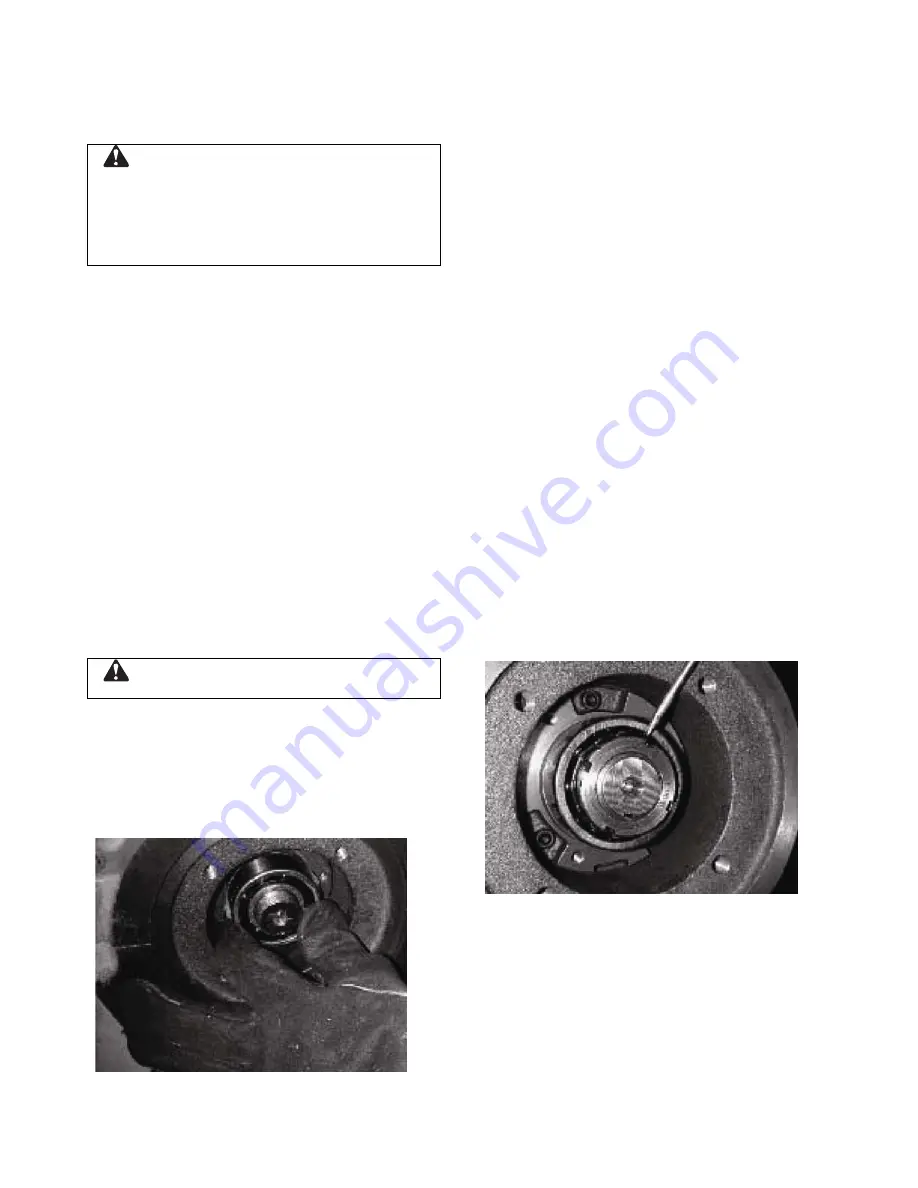
23
vegetable oil, or equal and slide the
mechanical seal head onto the shaft. Do not
compress the seal spring at this time.
CAUTION
Use a flashlight and make sure the mechanical
seal spring is seated properly into the spring
holder and around the bellows of the mechanical
seal before continuing.
5. Slide the gland plate, over the shaft, being
very careful that the head and the seat of the
mechanical seal do not get damaged. Then
press the gland plate with the O-ring into the
stuffing box and tighten the socket-head
capscrews.
NOTE:
Because of the compression of the O-ring,
it may be difficult to press the O-ring into the
stuffing box. Use longer socket-head capscrews to
start the gland plate into the stuffing box. Draw-up
the bolts evenly until the gland plate is secure in
the stuffing box. To prevent the mechanical seal
spring from pushing the gland plate back out of the
stuffing box, remove one long socket-head
capscrew at a time and replace with a regular
sockethead capscrew.
6. Heat the ball bearings using dry heat or 10% –
15% soluble oil and water, or an induction
heater.
CAUTION: Do not exceed a temperature
of 275°F.
7. Fill up the lip seal cavity with approximately
.50 ounces of grease.
8. Using gloves, slide the heated bearing onto
the shaft against the shaft shoulder. See
Figure 19.
Figure 19: Installing Bearing
9. Install the locknut and lockwasher on the
outboard end of the shaft. Make certain that
the locknut is secure and bend over the tabs
on the lockwasher. See Figure 20.
10. Allow the bearing to cool to room temperature.
Coat the exposed sides of the bearing with
two or three ounces of recommended grease.
Drive as much grease as possible into the
bearing using a putty knife or similar tool.
11. Remove the grease relief plug; coat the inside
of the bearing housing with grease, and then
slide the housing into place over the bearing.
Alternately tighten the bearing housing
capscrews so as not to “cock” the bearing
housing causing bearing to bind. Leave the
grease relief plug out of the outboard housing
until the pump is run for a minimum of two
hours and the system has reached its normal
operating temperature.
NOTE:
A locknut and lockwasher are not installed
on the inboard end of the pump shaft. It is
acceptable to leave the grease relief plug installed
on the inboard side for Step 11.
12. Repeat steps 1 through 11 for the inboard.
13. Reinstall the coupler, check for alignment, and
install the coupler guard. See the sections
entitled Alignment Procedure and ANSI/OSHA
Coupler Guard Removal/Installation.
Figure 20: Installing Lockwasher and Locknut
Содержание GOULDS AC8743
Страница 2: ......
Страница 3: ......
Страница 11: ......
Страница 22: ...20 SERVICE Figure 13 Mechanical View...