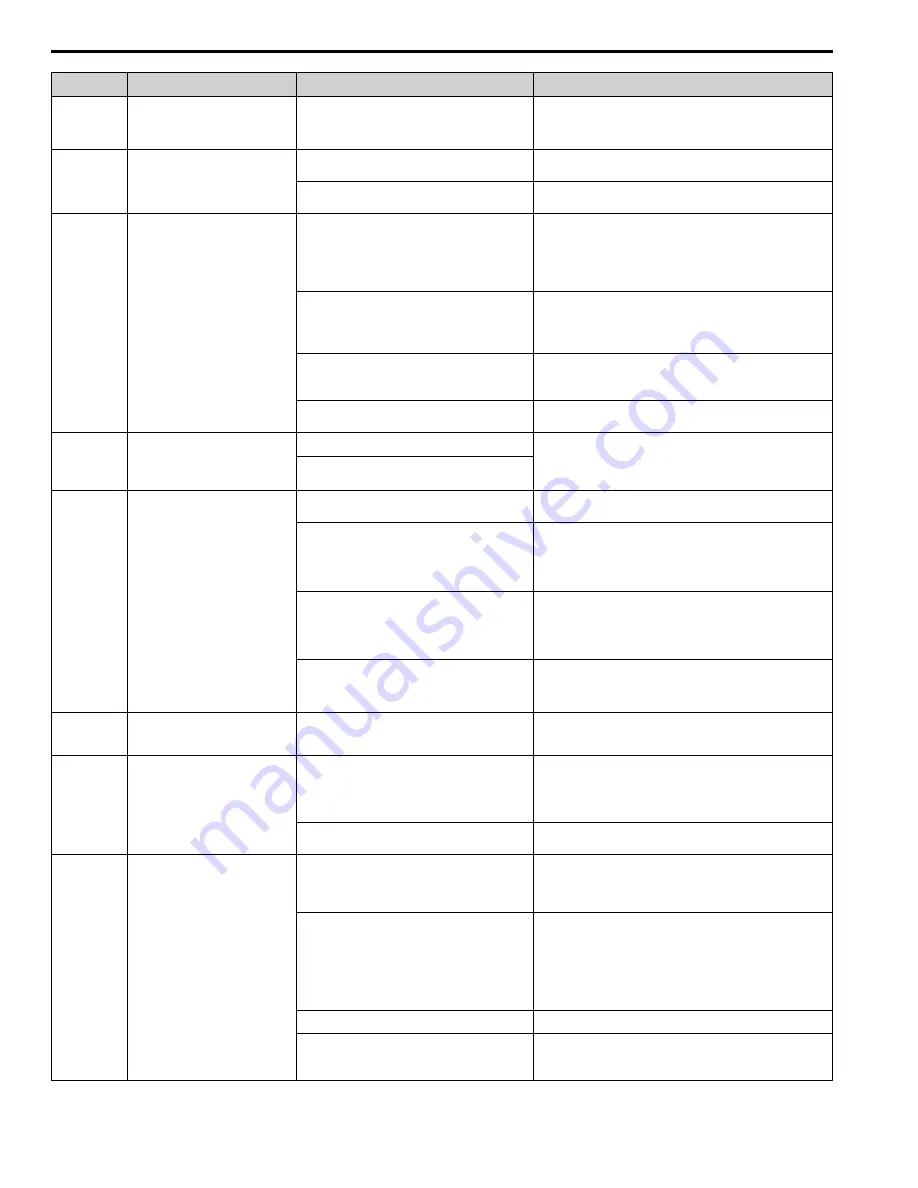
148
YASKAWA
TOEPC71061737D GA800 DRIVE INSTALLATION & PRIMARY OPERATION
Code
Name
Causes
Possible Solutions
PSE
JOHB-SMP3 Protocol Set Error
•
The DIP switches on the JOHB-SMP3 are at their
default setting.
•
There is no protocol assigned to the JOHB-SMP3.
Make sure that the power to the drive is OFF and the CHARGE
LED light is OFF before you use the DIP switches on the JOHB-
SMP3 to set the protocol. Refer to the JOHB-SMP3 manual for
more information.
rF
Braking Resistor Fault
The resistance of the dynamic braking option that is
connected to the drive is too low.
Use a dynamic braking option that fits the model and duty rating of
the drive.
A regenerative converter, regenerative unit, or
braking unit is connected to the drive.
Set
L8-55 = 0 [Internal DB TransistorProtection = Disable]
.
rH
Braking Resistor Overheat
The deceleration time is too short and excessive
regenerative energy is flowing back into the drive.
•
Check the load level, deceleration time, and speed.
•
Decrease the load.
•
Increase the values set in
C1-02, C1-04, C1-06, or C1-08
[Deceleration Times]
.
•
Use a dynamic braking option that lets you use more power.
The duty cycle is too high.
Examine the duty cycle.
Note:
When
L8-01 = 1 [3% ERF DB Resistor Protection = Enabled]
,
the maximum braking duty cycle is 3%.
The braking load is too heavy.
•
Calculate the braking load and braking power again, and
decrease the braking load.
•
Use a braking resistor that improves braking power.
The braking resistor is not sufficient.
Use the braking resistor specifications to select a sufficient braking
resistor.
rr
Dynamic Braking Transistor Fault
The drive control circuit is damaged.
There is a malfunction in the internal braking
transistor of the drive.
•
Re-energize the drive.
•
If the fault stays, replace the control board or the drive. For
information about replacing the control board, contact Yaskawa
or your nearest sales representative.
SC
Short Circuit/IGBT Failure
Overheating caused damage to the motor or the motor
insulation is not satisfactory.
Measure the motor insulation resistance, and replace the motor if
there is electrical conduction or unserviceable insulation.
The motor main circuit cable is contacting ground to
make a short circuit.
•
Examine the motor main circuit cable for damage, and repair
short circuits.
•
Measure the resistance between the motor main circuit cable and
the ground terminal. If there is electrical conduction, replace the
cable.
A short circuit or ground fault on the drive output
side caused damage to the output transistor of the
drive.
•
Make sure that there is not a short circuit in terminal B1 and
terminals U/T1, V/T2, and W/T3. Make sure that there is not a
short circuit in terminals - and terminals U/T1, V/T2, and W/T3.
•
If there is a short circuit, contact Yaskawa or your nearest sales
representative.
When
A1-02 = 5, 6, 7 [Control Method Selection =
OLV/PM, AOLV/PM, or CLV/PM]
, the output current
is more than the value set in
L8-27 [Overcurrent
Detection Gain]
.
Set
L8-27
correctly.
SCF
Safety Circuit Fault
The safety circuit is broken.
Replace the control board or the drive. For information about
replacing the control board, contact Yaskawa or your nearest sales
representative.
SEr
Speed Search Retries Exceeded
The speed search-related parameters are set
incorrectly.
•
Decrease
b3-10 [Speed Estimation Detection Gain]
.
•
Increase
b3-17 [Speed Est Retry Current Level]
.
•
Increase
b3-18 [Speed Est Retry Detection Time]
.
•
Do Auto-Tuning again.
The motor is coasting in the opposite direction of the
Run command.
Set
b3-14 = 1 [Bi-directional Speed Search = Enabled]
.
STPo
Motor Step-Out Detected
The motor code is set incorrectly for PM Control
Methods.
•
Set
E5-01 [PM Motor Code Selection]
correctly as specified by
the motor.
•
For specialized motors, refer to the motor test report and set
E5-
xx
correctly.
The load is too large.
•
Increase the value set in
n8-55 [Motor to Load Inertia Ratio]
.
•
Increase the value set in
n8-51 [Pull-in Current @ Acceleration]
.
If the drive detects
STPo
during deceleration when increasing the
value set in
n8-51
, set the value of
n8-79 [Pull-in Current @
Deceleration]
lower than
n8-51
.
•
Decrease the load.
•
Replace the drive and motor with larger capacity models.
The load inertia is too large.
Increase the value set in
n8-55
.
The acceleration/deceleration times are too short.
•
Increase the values set in
C1-01 to C1-08 [Acceleration/
Deceleration Times]
.
•
Increase the value set in
C2-01 [S-Curve Time @ Start of Accel]
.