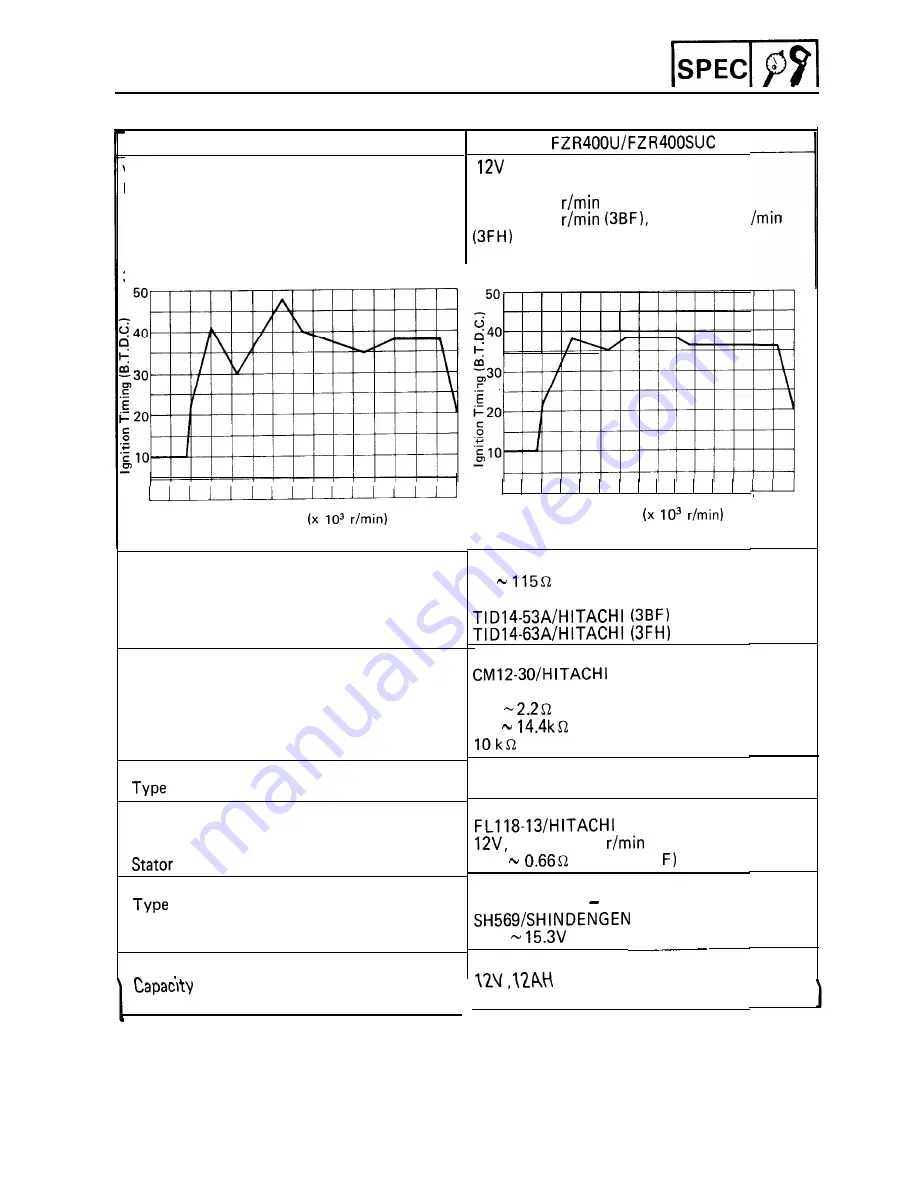
MAINTENANCE SPECIFICATIONS
Electrical
Model
Voltage:
Ignition System:
Ignition Timing (B.T.D.C.)
Advanced Timing (B.T.D.C.)
Advancer Type
3BF:
0
1
2
3
4
5
6
7 8 9 1 0 11 1 2 1 3 1 4 15
Engine Speed
T.C.I.:
Pickup Coil Resistance
(Color)
T.C.I. Unit/Manufacturer
Ignition Coil:
Model/Manufacturer
Minimum Spark Gap
Primary Winding Resistance
Secondary Winding Resistance
Spark Plug Cap Resistance
Charging System:
A.C. Generator:
Model/Manufacturer
Nominal Output
Coil Resistance
Voltage Regulator:
Model/Manufacturer
No Load Regulated Voltage
Battery:
Specific Gravity
IO” at 1,300
48” at 6,500
38” at 3,500 r
Electrical
3FH:
0
1 2 3
4
5 6
7 8 9 1 0 1 1 1 2 1
Engine Speed
85
at 20°C (68°F)
(White/Red -White/Black)
6 mm (0.24 in)
1.8
at 20°C (68°F)
9.6
at 20°C (68°F)
A.C. Magneto Generator
18A at 5,000
0.44
at 20°C (68”
Semi conductor short circuit
14.3
1.280
314 15
2-14
Содержание FZR400 1988-1989
Страница 1: ...Yamaha FZR400 Service Manual 1988 1989 Models ...
Страница 2: ......
Страница 79: ...LUBRICATION DIAGRAM ISPEC l LUBRICATION DIAGRAM Oil filter Oil strainer Oil pump ...
Страница 83: ...CABLE ROUTING CABLE ROUTING 3 2 24 ...
Страница 85: ...CABLE ROUTING bPECl j 39I CABLE ROUTING 4 2 26 ...
Страница 87: ...CABLE ROUTING ISPEC l CABLE ROUTING 5 2 28 ...
Страница 93: ...5 Remove Rear view mirrows Left and right 9 Remove 0 Upper cowling ...
Страница 250: ...FRONT AND REAR BRAKE piqzq ...
Страница 251: ...FRONT AND REAR BRAKE 8 Inspect Brake fl d level refer to the BRAKE FLUID INSPEC TICIN SeCtlo I the CHAPTER 3 ...
Страница 252: ...FRONT AND REAR BRAKE CHAS if31 Caliper Bleed screw 6 Nrn 0 6 m 4 3 18Nrn 1 8rn L 13ft b ...
Страница 296: ...CIRCUIT DIAGRAM wELEC ELECTRICAL FZR400WSUC CIRCUIT DIAGRAM q B I L 6 B Ch B B IL A 8 l ...
Страница 305: ...IGNITION SYSTEM ELECII IGNITION SYSTEM CIRCUIT DIAGRAM 8 11 ...
Страница 315: ...ELECTRIC STARTING SYSTEM ELECTRIC STARTING SYSTEM CIRCUIT DIAGRAM 8 21 ...
Страница 323: ...ELECTRIC STARTING SYSTEM a IDiode block is faulty Replace the diode block I 8 29 ...
Страница 324: ...ELECTRIC STARTING SYSTEM STARTER MOTOR Brush Armature Stator O ring 11 01 8 30 ...
Страница 327: ...CHARGING SYSTEM 1 CHARGING SYSTEM CIRCUIT DIAGRAM I R W1 tDm t 8 33 ...
Страница 332: ...ELECl m 1 LIGHTING SYSTEM LIGHTING SYSTEM CIRCUIT DIAGRAM I r 7 I 4 _r W B Ed L R 0 1 I I T L Br Ch Dg P t 8 39 ...
Страница 362: ...COOLING SYSTEM 1 ELECi ii 1 COOLING SYSTEM CIRCUIT DIAGRAM L Br LI R L D I G 8 69 ...
Страница 368: ...FUEL SYSTEM FUEL SYSTEM CIRCUIT DIAGRAM ...
Страница 395: ...J I II ...
Страница 396: ......
Страница 397: ...FOX Racing Shox Setup Manual MOTORCYCLE ...
Страница 408: ......
Страница 409: ......
Страница 410: ......
Страница 412: ...FZR400U A1 ...
Страница 476: ...FZR400U K1 ...
Страница 477: ...FZR400U K2 ...