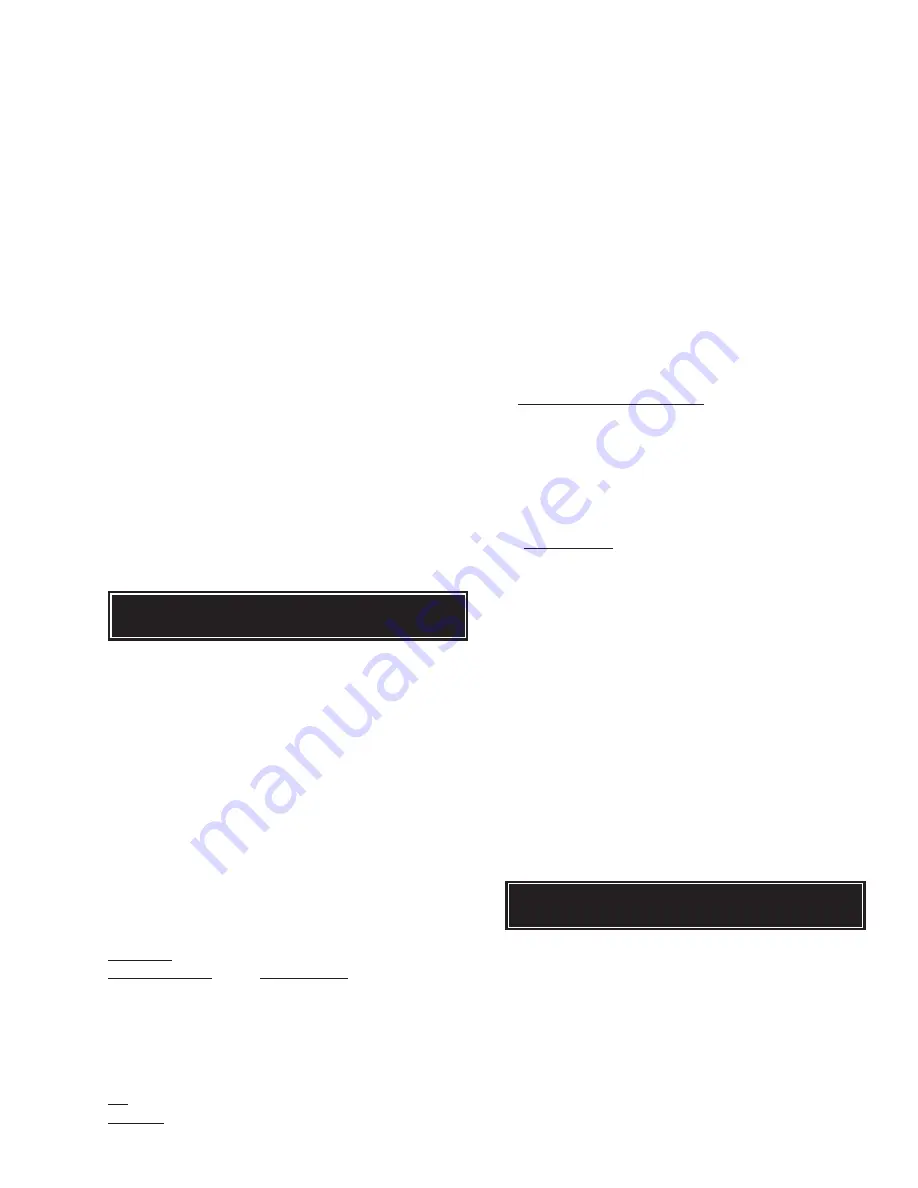
FORM 201.10-NM1
107
YORK INTERNATIONAL
sure differential between oil and suction pressure. Lack
of a differential indicates that the compressor is not
pumping and no oil is being pumped through the com-
pressor to lubricate the bearings and rotors.
This type of oil failure will not be picked up by the High
Oil Differential Safety since no flow will cause the differ-
ential through the oil piping to be zero, which would actu-
ally satisfy the High Oil Differential Safety.
The low oil pressure safety is activated after 60 seconds
of compressor operation. After 1 min., the oil pressure
must be greater than 10 PSID. After 2 min., greater than
20 PSID, after 3 min., greater than30 PSID, and after 4
min., 40 PSID. After 5 min. of operation and longer, oil
pressure must remain higher than 50 PSID or the sys-
tem will be shut down.
There is presently no display which allows the operator
to view the oil pressure differential.
The micro computes “differential oil pressure”, for this
safety by measuring oil pressure as sensed by the oil
transducer and subtracting suction pressure as sensed
by the suction transducer (Oil - Suction = Oil PSID).
An example of a low oil pressure fault display is shown
below:
Suction Pressure Safety
The Suction Pressure Safety assures that the system is
not allowed to operate under low refrigerant conditions or
due to a problem which will not allow proper refrigerant
flow.
When a compressor starts, the micro ignores suction
pressure until a pumpdown is completed (pumpdown to
cut-out or 30 sec., whichever comes first.). After
pumpdown, the micro begins monitoring the suction pres-
sure and continues to do so as long as the compressor
runs. For operation periods in the first 270 seconds, it is
permissible for the suction pressure to be less than the
programmed cut-out, but must be greater than:
Run Time + 10
3
x
SPCO
=
Cut-out
100
Programmed
Example: Run time = 60 seconds
Programmed Cut-out = 44 PSIG
60 + 10
3
x
44
=
13.2 PSIG
100
A close examination of the formula indicates the suction
pressure cut-out increases with time for the first 270 sec-
onds after the safety becomes active.
After 270 seconds, the suction pressure must be greater
than the cut-out.
A transient timer is built into the software to assure that
short term fluctuations in suction pressure due to fan
cycling, loading, etc. do not cause nuisance trips on low
suction pressure.
After 270 seconds of operation, the transient timer is
activated. If suction pressure drops below the cut-out
point, the 90 second transient timer begins timing and
the suction pressure must be greater than:
10 + (90 - transient time left)
x
SPCO
100
Example: Transient timer has been in effect for
30 sec. (60 sec. left)
Programmed cut-out = 44 PSIG
10 + (90 - 60)
x
44
=
17.6 PSIG
100
The longer the transient timer times, the higher the suc-
tion pressure must be. As long as the suction pressure
stays above the cut-out point as dictated by the formula,
the system will stay on line. 90 seconds after the tran-
sient timer starts, suction pressure must exceed the pro-
grammed cut-out. After the pressure exceeds SPCO + 5
PSIG, the transient timer will reset. Should the pressure
not reach SPCO + 5 PSIG which resets the transient
timer, but still remain above the cut-out, the compressor
will continue to run until suction pressure drops below
the cutout. At this time it will immediately shut down on a
low pressure fault.
The Suction Pressure Safety Cut-out is programmable
by the user (Page 91). An example of a suction pressure
fault message is shown below:
High Motor Current Safety
The High Motor Current Safety shuts a system down
and locks it out after only a single occurrence of a rise in
average motor current above the cut-out point. The safety
attempts to provide motor protection should an overload
occur due to a system or external problem. The micro
monitors motor current with 3 C.T.’s per motor, one on
each phase T1, T2 and T3 in both WYE-Delta or Across-
the-Line starters.
S Y S
1
L O W
O I L
D I F F
S Y S
2
L O W
O I L
D I F F
S Y S
1
L O W
S U C T I O N
S Y S
2
L O W
S U C T I O N
Содержание Millennium YCAS 316
Страница 11: ...FORM 201 10 NM1 11 YORK INTERNATIONAL YCAS 140 246 DIMENSIONS English LD01444 LD01446...
Страница 13: ...FORM 201 10 NM1 13 YORK INTERNATIONAL YCAS 140 246 DIMENSIONS SI LD01440 LD01442...
Страница 15: ...FORM 201 10 NM1 15 YORK INTERNATIONAL YCAS 216X 266X DIMENSIONS English LD01454 LD01454...
Страница 17: ...FORM 201 10 NM1 17 YORK INTERNATIONAL YCAS 216X 266X DIMENSIONS SI LD01450 LD01448...
Страница 33: ...FORM 201 10 NM1 33 YORK INTERNATIONAL 28514A FILTER DRYER LIQUID STOP VALVE...
Страница 37: ...FORM 201 10 NM1 37 YORK INTERNATIONAL LD01285 FIG 3 SCREW CHILLER REFIGERANT FLOW DIAGRAM...
Страница 54: ...54 YORK INTERNATIONAL FIG 9 SYSTEM WIRING YCAS 140 246 CONNECTION DIAGRAM SYSTEM WIRING LD01466 D...
Страница 59: ...FORM 201 10 NM1 59 YORK INTERNATIONAL FIG 11 CONTINUED LD01465 D...
Страница 60: ...60 YORK INTERNATIONAL FIG 12 CONNECTION DIAGRAM WYE DELTA YCAS 140 246 CONNECTION DIAGRAM WYE DELTA LD01458 D...
Страница 61: ...FORM 201 10 NM1 61 YORK INTERNATIONAL FIG 12 CONTINUED LD01458 D...
Страница 69: ...FORM 201 10 NM1 69 YORK INTERNATIONAL FIG 16 CONTINUED LD01206 D...
Страница 71: ...FORM 201 10 NM1 71 YORK INTERNATIONAL FIG 17 CONTINUED LD01202 D...