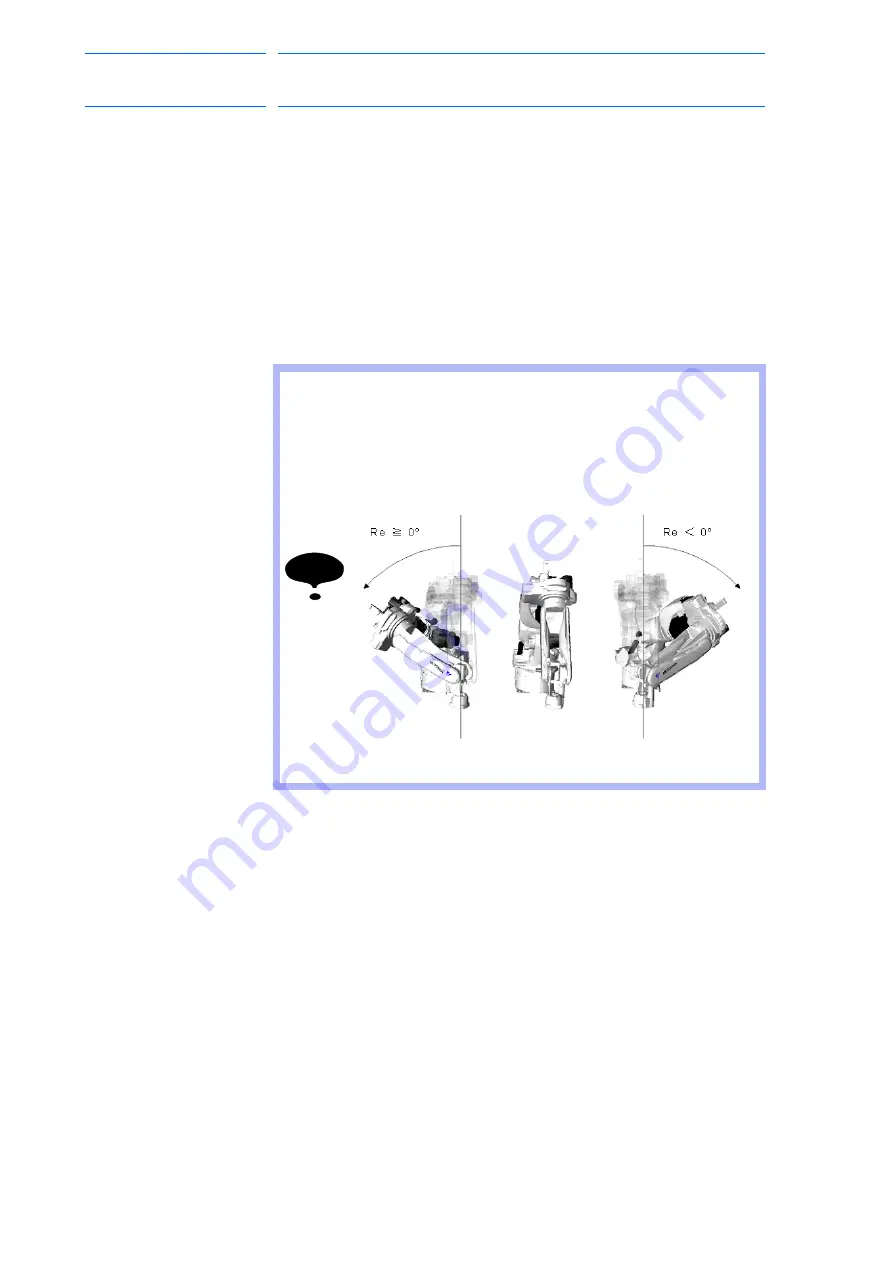
3 Teaching
3.9 Other Job-editing Functions
3-89
155507-1CD
RE-CSO-A037
DX100
3.9.4.10 Manipulator
Types
When the position data of the job data are described using the XYZ
format, several postures may be taken according to the manipulator’s
structure when moving it to the described position.
Although these postures have the same coordinates for TCP, they vary in
pulse for each axis.
Thus, the manipulator’s posture cannot be uniquely defined only by the
coordinate value, and it is necessary to specify the data other than the
coordinate value to define the manipulator’s posture.
This is called “Type”.
Type varies according to the manipulator model.
NOTE
For the manipulator with seven axes, X, Y, Z, Rx, Ry, Rz, Re
and Type are used.
Re is an element to indicate the posture of the manipulator
with seven axes and does not change by the specified
coordinates.
The definition of Re is shown below.
172 of 554