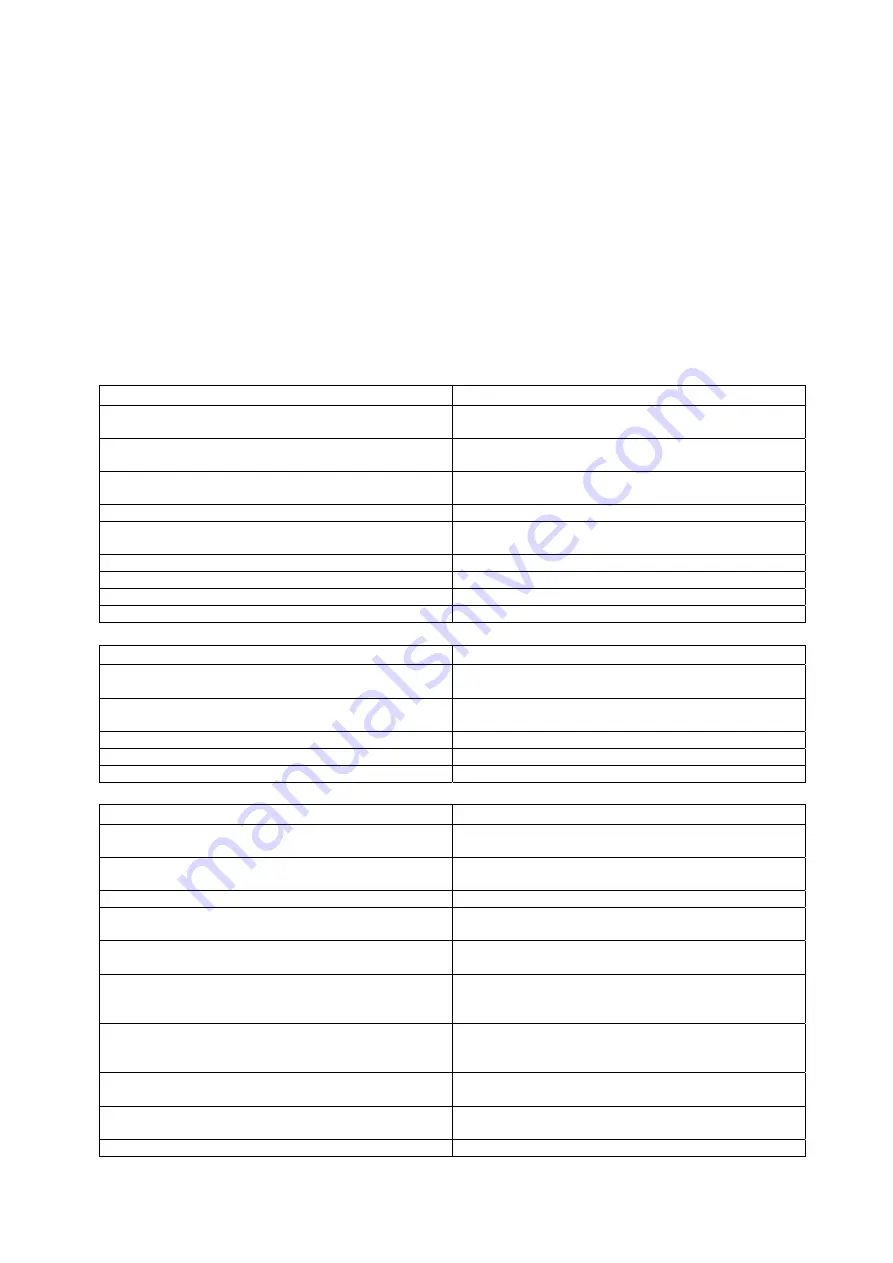
18
7. Daily check
• Before starting pump operation, be sure to conduct the following check every day. If any irregularity is
found, do NOT start running the pump until the cause of the irregularity has been found and corrective
measures have been taken.
a) Verify the drain flow through the air filter.
b) In case using a lubricator, verify the quantity of lubricating oil.
c) Make sure that there is no leakage of fluid from any connection part or the pump.
d) Make sure that there are no cracks in the pump casing or piping.
e)
Check the tightness of every bolt of the pump and retighten if necessary. For details, see the
maintenance manual.
f) Make sure that the connection parts of the piping and peripheral equipment are not loose.
g) Make sure that each consumable parts of the pump has not been inspected or replaced. For details, see
the maintenance manual.
8. Troubleshooting
8.1 Pump does not run
Cause
Action to be taken
The exhaust port (silencer) of pump is clogged with
sludge.
Check and clean the exhaust port and silencer.
Air is not supplied.
Start the compressor, and open the air valve and
air regulator.
The supply air pressure is low.
Check the compressor and the configuration of air
piping.
Air leaks from connection parts.
Check the connection parts and tightness of bolts.
Air piping or peripheral equipment is clogged with
sludge.
Check and clean the air piping.
The flow valve on the discharge side is not open.
Open the flow valve on the discharge side.
The spool stopped in neutral position.
Press the RESET button.
The fluid piping is clogged with sludge.
Check and clean the fluid piping.
The pump is clogged with sludge.
Disassemble the casing, check and clean.
8.2 Pump runs, but fluid does not come out
Cause
Action to be taken
The suction lift or discharge head is long.
Confirm the piping configuration and shorten the
length.
The discharge-side fluid piping (including the
strainer) is clogged with sludge.
Check and clean the fluid piping.
The valve on the suction side is not open.
Open the valve on the suction side.
The pump is clogged with sludge.
Disassemble the casing, check and clean.
The ball and valve seat are worn out or damaged.
Disassemble the manifold, check and replace parts.
8.3 Flow (discharge volume) decreased
Cause
Action to be taken
The supply air pressure is low.
Check the compressor and configuration of air
piping.
Air piping or peripheral equipment is clogged with
sludge.
Check and clean the air piping.
The discharge-side flow valve opens differently.
Adjust the discharge-side flow valve.
Air is taken in together with fluid.
Replenish fluid and check the configuration of the
suction-side piping.
Cavitation occurs.
Adjust the supply air pressure and discharge
pressure, and shorten the suction lift.
Chattering occurs.
Adjust the supply air pressure and discharge
pressure. Reduce inlet flow valve to adjusting
liquid pressure and volume.
Icing on air-switching portion.
Eliminate ice from air-switching valve and check
and clean the air filter. Use external exhaust hose
to control exhaust air speed. (Refer Fig.3.2)
The fluid piping (including the strainer) is clogged
with sludge.
Check and clean the fluid piping and strainer.
The exhaust port (silencer) of the pump is clogged
with sludge.
Check and clean the exhaust port and silencer.
The pump is clogged with sludge.
Disassemble the casing, check and clean.