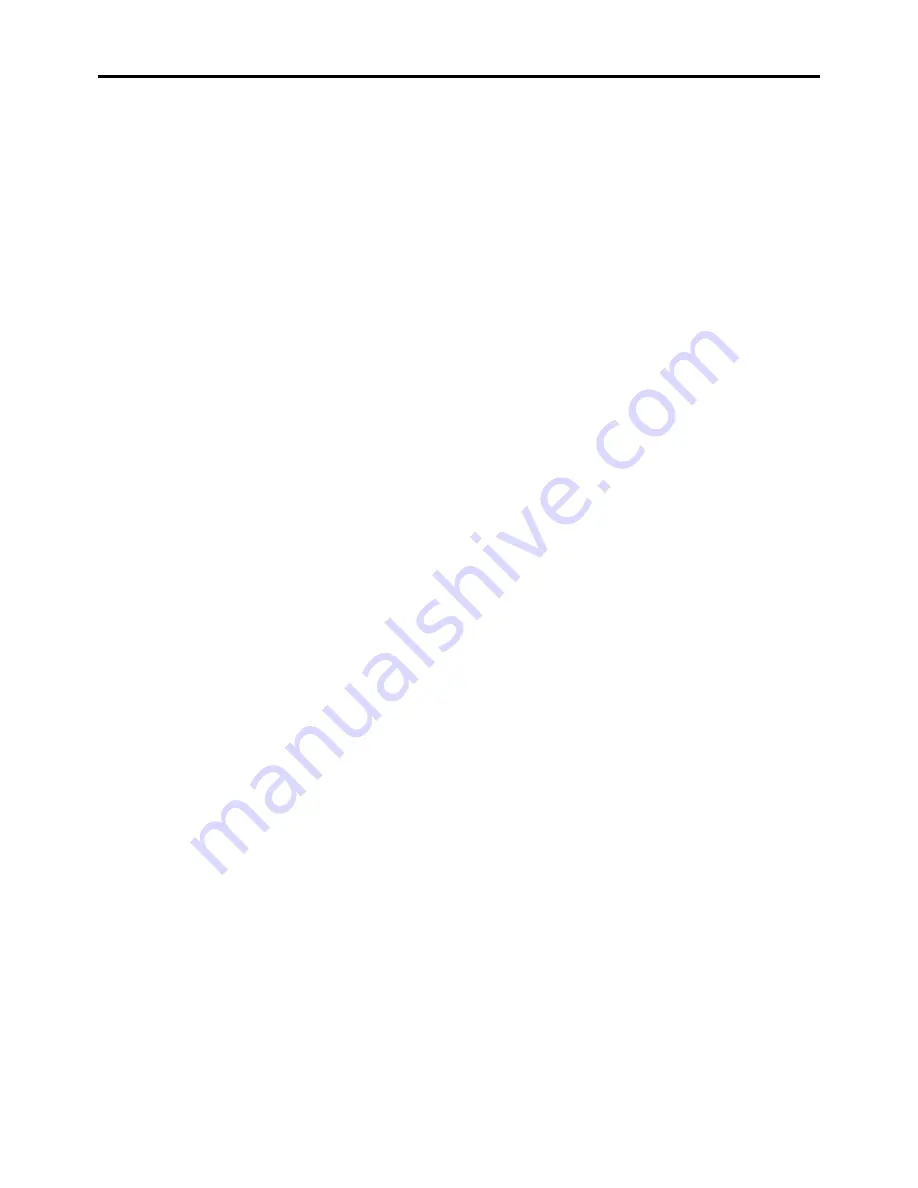
SWINGARM
................................................................................................4-79
REMOVING THE SWINGARM .............................................................4-81
CHECKING THE SWINGARM .............................................................4-82
INSTALLING THE SWINGARM ............................................................4-82
CHAIN DRIVE
.............................................................................................4-84
REMOVING THE DRIVE CHAIN ..........................................................4-85
CHECKING THE DRIVE CHAIN ..........................................................4-85
CHECKING THE DRIVE SPROCKET ..................................................4-86
CHECKING THE REAR WHEEL SPROCKET .....................................4-86
CHECKING THE REAR WHEEL DRIVE HUB .....................................4-86
INSTALLING THE DRIVE CHAIN .........................................................4-86
Содержание 2009 YZF-R1Y
Страница 1: ...SERVICE MANUAL YZFR1Y C 14B 28197 10 LIT 11616 22 78 2009 ...
Страница 6: ......
Страница 8: ......
Страница 36: ...SPECIAL TOOLS 1 27 ...
Страница 66: ...LUBRICATION SYSTEM CHART AND DIAGRAMS 2 29 EAS20410 LUBRICATION DIAGRAMS ...
Страница 68: ...LUBRICATION SYSTEM CHART AND DIAGRAMS 2 31 ...
Страница 70: ...LUBRICATION SYSTEM CHART AND DIAGRAMS 2 33 ...
Страница 72: ...LUBRICATION SYSTEM CHART AND DIAGRAMS 2 35 ...
Страница 73: ...LUBRICATION SYSTEM CHART AND DIAGRAMS 2 36 1 Main axle 2 Oil water pump assembly ...
Страница 74: ...LUBRICATION SYSTEM CHART AND DIAGRAMS 2 37 ...
Страница 75: ...LUBRICATION SYSTEM CHART AND DIAGRAMS 2 38 1 Main axle 2 Oil delivery pipe 2 3 Drive axle ...
Страница 76: ...LUBRICATION SYSTEM CHART AND DIAGRAMS 2 39 ...
Страница 78: ...LUBRICATION SYSTEM CHART AND DIAGRAMS 2 41 ...
Страница 80: ...LUBRICATION SYSTEM CHART AND DIAGRAMS 2 43 ...
Страница 81: ...LUBRICATION SYSTEM CHART AND DIAGRAMS 2 44 1 Balancer shaft 2 Crankshaft ...
Страница 82: ...COOLING SYSTEM DIAGRAMS 2 45 EAS20420 COOLING SYSTEM DIAGRAMS ...
Страница 83: ...COOLING SYSTEM DIAGRAMS 2 46 1 Oil water pump assembly 2 Radiator 3 Radiator fan 4 Thermostat 5 Oil cooler ...
Страница 84: ...COOLING SYSTEM DIAGRAMS 2 47 ...
Страница 85: ...COOLING SYSTEM DIAGRAMS 2 48 1 Radiator cap 2 Radiator 3 Radiator fan 4 Oil cooler ...
Страница 86: ...CABLE ROUTING 2 49 EAS20430 CABLE ROUTING ...
Страница 88: ...CABLE ROUTING 2 51 ...
Страница 90: ...CABLE ROUTING 2 53 ...
Страница 92: ...CABLE ROUTING 2 55 ...
Страница 94: ...CABLE ROUTING 2 57 ...
Страница 96: ...CABLE ROUTING 2 59 ...
Страница 98: ...CABLE ROUTING 2 61 ...
Страница 100: ...CABLE ROUTING 2 63 ...
Страница 102: ...CABLE ROUTING 2 65 ...
Страница 104: ...CABLE ROUTING 2 67 ...
Страница 106: ...CABLE ROUTING 2 69 ...
Страница 108: ...CABLE ROUTING 2 71 ...
Страница 110: ...CABLE ROUTING 2 73 ...
Страница 113: ......
Страница 148: ...PERIODIC MAINTENANCE 3 35 ...
Страница 253: ...ENGINE REMOVAL 5 12 Installed depth of gasket c 3 5 mm 0 14 in ...
Страница 280: ...GENERATOR 5 39 4 Apply Sealant onto the stator coil lead grommet 1 Yamaha bond No 1215 Three Bond No 1215 90890 85505 ...
Страница 286: ...PICKUP ROTOR 5 45 Yamaha bond No 1215 Three Bond No 1215 90890 85505 ...
Страница 291: ...ELECTRIC STARTER 5 50 ...
Страница 340: ...TRANSMISSION 5 99 ...
Страница 356: ...WATER PUMP 6 15 ...
Страница 378: ...AIR INDUCTION SYSTEM 7 21 EAS27040 AIR INDUCTION SYSTEM ...
Страница 384: ...AIR INDUCTION SYSTEM 7 27 ...
Страница 387: ......
Страница 388: ...IGNITION SYSTEM 8 1 EAS27090 IGNITION SYSTEM EAS27110 CIRCUIT DIAGRAM ...
Страница 394: ...ELECTRIC STARTING SYSTEM 8 7 EAS27160 ELECTRIC STARTING SYSTEM EAS27170 CIRCUIT DIAGRAM ...
Страница 400: ...CHARGING SYSTEM 8 13 EAS27200 CHARGING SYSTEM EAS27210 CIRCUIT DIAGRAM ...
Страница 401: ...CHARGING SYSTEM 8 14 2 AC magneto 3 Rectifier regulator 4 Main fuse 7 Battery 95 Engine ground 96 Battery negative lead ...
Страница 403: ...CHARGING SYSTEM 8 16 ...
Страница 404: ...LIGHTING SYSTEM 8 17 EAS27240 LIGHTING SYSTEM EAS27250 CIRCUIT DIAGRAM ...
Страница 408: ...SIGNALING SYSTEM 8 21 EAS27270 SIGNALING SYSTEM EAS27280 CIRCUIT DIAGRAM ...
Страница 415: ...SIGNALING SYSTEM 8 28 ...
Страница 416: ...COOLING SYSTEM 8 29 EAS27300 COOLING SYSTEM EAS27310 CIRCUIT DIAGRAM ...
Страница 419: ...COOLING SYSTEM 8 32 ...
Страница 420: ...FUEL INJECTION SYSTEM 8 33 EAS27330 FUEL INJECTION SYSTEM EAS27340 CIRCUIT DIAGRAM ...
Страница 484: ...FUEL PUMP SYSTEM 8 97 EAS27550 FUEL PUMP SYSTEM EAS27560 CIRCUIT DIAGRAM ...
Страница 488: ...ELECTRICAL COMPONENTS 8 101 EAS27972 ELECTRICAL COMPONENTS ...
Страница 490: ...ELECTRICAL COMPONENTS 8 103 ...
Страница 492: ...ELECTRICAL COMPONENTS 8 105 EAS27980 CHECKING THE SWITCHES ...
Страница 516: ...ELECTRICAL COMPONENTS 8 129 ...
Страница 523: ......
Страница 524: ...YAMAHA MOTOR CO LTD 2500 SHINGAI IWATA SHIZUOKA JAPAN ...
Страница 525: ...WIRING DIAGRAM YZFR1Y C ...
Страница 526: ...WIRING DIAGRAM YZFR1Y C ...