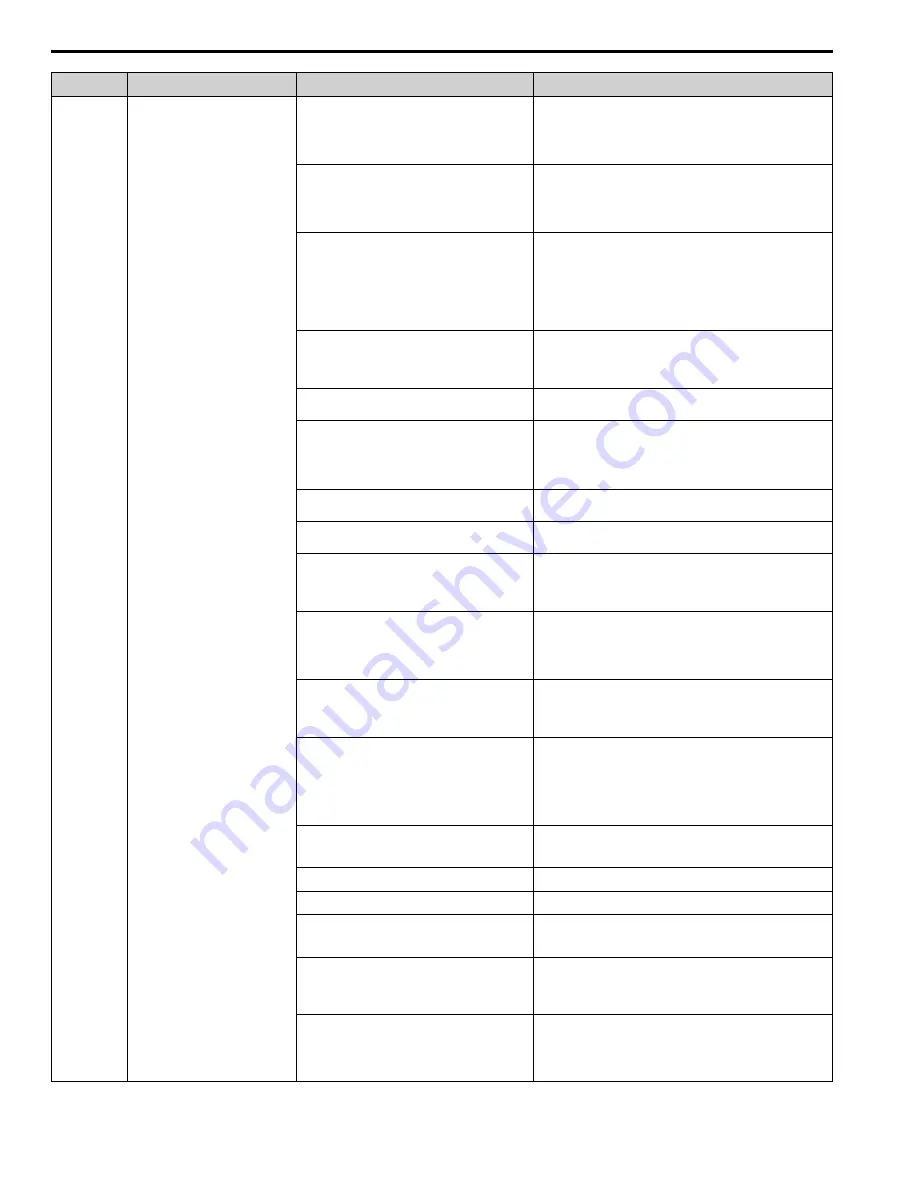
142
YASKAWA
TOEPC71061737D GA800 DRIVE INSTALLATION & PRIMARY OPERATION
Code
Name
Causes
Possible Solutions
The motor main circuit cable is contacting ground to
make a short circuit.
•
Examine the motor main circuit cable for damage, and repair
short circuits.
•
Measure the resistance between the motor main circuit cable and
the ground terminal. If there is electrical conduction, replace the
cable.
A short circuit or ground fault on the drive output
side caused damage to the output transistor of the
drive.
•
Make sure that there is not a short circuit in terminal B1 and
terminals U/T1, V/T2, and W/T3. Make sure that there is not a
short circuit in terminals - and terminals U/T1, V/T2, and W/T3.
•
If there is a short circuit, contact Yaskawa or your nearest sales
representative.
The acceleration time is too short.
•
Calculate the torque necessary during acceleration related to the
load inertia and the specified acceleration time.
•
Increase the values set in
C1-01, C1-03, C1-05, or C1-07
[Acceleration Times]
to get the necessary torque.
•
Increase the values set in
C2-01 to C2-04 [S-Curve
Characteristics]
to get the necessary torque.
•
Replace the drive with a larger capacity model.
The drive is trying to operate a specialized motor or a
motor that is larger than the maximum applicable
motor output of the drive.
•
Examine the motor nameplate, the motor, and the drive to make
sure that the drive rated current is larger than the motor rated
current.
•
Replace the drive with a larger capacity model.
A magnetic contactor was switched at the output.
Set the operation sequence to not turn ON or OFF the magnetic
contactor while the drive is outputting voltage.
The V/f pattern settings are incorrect.
•
Examine the ratios between the V/f pattern frequency and
voltage. Decrease the voltage if it is too high compared to the
frequency.
•
Adjust
E1-04 to E1-10 [V/f Pattern Parameters]
. For motor 2,
adjust
E3-04 to E3-10
.
The torque compensation gain is too large.
Decrease the value set in
C4-01 [Torque Compensation Gain]
to
make sure that the motor does not stall.
Electrical interference caused a problem.
Examine the control circuit lines, main circuit lines, and ground
wiring, and decrease the effects of electrical interference.
The gain during overexcitation operation is too large.
•
Find the time when the fault occurs.
•
If the fault occurs at the same time as overexcitation operation,
decrease the value set in
n3-13 [OverexcitationBraking (OEB)
Gain]
and consider the motor flux saturation.
The drive received a Run command while the motor
was coasting.
•
Examine the sequence and input the Run command after the
motor fully stops.
•
Set
b3-01 = 1 [Speed Search at Start Selection = Enabled]
or set
H1-xx = 61, 62 [Speed Search from Fmax or Fref]
to input speed
search commands from the MFDI terminals.
In PM Control Methods, the setting of the motor code
is incorrect.
•
Enter the correct motor code to
E5-01 [PM Motor Code
Selection]
as specified by the PM motor.
•
For specialized motors, refer to the motor test report and set
E5-
xx [PM Motor Settings]
correctly.
If the drive detects the fault at start or in the low
speed range (10% or less) and
n8-57 = 1 [HFI
Overlap Selection = Enabled]
for PM Control
methods, the high frequency injection gain is too
high.
•
Set
E5-xx [PM Motor Parameters]
correctly or do Rotational
Auto-Tuning.
•
Decrease the value of
n8-41 [HFI P Gain]
in 0.5-unit
increments.
Note:
Set
n8-41 > 0.0
for IPM motors.
The current flowing in the motor is more than the
value set in
L8-27 [Overcurrent Detection Gain]
for
PM Control Methods.
Correct the value set in
L8-27
.
The control method is set incorrectly for the motor.
Set
A1-02 [Control Method Selection]
correctly.
The motor main circuit cable is too long.
Replace the drive with a larger capacity model.
Speed search does not complete at start when you set
A1-02 = 8 [EZ Vector Control]
and use an induction
motor.
When
E9-01 = 0 [Motor Type Selection = Induction (IM)]
, set
b3-
24 = 2 [Speed Search Method Selection = Current Detection Speed
Search]
.
An overcurrent occurred during overexcitation
deceleration.
•
Decrease the value set in
n3-13 [OverexcitationBraking (OEB)
Gain]
.
•
Decrease the value set in
n3-21 [HSB Current Suppression
Level]
.
When you use an IE3 premium efficiency motor.
Use these values to adjust the parameters.
•
b3-03 [Speed Search Deceleration Time]
= default value × 2
•
L2-03 [Minimum Baseblock Time]
= default value × 2
•
L2-04 [Powerloss V/f Recovery Ramp Time]
= default value × 2