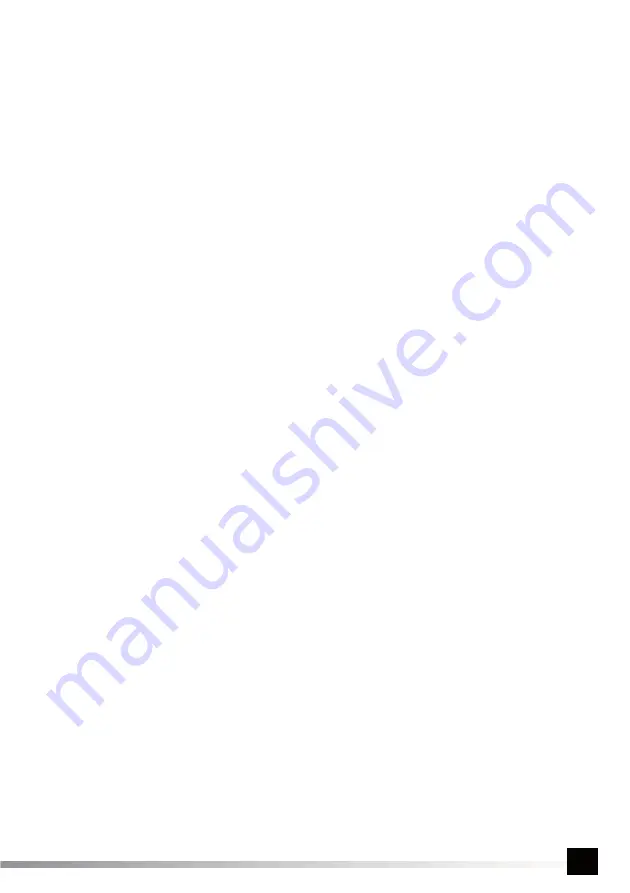
17
GB
O R I G I N A L I N S T R U C T I O N S
Proceed to work with the proper surface of the grinding wheel to workpiece:
- in the case of grinding wheels for grinding you should grind by the side and/or leading surface,
- in the case of flap grinding wheels you should grind by the surface side so that the sandpaper leaves would move parallel to
the workpiece,
- in the case of discs with Velcro for attachment for mouning the abrasive paper, grinding must be carried out by side surface,
- in the case of wire brushes the treatment should be done by wires endings, not by their side surface,
- in the case of grinding wheels for cutting, you should cut by their front surface, do not grind by the front surface of grinding
wheels, which are designed for cutting.
When grinding by the side surface, you should keep the grinder for angle not more than 30 degrees relative to the treated surface
(VIII). Move the grinder forward and back by smooth moves.
During cutting, the grinding wheel should be at a right angle relative to the cut surface. Do not make the cut at a different angle.
It is forbidden to change the angle of the cutting grinding wheels in relation to the workpiece during the cutting operation. The cut
should be made only in a straight line. Failure to follow these guidelines increases the risk of grinding wheel jam in workpiece,
which can cause rebound of tool toward the operator, rupture of the grinding wheel or its disintegration
Cutting must be carried out in a direction of rotation of the grinding wheel (IX).
During grinder operation, do not exert too much pressure on the treated surface, and do not make sudden movements, to not
cause jamming, or cracks and bursts of grinding wheel.
Do not allow to overload the grinder, its external surface temperature should never exceed 60
O
C.
At the end of work you should turn off the grinder, disconnect it from the pneumatic system and inspect the grinder.
Attention! The grinding wheel rotates even for some time after the machine is switched off. Prior to the inspection you should
wait for cooling of the grinding wheel. During the work, both, grinding wheel and workpiece material, can warm up to a high
temperature.
Remember! When operating the angle grinder:
Always use eye protection.
Do not use grinding wheels of a maximum allowable peripheral speed of less than 80 m/s.
Do not use grinding wheels of a maximum authorized rotational speed less than the rotational speed of the grinder.
MAINTENANCE
Never use gasoline, solvent, or any other flammable liquid to clean the tool. The vapors can be ignited, causing the tool explosion
and serious injury. Solvents, which are used to clean the tool holder and the body, can cause seals softening. Thoroughly the tool
before starting your work.
In case of finding any irregularities in the tool operation, the tool you should be immediately disconnect from the pneumatic
system.
All the elements of the pneumatic system must be protected against contamination. Contamination, that enters the pneumatic
system can damage the tool and other air system components.
Maintenance the tool before each use
Disconnect the tool from the pneumatic system.
Before each use, let a small amount of liquid preservative (e.g.. WD-40) through the air intake.
Connect the tool to pneumatic system and run for about 30 seconds. This will distribute the liquid preservative inside the tool
interior and will clean it.
Again, disconnect the tool from the pneumatic system.
Let small amount of oil SAE 10 to the inside of the tool, through the air inlet and the holes intended for this purpose. It is recom-
mended to use oil SAE 10 intended for maintenance of pneumatic tools. Connect the tool and run it for a short time.
Attention! WD-40 may not be used as an appropriate lubricating oil.
Remove excess of oil, that spill out through the holes. Left oil may damage the tool seals.
Other maintenance operations
Before each use, you should check whether the tool shows any traces of damages. Drivers, tool holders and the spindles must
be kept clean.
Every 6 months or after 100 hours of operation, you must pass the tool for inspection by the qualified personnel in the repair
shop. If the tool was used without the application of recommended air supply system, you should increase the frequency of the
tool inspections.
Troubleshooting
You should stop using the tool immediately after the disguardy of any fault. Work with a defective tool can cause injury. Any repair
or replacement of tool components must be carried out by qualified personnel in authorized repair facility.