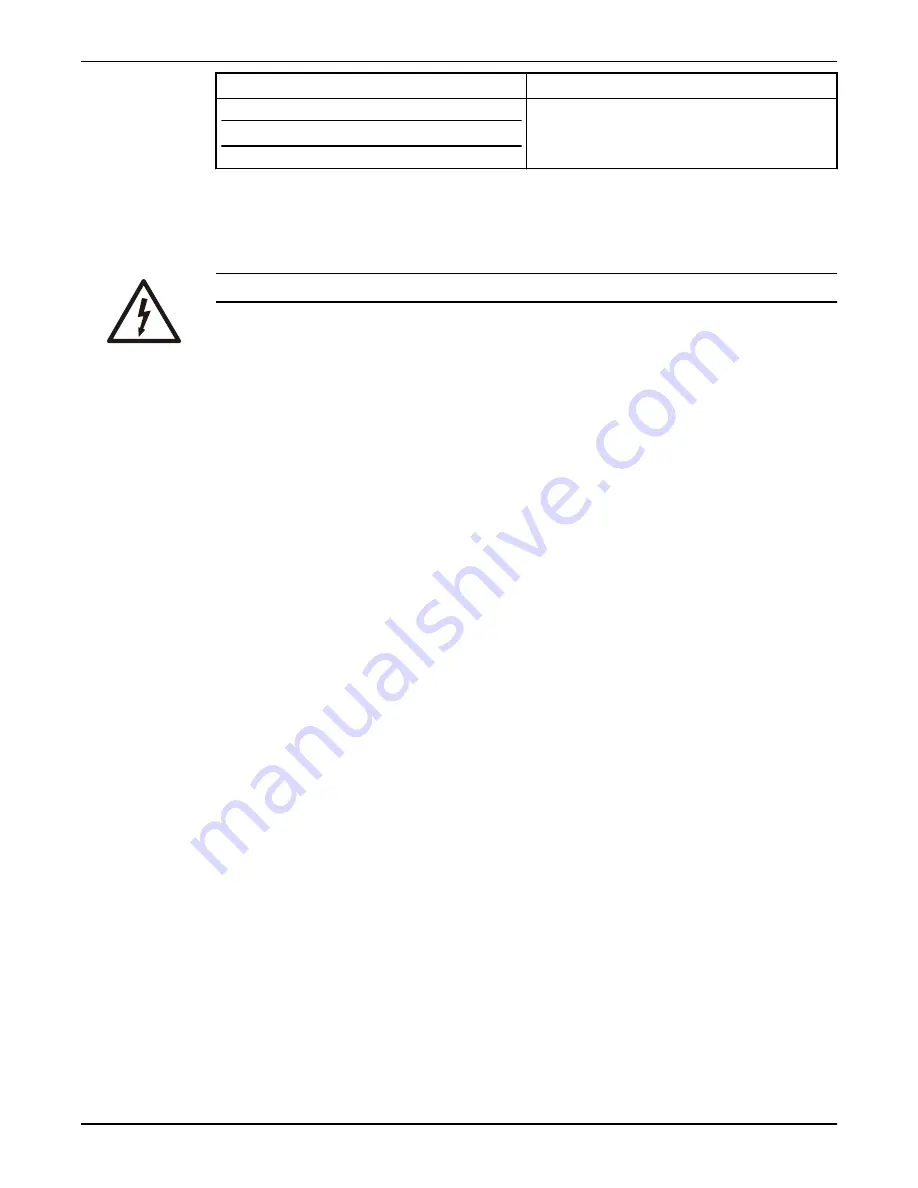
Hazard level
Indication
NOTICE:
• A potential situation which, if not avoided, could
result in undesirable conditions
• A practice not related to personal injury
Hazard categories
Hazard categories can either fall under hazard levels or let specific symbols replace the
ordinary hazard level symbols.
Electrical hazards are indicated by the following specific symbol:
Electrical Hazard:
These are examples of other categories that can occur. They fall under the ordinary hazard
levels and may use complementing symbols:
• Crush hazard
• Cutting hazard
• Arc flash hazard
Product warranty
Coverage
Xylem undertakes to remedy defects in products from Xylem under these conditions:
• The faults are due to defects in design, materials, or workmanship.
• The faults are reported to an Xylem representative within the warranty period.
• The product is used only under the conditions described in this manual.
• The monitoring equipment incorporated in the product is correctly connected and in
use.
• All service and repair work is done by Xylem-authorized personnel.
• Genuine Xylem parts are used.
• Only Ex-approved spare parts and accessories authorized by Xylem are used in Ex-
approved products.
Limitations
The warranty does not cover defects caused by these situations:
• Deficient maintenance
• Improper installation
• Modifications or changes to the product and installation made without consulting
Xylem
• Incorrectly executed repair work
• Normal wear and tear
Xylem assumes no liability for these situations:
• Bodily injuries
• Material damages
• Economic losses
Warranty claim
Xylem products are high-quality products with expected reliable operation and long life.
However, should the need arise for a warranty claim, then contact your Xylem
representative.
Introduction and Safety
4
Flygt 2250 Installation, Operation, and Maintenance Manual
Содержание Flygt 2250
Страница 1: ...Flygt 2250 Installation Operation and Maintenance Manual ...
Страница 2: ......
Страница 41: ......