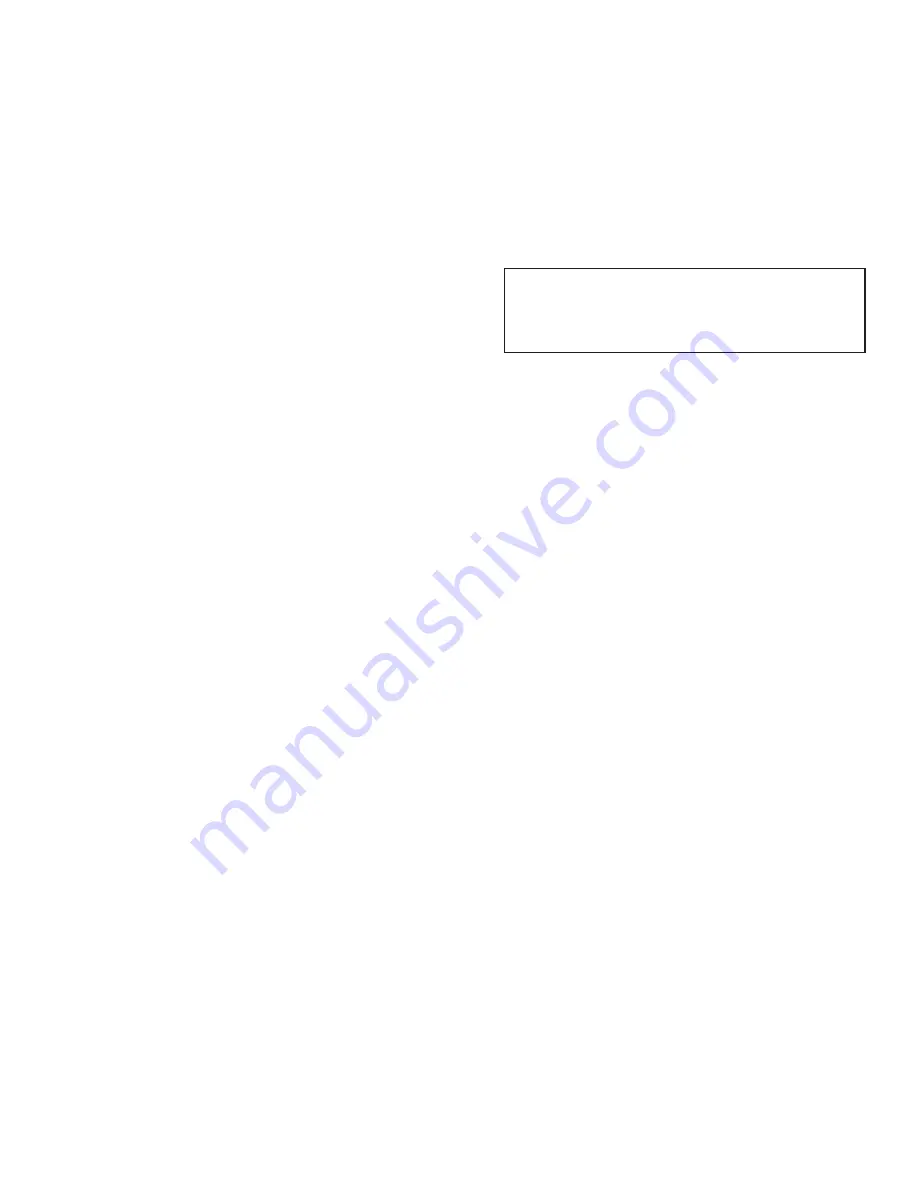
FORM 201.10-NM1
43
YORK INTERNATIONAL
Hand stop valves should be installed in all lines to
facilitate servicing.
Piping to the inlet and outlet connections of the chiller
should include high-pressure rubber hose or piping loops
to insure against transmission of water pump vibration.
This is optional and the necessary components must be
obtained in the field.
Drain connections should be provided at all low points to
permit complete drainage of the liquid cooler and system
piping.
A small valve or valves should be installed at the highest
point or points in the chilled liquid piping to allow any
trapped air to be purged. Vent and drain connections
should be extended beyond the insulation to make them
accessible.
The piping to and from the cooler must be designed to suit
the individual installation. It is important that the following
considerations be observed:
1. The chilled liquid piping system should be laid out so
that the circulating pump discharges directly into the
cooler. The suction for this pump should be taken from
the piping system return line and not the cooler. This
piping scheme is recommended, but is not
mandatory. Keep in mind that a pump whose suction
is taken from the evaporator may suffer performance
problems.
2. The inlet and outlet cooler connection sizes are 8".
3. A strainer, preferably 40 mesh, must be installed in
the cooler inlet line just ahead of the cooler. This is
important to protect the cooler from entrance of large
particles which could cause damage to the
evaporator.
4. All chilled liquid piping should be thoroughly flushed to
free it from foreign material before the system is
placed into operation. Use care not to flush any foreign
material into or through the cooler.
5. As an aid to servicing, thermometers and pressure
gauges should be installed in the inlet and outlet water
lines. One connection point (plugged) is provided in
each cooler nozzle. Thermometers and gauges are
not furnished by other suppliers.
6. The chilled liquid lines that are exposed to outdoor
ambients should be wrapped with supplemental
heater cable and insulated to protect against freeze-
up during low ambient periods, and to prevent
formation of condensation on lines in warm humid
climates.
7. A chilled water flow switch, (either by YORK or others)
MUST be installed in the leaving water piping of the
cooler. There should be a straight horizontal run of at
least 5 diameters on each side of the switch. Adjust
the flow switch paddle to the size of the pipe in which
it is to be installed. (See manufacturer’s instructions
furnished with the switch.) The switch is to be wired to
terminals in the control panel as shown in the WIRING
DIAGRAM.
WARNING
The Flow Switch MUST NOT be used to start and stop
the chiller. It is intended only as a safety switch.
COMPRESSOR INSULATION
In high humidity environments, compressor sweating
may be noted. In most applications, this is of no concern.
However, if it is undesirable, it is the responsibility of the
installer to make provisions to field insulate the
compressors or install factory insulation when the option
becomes available. Contact YORK Factory Marketing for
availability of factory supplied kits.
ELECTRICAL WIRING
Liquid Chillers are shipped with all factory mounted
controls wired for operation.
Field Wiring – Power wiring must be provided through
a fused disconnect switch to the unit terminals (or optional
molded disconnect switch) in accordance with N.E.C. or
local code requirements. Minimum circuit ampacity and
maximum dual element fuse size are given in the
ELECTRICAL DATA tables. A 115-1-60, 20 amp source
must be supplied for the control panel through a fused
disconnect when a control panel transformer (optional) is
not provided. Refer to Wiring Diagram (Page 52) in this
manual or Form 201.10-W1.
Affiliated apparatus, such as chilled water flow switch,
auxiliary contacts from the chilled water pump starter,
alarms, etc., should be interlocked into the control panel
circuit. These field modifications may be made as shown
on the WIRING DIAGRAM.
MULTIPLE UNITS
For increased compressor protection and to reduce power
inrush at start-up on multiple chiller installations,
provisions must be made to prevent simultaneous start-
up of two or more units. Also, some method must be
employed to automatically cycle one or more of the units
on or off to permit more efficient operation at part load
conditions.
Содержание Millennium YCAS 316
Страница 11: ...FORM 201 10 NM1 11 YORK INTERNATIONAL YCAS 140 246 DIMENSIONS English LD01444 LD01446...
Страница 13: ...FORM 201 10 NM1 13 YORK INTERNATIONAL YCAS 140 246 DIMENSIONS SI LD01440 LD01442...
Страница 15: ...FORM 201 10 NM1 15 YORK INTERNATIONAL YCAS 216X 266X DIMENSIONS English LD01454 LD01454...
Страница 17: ...FORM 201 10 NM1 17 YORK INTERNATIONAL YCAS 216X 266X DIMENSIONS SI LD01450 LD01448...
Страница 33: ...FORM 201 10 NM1 33 YORK INTERNATIONAL 28514A FILTER DRYER LIQUID STOP VALVE...
Страница 37: ...FORM 201 10 NM1 37 YORK INTERNATIONAL LD01285 FIG 3 SCREW CHILLER REFIGERANT FLOW DIAGRAM...
Страница 54: ...54 YORK INTERNATIONAL FIG 9 SYSTEM WIRING YCAS 140 246 CONNECTION DIAGRAM SYSTEM WIRING LD01466 D...
Страница 59: ...FORM 201 10 NM1 59 YORK INTERNATIONAL FIG 11 CONTINUED LD01465 D...
Страница 60: ...60 YORK INTERNATIONAL FIG 12 CONNECTION DIAGRAM WYE DELTA YCAS 140 246 CONNECTION DIAGRAM WYE DELTA LD01458 D...
Страница 61: ...FORM 201 10 NM1 61 YORK INTERNATIONAL FIG 12 CONTINUED LD01458 D...
Страница 69: ...FORM 201 10 NM1 69 YORK INTERNATIONAL FIG 16 CONTINUED LD01206 D...
Страница 71: ...FORM 201 10 NM1 71 YORK INTERNATIONAL FIG 17 CONTINUED LD01202 D...