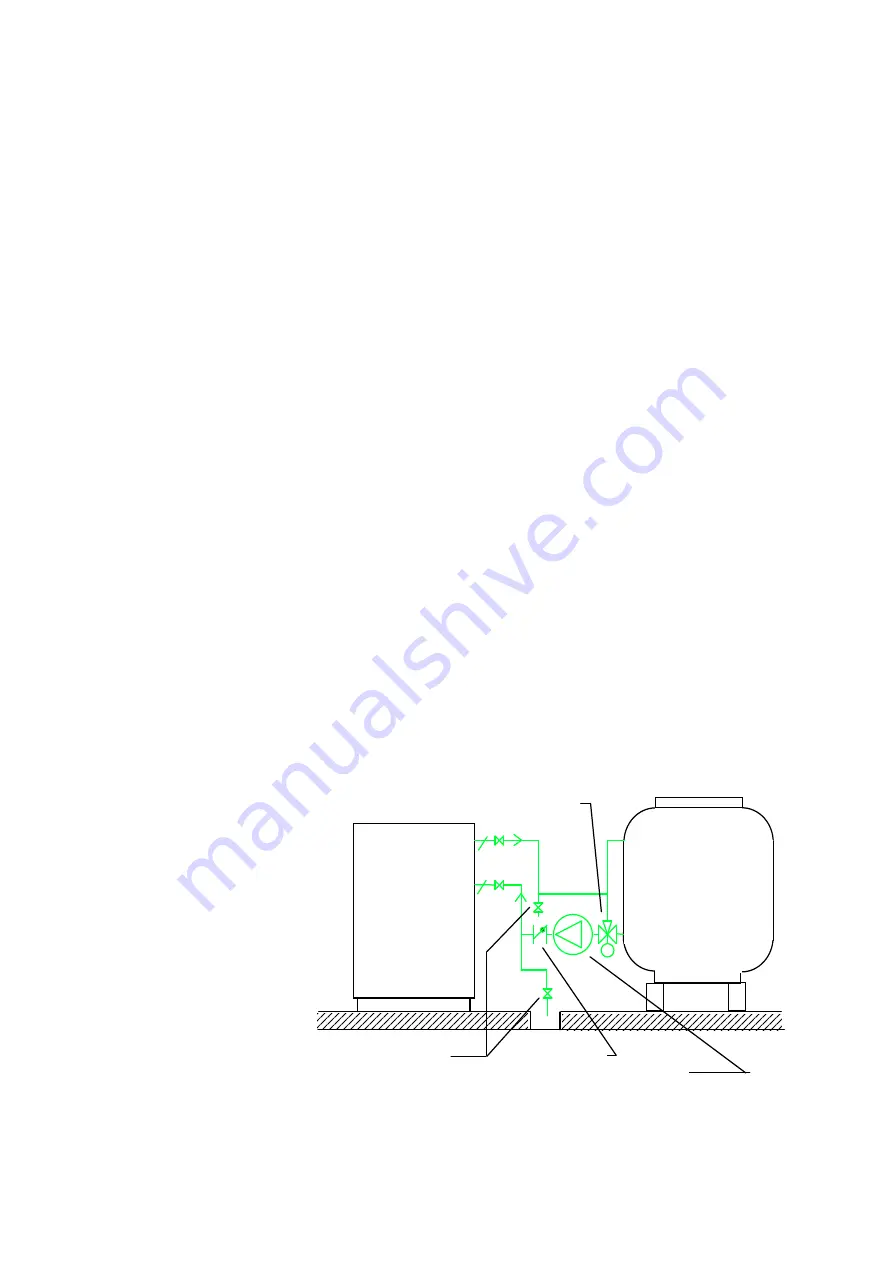
WFC- SC(H) Series
.
Installation
- 10 -
A balance valve should be installed in the chilled-hot water outlet and a stop valve
should be installed in the chilled-hot water inlet. Both valves along with thermometer
wells should be placed in close proximity to the chiller-heater, refer figure 12.
After thoroughly testing for leaks, insulate the piping circuit ensuring an adequate
vapor barrier is obtained. Be sure the insulation allows proper access to all
thermometer wells and hand valves. Be also sure that the chiller-heater panels are not
restricted by the insulation.
If the equipment is installed outdoors and subject to freezing ambient conditions, trace
heating of the pipes under the insulation may be considered. If glycol solutions are
contemplated, it is important that inhibitors are in solution to protect copper tubes
internal to the machine. It is further most important to understand that cooling
capacity of the chiller-heater will be degraded as concentrations of the glycol
solutions increase – it must be noted that there is limited flow rate increase allowance
for the chilled- hot water circuit.
4.3
Cooling Water Piping
Cooling water to the absorption chiller-heater is required at a temperature of 31°C or
less during cooling operation. It is also imperative that cooling water less than 24°C
should not be supplied to the chiller-heater for prolonged periods.(longer than 30
minutes). If such contingency is likely to occur, a mixing valve facility must be
installed as illustrated in figure 13.
It is also of particular importance to observe that the cooling flows in a parallel
fashion through the WFC-SHC20 & SCH30 machines – dissimilar to the WFC-
SCH10 which flows in parallel. Attention must be paid to the instruction label on the
machine with respect to the sizing of the transfer pipe on the cooling water inlet.
Wherever possible, install the cooling tower at the same level or higher than the
chiller-heater. If it is not possible, give careful consideration to the prevention of
drain-back and loss of
cooling water due to
overflow at the tower.
Such matters should
have been given prior
consideration by the
design engineer along
with proper facility to
prevent damage to the
cooling
tower
fill
media as a result of
daily, frequent mode
change-over of the
chiller-heater.
F
Figure 13
Chiller-
Heater
Cooling
Tower
Mixing valve
Check valve
Cooling water
pump
Drain valves