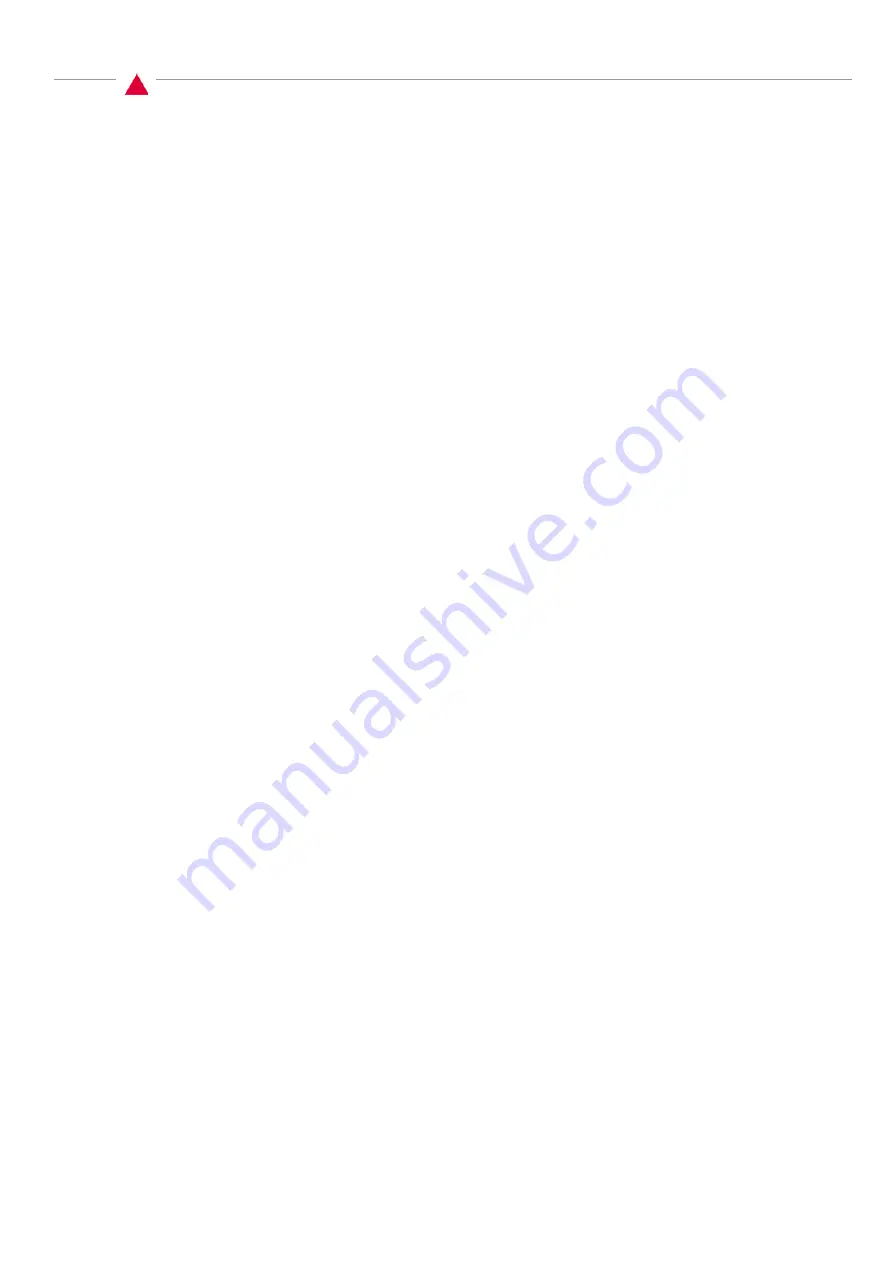
3
Ek-2/TL-KLT-01-01 / Rev 0
PRINCIPLES OF THE YENEN LPG PUMP
The Yenen LPG Pump is a special type of pump known as a turbine or regenerative pump. The liquid flows into
the inlet nozzle and into the passageway on each side of an impeller (the rotating element) and is recirculated
constantly between the vanes or teeth of the impeller and this passageway as the impeller rotates. The fluid
makes a complete revolution in the pump case and is diverted out the outlet nozzle. The horsepower required to
drive the pump increases as the differential pressure increases, but the capacity decreases at the same time.
Differential pressure is the difference between the pressure at the inlet of the pump and at the outlet of the
pump.
The impeller is the only moving part and has no contact with the casing. Consequently, practically no wear
occurs to the impeller, even when pumping volatile liquids such as LPG or ammonia which have little lubricating
qualities.
The pumping of volatile liquids is one of the most difficult of all pumping applications. Unlike other pumping
applications, more attention must be given to the design, manufacture, installation and operation of the pump.
Ductile iron has been used in the manufacture of this pump for parts under pressure.
The impeller floats on a shaft and may be replaced easily without disturbing the piping or driver by simply
removing the cover. No special tools are needed.
The mechanical seal assembly may be replaced easily by removing the cover and impeller without disturbing
the piping or driver. No special tools are needed.
Pressure gauge connections, ¼” NPT, are provided on the inlet and outlet nozzles.
INSTALLATION OF YENEN LPG PUMP
However, in order for the pump to deliver optimum performance, the principles discussed in this book should be
followed. The piping details are furnished to illustrate methods proved by hundreds of installations. Your own
needs may require slight variations, but every effort should be made to follow the recommendations identified in
this manual.
No pump can discharge more liquid than it receives, so the location and the inlet piping must be given careful
attention. If the inlet piping is inadequate to supply the demand of the pump, you may expect trouble! The inlet
line size should be the same size as the pump suction or next size larger. Pressure loss between the storage
tank and the pump should be minimized.
The pump should be located as close to the storage tank as possible. The complete inlet line, including the
vertical line from the tank, should not exceed 3.6 m in length. The bottom of the tank should be at least 0.6 m
above the pump inlet nozzle, and 1.2 m should be considered standard.
The inlet should include the following:
1. The tank excess flow valve should have a flow rate of 1-1/2 to 2 times the capacity of the pump.
2. Pressure gauge at pump suction nozzle.
3. The tank shutoff valve should be a full port ball valve or an internal valve.
5. A flexible connection should be used on the pump inlet or outlet to accommodate piping strains.
6. An eccentric swage should be used at the pump inlet nozzle to change line size (flat side up).
7. The inlet line must be level or slope downward to the pump.
The outlet piping should include the following:
1. A pressure gauge should be installed in the opening provided on the outlet nozzle or in the outlet piping near
the pump. This pressure gauge will tell you the complete story of the operation inside your pump. Be sure you
have one installed.
2. A hydrostatic relief valve is required to be installed in the outlet piping.
3. If the outlet piping exceeds 50 feet (15.2 m) in length, a check valve should be installed near the pump
outlet.