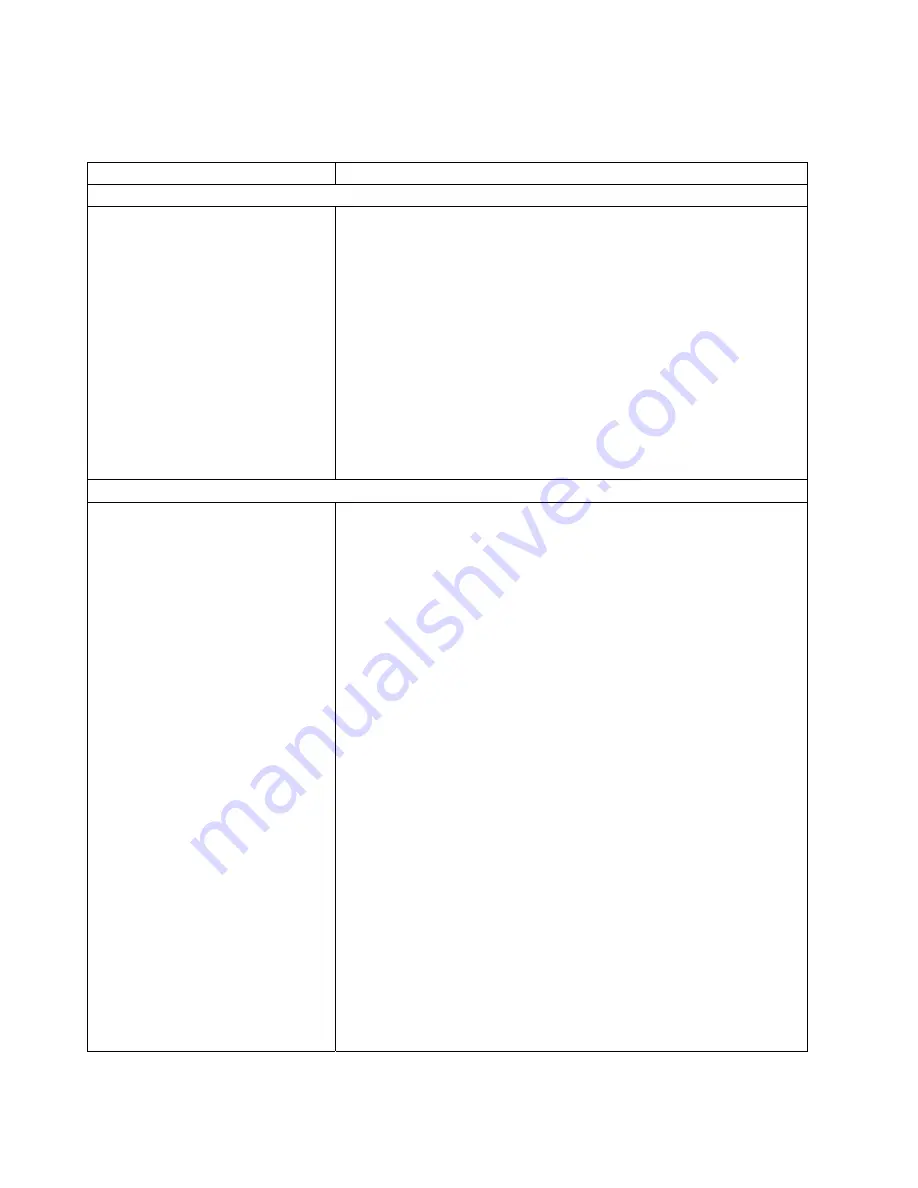
16
TROUBLESHOOTING
Between regular maintenance inspections, be alert for signs of motor or pump trouble. Common symptoms
are listed below. Correct any trouble immediately and AVOID COSTLY REPAIR AND SHUTDOWN.
CAUSES
CURES
No Liquid Delivered
1. Lack of prime
Fill pump and suction pipe completely with liquid.
2. Loss of prime
Check for leaks in suction pipe joints and fittings; vent casing to
remove accumulated air.
3. Suction lift too high
If no obstruction at inlet, check for pipe friction losses. However,
static lift may be too great. Measure with mercury column or vacuum
gauge while pump operates. If static lift is too high, liquid to be
pumped must be raised or pump lowered.
4. Discharge head too high
Check pipe friction losses. Large piping may correct condition.
Check that valves are wide open.
5. Speed too low
Check whether motor is directly across-the-line and receiving full
voltage. Or frequency may be too low; motor may have an open
phase.
6. Wrong direction of rotation
Check motor rotation with directional arrow on pump casing.
7. Impeller completely plugged
Dismantle pump and clean impeller.
Not Enough Liquid Delivered
8. Air leaks in suction piping
If liquid pumped is water or other non-explosive, and explosive gas
or dust is not present, test flanges for leakage with flame or match,
or by plugging inlet and putting line under pressure. A gauge will
indicate a leak with a drop of pressure.
9. Speed too low
See item 5.
10. Discharge head too high
See item 4.
11. Suction lift too high
See item 3.
12. Impeller partially plugged
See item 7.
13. Cavitation; insufficient NPSH
(depending on installation)
a. Increase positive suction head on pump by lowering pump.
b. Sub-cool suction piping at inlet to lower entering liquid
temperature.
c. Pressurization suction vessel.
14. Defective impeller
Inspect impeller, bearings and shaft. Replace if damaged or vane
sections badly eroded.
15. Foot valve too small or partially
obstructed
Area through ports of valve should be at least as large as area of
suction pipe – preferably 1-1/2 times. If strainer is used, net clear
area should be 3 to 4 times area of suction pipe.
16. Suction inlet not immersed
deeply enough
If inlet cannot be lowered, or if eddies through which air is sucked
persist when it is lowered, chain a board to suction pipe. It will be
drawn into eddies, smothering the vortex.
17. Wrong direction of rotation
Symptoms are an overloaded drive and about 1/3 rated capacity
from pump. Compare the rotation of the motor with the directional
arrow on the pump casing.
18. Too small impeller diameter
(probable cause if none of the
above)
Check with the factory to see if a larger impeller can be used;
otherwise, cut the pipe losses or increase the speed, or both as
needed. Be careful not to overload the driver.
19. Air leaks in suction piping
See item 8.
Содержание GOULDS AC8743
Страница 2: ......
Страница 3: ......
Страница 11: ......
Страница 22: ...20 SERVICE Figure 13 Mechanical View...