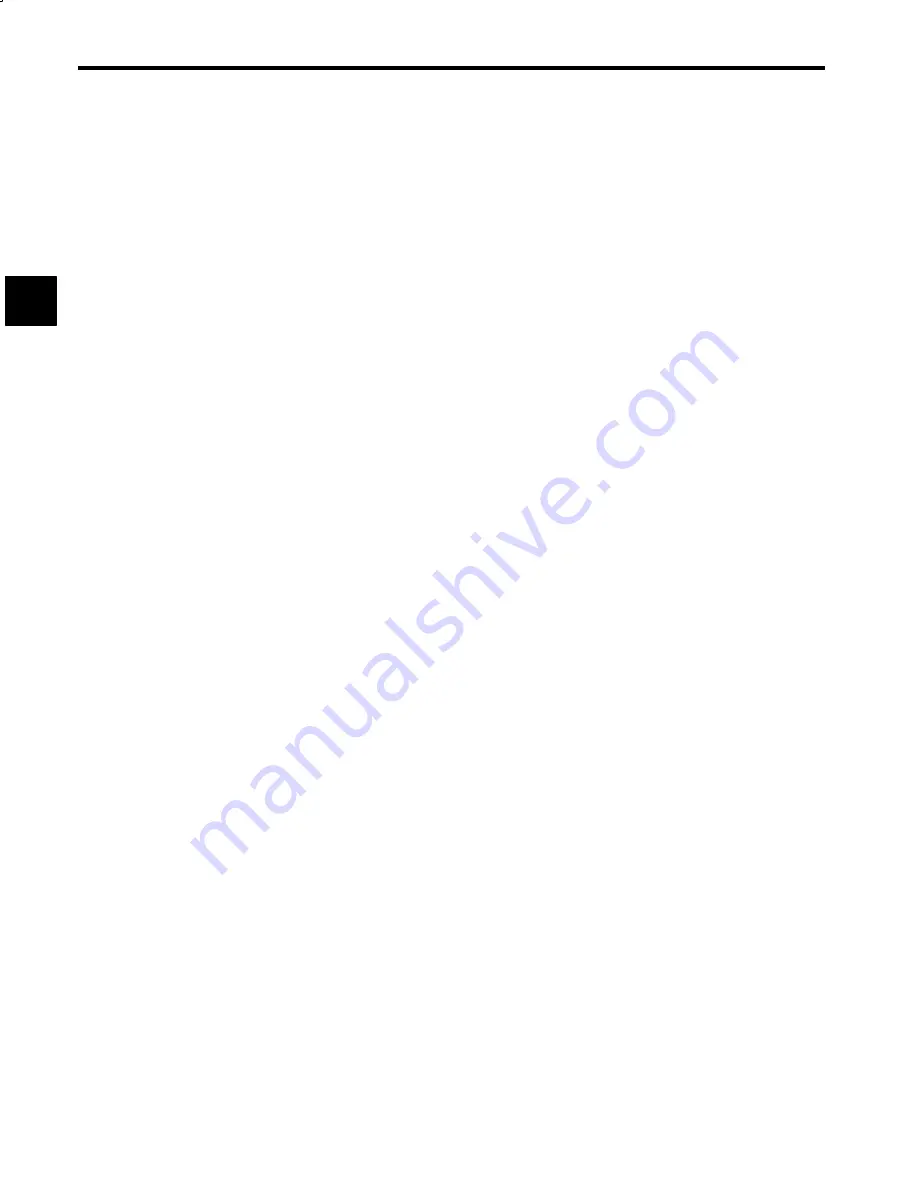
Introduction
1.1.1 Features
1
-2
1.1 Overview
The VS-625M5 Inverter and VS-656MR5 Converter form a highly reliable, high-performance AC drive system
in which an AC spindle motor is controlled by the Inverter using vector control with a regenerative function.
The system ensures stable drive control of machine tools, such as machining centers and lathes, and industrial
machines, such as transfer machines and testing machines, while providing high speed and the ability to handle
tough environmental conditions.
1.1.1 Features
The system has the following features.
J
Multi-axis Driving
The Inverter and Converter are separate units of highly reliable, compact book-type construction. The
Converter incorporates a power regeneration function and multi-axis driving configuration, providing
power to the spindle drive and servo drive with easy control through the control panel.
J
Compact
The Inverter and Converter are more compact and ensure higher precision than conventional models. This
was enabled by the development of a compact, high-precision detector, improvement in output voltage
under optimal vector control, and the selection of an optimum cooling construction as a result of thermal
analysis.
J
Compatible with Yaskawa’s YENET1200 Standard Network
The Inverter and Converter are available in models that are compatible with Yaskawa’s YENET1200 stan-
dard high-speed serial network, making it possible to reduce the number of wires for CNC connections.
The Inverter and Converter are also available in models that are compatible with analog I/O interfaces as
well so that the Inverter and Converter can be used with the VS-626 Series for conventional spindle driv-
ing. Sequence I/O can be connected to 0- and 24-V common terminals.
J
Compact, Lightweight Spindle Motor
The downsizing of the spindle motor was enabled by the optimum electromagnetic design of the system
ensuring ideal heat distribution, improvements in the core and cooling construction of the system, and
changes in the circuit design of the encoder. The system ensures higher reliability under tough environ-
mental conditions than any conventional system.
J
High-precision, High Servo Performance
The system employs a high-speed IGBT (insulated gate bipolar transistor) power element for high
−
preci-
sion, high-frequency PWM control at high speeds, suppressing current distortion that may cause torque
ripples and reducing rotational fluctuations. The system employs a DSP (digital signal processor) as well
to improve the servo performance of the system.
J
Improved Orientation Function
The system performs orientation control to a fixed position using the motor encoder. This function is used
when the motor shaft is connected to the load shaft at a ratio of one to one. For orientation control with
a magnetic sensor, the detected signal of the motor encoder will be used for orientation control to desired
position.
J
Expanded Fixed Output Range via Winding Selection
If a winding selection motor is used, a dedicated electromagnetic contactor will select the winding, making
it possible to expand the fixed output range without an increase in the capacity of the Inverter. This will
eliminate the speed change mechanism of the machinery to enable downsizing.
J
Continuous Regenerative Operation
The Converter and Inverter employ an IGBT so that the Converter will respond to frequent accelerations
and decelerations, suppress temperature rises, and save energy consumption, improving the rate of power
supply regeneration and enabling regenerative control at high speeds.
J
Construction
Inverter and Converter models with external heatsink cooling are available and panel-mounting construc-
tion with an integral cooling fan are provided for ease of panel mounting and maintenance.
1